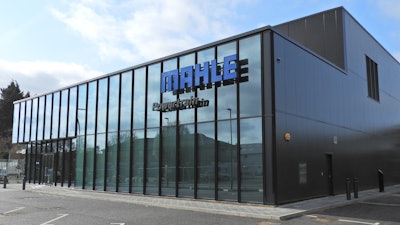
Engineering services specialist MAHLE Powertrain has helped a major vehicle manufacturer to overcome testing challenges posed by travel restrictions during the Covid crisis. Under strict Covid precautions, utilization of the hypobaric and climatic capability of the company’s Real Driving Emissions (RDE) Centre in Northampton, UK, has enabled the replication of real-world drive cycles without the requirement for global travel normally associated with altitude testing. This has mitigated risk and significantly reduced testing time and cost when compared to traditional methods and, believes MAHLE Powertrain, could result in a permanent change in the way testing is approached.
“Travel restrictions had the potential to generate a significant backlog in testing – MAHLE managed to not only avoid delays during delivery of a program for a major vehicle manufacturer, but devised a more streamlined, cost-effective test schedule that could be completed faster than normally anticipated,” explains Thomas Brooks, MAHLE Powertrain’s head of calibration. “We think it’s the first example of a manufacturer completing an RDE test program, including at altitude, in the UK.”
Through strategic use of the chamber testing facilities at the RDE Centre, MAHLE and its customer have managed to turn a potentially delaying, costly challenge into a production advantage. Replicating whole drive cycles in one controlled environment as opposed to shipping vehicles, engineers and associated hardware around the globe – even in a Covid-free world – makes a compelling commercial and engineering case. Brooks notes that, based upon MAHLE Powertrain’s own experience, engineer time combined with travel and subsistence costs can very quickly reach significant sums even for relatively modest test programs.
MAHLE Powertrain
The main advantage of MAHLE Powertrain’s facility is the ability to test in a precisely controlled environment that can replicate any necessary test condition. This includes aggressive climbs on a 4WD chassis dyno up to 5,000 m with relevant barometric pressures, variable road gradients at temperatures between -40 and 50 C, and humidity levels of between 10 and 80%.
“The vehicle manufacturer carried out eight mountain test runs over a 3-day period which would normally take 9-10 days plus travel and engineer time - with no guarantee of the stable conditions necessary for good test data,” continues Brooks. “This test program provided a guarantee of safety, not only from Covid but from day-to-day road incidents and crucially, repeatability. There are a number of factors to consider when extending physical location testing, such as logistics, accommodation, engineer time and vehicle shipping. It is much easier to simply book another day of test chamber time. This could mark the start of a real shift in the way powertrain test programs are planned.”
MAHLE Powertrain has worked with most major vehicle manufacturers to carry out testing and sees the use of dynamic test programs as a key factor in accelerating the time to market of new vehicles and technologies. In a time-contracted automotive industry, MAHLE Powertrain believes this provides a significant competitive advantage combined with reduced cost.
In the face of growing demand, MAHLE Powertrain is already building an additional climatic chamber, which will be ready for utilization by vehicle manufacturers in early 2022.