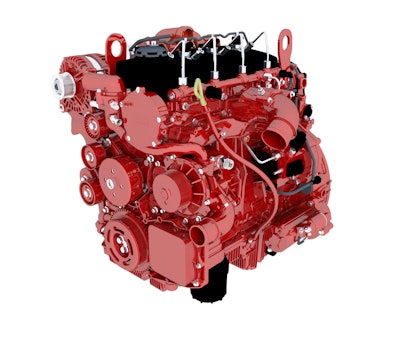
For Tier 4 Final you will really need to study available diesel engine technologies and determine which best fits your application. There is no one solution that fits all applications. Engine size and application will heavily influence the best technology choice. The good news is these engines deliver increased customer value.
There is no single technology that enables an engine to meet the stringent emissions standards. Rather it is a complex combination of proven strategies such as in-cylinder combustion optimization, turbocharging, high-pressure fuel injection with multiple events per cycle, diesel oxidation catalysts and diesel particulate filters. Either all or some of these strategies can be combined to achieve the desired results.
One of the biggest changes for Tier 4 Final is the availability of engines without diesel particulate filters in some engine makes and sizes. It is also noteworthy that some smaller engines will not need cooled exhaust gas recirculation (EGR) or selective catalytic reduction (SCR). You need to do your research to find out which options are available in any given engine range and if there are any trade-offs in your particular application.
One of the enabling technologies that help reduce particulate matter, in addition to combustion chamber design, is high-pressure common rail fuel injection. “Higher rail pressure reduces particulate matter emissions from the cylinder so there is no need for a particulate filter,” says Tommy Sjöberg, Product Sales Manager at Scania (company information, 10056056), based in Sweden. “Without a DPF there is no downtime needed for maintenance or cleaning (regeneration). Since there is no downtime, this allows for higher productivity.”
The performance of a diesel engine is heavily influenced by its fuel injection design. How you deliver the fuel impacts performance, emissions and noise. In the recent past unit fuel pumps fed unit injectors at pressures. But now modern common rail diesels feature piezoelectric injectors for increased precision. You can program multiple injection events per cycle with both pre- and post-injection events. It wasn’t uncommon in the not too distant past to witness fuel injection pressures from rotary fuel injection pumps in the neighborhood of 6,000 to 8,000 psi. Now pressures can reach into the mid-30,000psi range.
“High-pressure common-rail fuel injection results in better atomization and mixing of fuel, which reduces Nitrogen oxides (NOx), particulate matter (PM) and hydrocarbons (HC),” notes Chris Giogianni, Vice President – Product, JCB North America, (company information, 10055648), Pooler, GA.
There is also more latitude with injection timing with common rail fuel systems. “The high-pressure common-rail (HPCR) fuel system provides constant control over fuel injection variables such as pressure, timing, duration and multiple injections,” says Doug Laudick, Product Planning Manager at John Deere Power Systems (company information, 10056373), Waterloo, IA. “The HPCR fuel system has higher injection pressures, resulting in more efficient combustion, which in turn leads to a reduction in particulate matter (PM).”
But the common rail fuel system is only one part of the solution. “The HPCR fuel system by itself does not enable the removal of the diesel particulate filter (DPF),” Laudick explains. “Removal of the DPF requires a combination of HPCR, optimized combustion system design, associated changes in engine calibration and other factors.”
We are now seeing fuel injection pressure we would not have thought possible a decade ago. “Fuel injection pressures today are capable of reaching 36,000 psi under full-load conditions,” says Laudick. “Injection pressures could go higher in the future and mandate the need for stronger materials to maintain or improve upon current durability goals.”
Manufacturers have maintained system durability in the face of the rising pressures. “There are no trade-offs between fuel injection pressure and fuel injector durability because we continue to design for the same or better durability compared to previous tiers,” says Laudick. “We use materials that allow us to maintain or improve upon our durability goals despite increased fuel injection pressures.”
But fuel quality and cleanliness do become more critical at the higher fuel injection pressures. “The higher-pressure fuel systems featured on Tier 4 engines make it critical to utilize high-quality fuel and fuel filtration,” says Laudick. “John Deere recommends the use of diesel fuel specified to EN or ASTM standards and our 10/2 micron filtration system consisting of a 10-micron primary fuel filter and a 2-micron final filter.”
These systems require the ultra-low sulfur diesel (ULSD) that is mandated in North America. “Further, owners should take care of their fuel dispensing systems, as a small investment up front can eliminate costly repairs down the road,” says Giorgianni. But there should be no concerns if the fuel meets the standards and is kept clean. “Our fuel injection system is designed to withstand these increased pressures.”
John Deere uses building block approach
“John Deere will continue its planned building-block approach to meet Final Tier 4/Stage IV emissions regulations,” says Laudick. “To achieve regulatory compliance, John Deere developed the Integrated Emissions Control system – a solution that optimizes engine performance, operating efficiency and long-term durability. The Integrated Emissions Control System encompasses any combination of aftertreatment emissions-reductions components designed and integrated by John Deere engineering to meet the most demanding customer requirements.”
“John Deere continues to use the best combination of available technologies to meet emissions regulations and customer needs in each power range,” claims Laudick. “For the 48- to 74-net hp power range, John Deere will offer models using an exhaust filter that contains a DOC/DPF without the need for cooled EGR or SCR. Engine models greater than 75 hp will feature an Integrated Emissions Control system consisting of cooled EGR, a DOC/DPF and SCR. All John Deere Integrated Emissions Control systems are specifically designed to meet the demands of off-highway applications.”
Laudick adds, “We will continue to tailor our Final Tier 4/Stage IV engine solutions to fit the variety of off-highway applications while minimizing the regulatory impact on our customers. The Integrated Emissions Control system allows John Deere to tailor its technology approach to Final Tier 4/Stage IV regulations, and deliver emissions compliance without sacrificing power, performance, ease of operation, fluid efficiency, reliability, durability or economical operating cost.”
With Tier 4 technology John Deere is focused on total fluid economy. “Total fluid economy takes into account total fluid consumption, including diesel fuel and additional fluids such as DEF (diesel exhaust fluid),” says Laudick. “Fuel consumption with John Deere Tier 4/Stage IV engines will be 1 to 4% lower than our Interim Tier 4/Stage IIIB engine models. The Integrated Emissions Control system consisting of cooled EGR, a DOC/DPF and SCR will allow our Final Tier 4/Stage IV engines to meet emissions requirements while utilizing less DEF. DEF consumption with John Deere Final Tier 4/Stage IV engines will be 1 to 3% of diesel fuel consumption depending upon the application.”
Laudick adds, “Lower DEF consumption means the DEF tank size can be smaller – minimizing the impact on vehicle applications while extending DEF filter service intervals and reducing operator involvement. Increased pressures created by John Deere Final Tier 4/Stage IV high-pressure fuel systems will reduce engine-out PM and extend intervals between active exhaust filter regeneration.”
Scania draws from on-road expertise
“Scania’s long-standing experience of EGR and SCR from trucks and buses has meant that these developments could be applied to Scania industrial engines as well,” says Sjöberg. “Scania industrial engines will manage Stage IV and Tier 4 final without a particulate filter. With only EGR and SCR technology, the installation will be unaffected.”
Combustion efficiency is a core focus for Scania. “In the course of researching various single-cylinder engines of different displacements, it has become apparent that cubic capacity itself is a critical factor,” says Sjöberg. “Quite simply, the potential for optimization – excellent fuel economy, low emissions and generous torque – is at its greatest when the physical dimensions of the bore and stroke are within certain critical limits. This has led to the development of the Scania modular combustion concept.
“All Scania engines are based on this advanced concept,” says Sjöberg. “These engines have identical combustion chambers and also share components such as pushrods, valve gear, roller tappets and piston rings. This makes them not only efficient, but also exceedingly simple to maintain and repair.
“The choice of different aftertreatment technologies is a trade-off between a number of different parameters such as performance, efficiency and reliability,” notes Sjöberg. “But the foundation in our solution is our ‘know how’ in base engine combustion technology.”
High-pressure fuel injection increases performance and efficiency. “With Scania XPI (extra-high pressure injection), fuel delivery and injection pressure can be set independently of engine speed, with exceptional precision,” says Sjöberg. “This sophisticated system adjusts continually to adapt to changing speeds and situations, so you can get the most of every drop of diesel. It uses a number of precisely timed fuel injections to enhance performance and economy – while reducing harmful emissions – through every cycle.”
“Every vital aspect, from air temperature, fuel injection settings to exhaust aftertreatment, is controlled by the Scania EMS (engine management system),” says Sjöberg. “And with up to 34,800 psi injection pressure, the Scania XPI injection system contributes to low particulate emissions and exceptional torque capabilities.”
MTU and C&I engines don’t use DPF
At MINExpo 2012 , the Tognum Group (company information, 10656608), Friedrichshafen, Germany, a global supplier of engines and propulsion systems and distributed power generation systems, showcased its MTU-brand C&I engines designed to meet Tier 4 Final emissions regulations.
The Series 1000, 1100, 1300 and 1500 engines will use SCR exhaust aftertreatment technology to achieve compliance with limits set for NOx and particulate emissions. No DPF is required to achieve further particulate reduction.
The new engines will cover the 750 hp and below power range, offering outputs ranging from 134 to 617 hp. According to Tognum, they will provide up to 5% reductions in fuel consumption, up to a 20% increase in service life, higher torque at low engine speeds, greater engine brake power and fast, straightforward maintenance.
Series 1600 C&I engines — which meet Tier 4 Final regulations without either SCR systems or DPFs — will be introduced to extend the range to 980 hp. The engines will incorporate in-engine EGR technology, along with high-pressure common rail injection, two-stage turbocharging and cooled EGR. Particular emphasis has been placed on optimizing the combustion process in order to minimize fuel consumption.
Series 2000 and Series 4000 engines above 750 bhp will meet Tier 4 Final standards with no aftertreatment or DPF required at any bhp. This will be achieved through a combination of two-stage turbocharging, EGR cooling, a new combustion system design and high-pressure common rail injection. Both series are based on proven MTU engine technology, and are designed to provide optimal transient behavior with rapid response to changes in engine load.
JCB includes recalibration option
In mid-2012, JCB formally launched its technology solution to meet Tier 4 Interim/Stage IIIB requirements. The JCB Ecomax engine achieves emissions levels through the use of its patented in-cylinder technologies, without the need for external exhaust aftertreatment or a DPF.
There are several benefits to eliminating the DPF. There is decreased downtime since there is no DPF to service or DEF tank to fill, as well as reduced servicing costs. There is increased packaging flexibility, delivering better service access and improved visibility to the work area. There is no residual heat typically associated with DPF systems and it doesn’t require the higher heat resistant lube oils typically associated with aftertreatment solutions.
Using a patent-pending combustion process design, the company combines injection pressures of 29,000 psi in the common rail system with a variable geometry turbocharger (VGT) for rapid response at low rpm to create a cleaner, more efficient burn. Cooled EGR is used to further reduce emissions, passing a small amount of the exhaust gas back through the engine to cool the combustion process and reduce NOx within the cylinder.
Upgraded fuel and air filters will ensure cleanliness of the fuel going into the engines, plus a 5-micron water separator and fuel filter for the fuel supply line will supplement the 2-micron engine filter. A crankcase ventilation filter is also required. However, the engines will be able to run on standard engine oils, helping to reduce owning and operating cost.
The Tier 4 Interim engines will have the same 500-hour service intervals as the previous models. It’s estimated that there will be an increase of $0.05/hour over a typical 6,000-hour ownership period for a backhoe-loader, an amount that should be offset by fuel economy and productivity benefits.
“With the JCB engine, it is a combination of patent pending in-cylinder technologies, the high-pressure common rail system and the variable geometry turbocharger that has allowed us to maximize fuel efficiency,” says Giorgianni. “Specifically with the VGT it allows control of the quantity of air entering the engine to match fuel injected and optimize combustion.”
According to JCB, its Tier 4 Interim technology also allows the company or its dealers to sell a low-cost kit to recalibrate the electronic control unit so the engine machine can be resold and operated in countries where poor quality (higher sulfur) fuels are used. The kit keeps the EGR valve closed (reducing potential sulphur damage), reduces fuel injection pressures and reduces the VGT range.
“By recalibrating the JCB Ecomax engine, turning off the EGR and reducing fuel injection pressures, it is possible for the engine to be run on higher sulphur content fuels,” says Alan Tolley, Director of Engine Programs at JCB.
Perkins optimizes SCR technology
Perkins (company information, 10055932), Peterborough, United Kingdom, unveiled its new range of four-cylinder Tier 4 Final-compliant engines in the Spring of 2012. The new models all incorporate the company’s specially optimized SCR technology.
The 1204F 4.4-liter, four-cylinder aftercooled engine is offered in a choice of two versions. The single turbo aftercooled 1204F-E44TA produces 147 hp, delivering improved fuel economy while offering great power and torque. The twin turbo, aftercooled 1204F-E44TTA has power ratings up to 175 hp and employs twin turbochargers mounted in series for extra power density, low-speed torque and faster transient response.
Both 1204F models use aftertreatment comprising DOC/SCR modules. This compact solution not only achieves the significant reduction of NOx required, it also removes the need for any regeneration strategy for soot, since the formulation of particulate emissions is prevented in the combustion process. The small size of the DOC/SCR module means it can be mounted in a variety of remote locations, freeing up valuable space in the engine bay.
“We have used the arrival of SCR technology to our customers’ advantage,” states Daniel Clayton, Perkins Tier 4 Product Marketing Manager. “By offering a no-DPF option, we have given them unrivalled flexibility as to how they wish to configure their machines. What is certain is that machine performance will in no way be compromised.”
Perkins does offer the option of a service-free DPF aftertreatment unit to meet specific OEM requirements.
Many of the improvements made for Tier 4 Interim have been carried over into the new engine range, such as improved power density, improved transient response and competitive fluid consumption. For engines from 3.4 to 7.1 liters, Perkins has tailored SRC systems that maximize customer benefits.