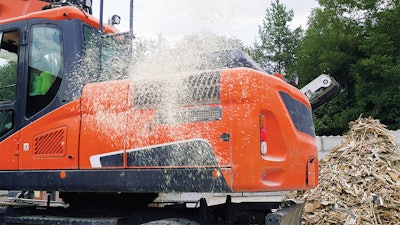
*This content is sponsored by CLEANFIX North America Ltd.*
Maximize Benefits, Minimize Investment
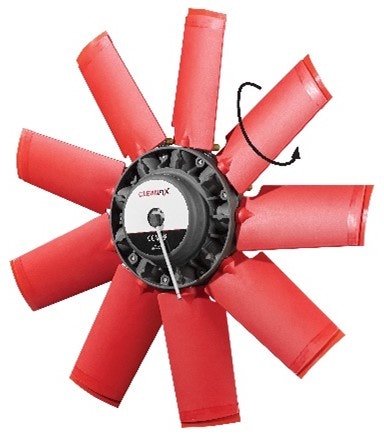
Through the evolution of diesel emissions regulations, countless hours and dollars have been invested in optimizing the design of cooling packages to balance performance, physical size, and serviceability. A high performing cooler will have a trade-off in serviceability, an easy to clean cooler will be too large for the application, a smaller cooler will not meet the heat rejection requirements… a vicious circle. Add now to the mix the introduction of automated machine operation, where a clogged cooler is now possibly hours of down-time and (lost revenue!) to have a person travel to the machine for service.
Evolution of Reversing Fans
The traditional solution to some of these issues is to use a hydraulic reversing cooling fan. These systems have proven to be durable and somewhat effective in keeping coolers clean and machines running efficiently, but only somewhat.
The reversing of the fan rotation does reverse the flow of air through the core, but at only a fraction of the efficiency with which the fan cools. The net result is a severe reduction in cooling performance during the relatively long cleaning cycle. The hydraulic drive system is effective to allow for fan reversal but also comes with a compounding factor of inefficient cleaning and hydraulic system losses.
These are the compromises once the machine is in the customer’s hands; there are many more that affect the entire manufacturing process. First is cost; hydraulic drive systems are very reliable, but the combination of pumps/motors/hoses/adapters soon adds up in product costs. Second is part count; the typical hydraulic fan drive system can introduce up to 5x more parts to the fan drive alone. These additional components require sourcing, logistics for delivery, floor-space within the manufacturing organization, and labor to assemble. Third is complexity; with each component added the fan drive system, another line is added to the FMEA (not including control strategy programming!).
Revolutionary Design for Optimal Cooling Efficiency
A unique solution is available to address these considerations; the Cleanfix® fan. The Cleanfix® fan is not a reversing fan; it is an engine mounted, belt driven fan that fully reverses the blade direction on command while the fan continues to spin in the same direction. This allows for the air flow to reverse direction (at any engine speed or power level) and produce the same pressure and flow characteristics for cleaning the coolers as was designed for cooling. This same technology can be applied to vary the attack angle of the blades, matching fan power to the cooling requirements.
This operating principle also brings advantages over the most advanced viscous clutch fan drives as well. Cleanfix® fans are direct driven from the belt drive, eliminating the slip-losses associated with a viscous clutch.
The effect of Autonomy
Cooling system maintenance has always been at the very best a begrudging experience. The main initiator being the machine operator; either a warning light or buzzer is active, or the cabin air conditioning unit ceases to function due to a clogged condenser. In either case it is a sensory input to the operator which initiates the dirty job of cleaning the cores.
With the rapid adoption of autonomous control, those sensory inputs are replaced with electronic monitoring and telematic systems. With all the advantages that this brings; the absence of an operator also means that there is no longer on-site maintenance at hand. The prospect of a simple blow-out of the cooling system being possibly hours away eats into the payback proposal that autonomous operation presents.
A Cleanfix® self-cleaning fan system removes this concern by automatically cleaning the cooling system on a pre-determined schedule. Even if the cleaning interval is in the hours, the time savings of the person attending to the regular fuel and lubricant needs of the machine are quite measurable when avoiding cooler clean out.
Smaller Cooling Packages, Constant Cooling Performance
A scheduled, automatic clean out cycle combined with the availability of high power cleaning can have a direct correlation to overall cooling package size. Without the worry of trash loading on the cooler face, or dust loading in the fins, a tighter fin spacing and/or more aggressive fin profiles can be used than with other fan drive technologies.
An additional benefit of the Cleanfix® fan system is that there is very little loss in cooling performance during the self-cleaning cycle. Hydraulic fan drives must reduce fan speed to zero, then reverse the fan direction (to operate in an inefficient manner) to achieve the cleaning cycle. During this time there is a marked decrease in cooling system performance, leading to potential heating issues in high power / high ambient temperature applications. With the quick action of the Cleanfix® blade reversal, there is nearly zero time with no air flow. The patented blade articulation also ensures the same fan performance during the cleaning cycle as in the normal cooling position. These features combine for seamless operation, regardless of engine load or ambient temperature.
Cost-Effective Integration with Minimal Maintenance
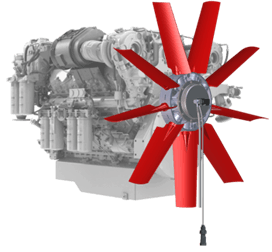
Integrating Cleanfix® fans into a cooling system design offers considerable cost advantages. Unlike hydraulic systems that involve expensive components and complex installations, Cleanfix® fans are simple to install and require minimal upkeep. The simplicity and low cost of integration make Cleanfix® fans an excellent solution for Off-Highway OEMs aiming to reduce the complexity and expense of their engine cooling systems.
Moreover, Cleanfix® fans lower the risk of costly downtime and repairs. With fewer moving parts and a reliable, self-contained design, the risk of failure is significantly reduced compared to other fan drive systems.
Regular Radiator Cleaning Is Crucial for Efficiency
Maintaining clean radiators is essential for optimal cooling performance and minimizing fuel consumption. Partially plugged radiators can cause a substantial, hidden parasitic loss in engine power. Increased air restriction causes a higher fan inlet static pressure for a given air flow. To compensate for the reduced cooling capacity of a partially plugged radiator, the fan must work harder, which results in considerable energy loss.
For example, a 5-6 kW increase in parasitic loss (not uncommon) can increase fuel consumption by 1.5 to 2.0 liters per hour. Cleaning radiators frequently reduces these inefficiencies and minimizes the risk of engine damage, maximizing fuel efficiency.
- ( 6KW = 250g/kwh x 6 = 1500g/h x 0,85 kg/l = 1,8 l/h)
Comparison of Performance: Cleanfix® vs. Viscous Fan Drives
• Cleanfix® Fan: The blade angle of Cleanfix® fans can automatically adjust to accommodate varying cooling loads, eliminating slip loss and improving cooling efficiency without increasing fuel consumption.
Advanced Fan Drive Comparison
When comparing different fan drives:
• Viscous Fan Drive: The efficiency ranges from 20% to 90%, with slip losses leading to higher fuel consumption and reduced efficiency.
• Hydraulic Fan Drive: Efficiency ranges from 50% to 70%, also suffering from power losses.
• Cleanfix® Fan Drive: With belt-driven systems, Cleanfix® fans achieve an impressive efficiency range of 95% to 97%, minimizing power losses and maximizing cooling performance.
Advantages of Cleanfix® Reversible Fans
• Increased Power to the Wheels and PTO: Cleanfix® fans provide more power to the wheels and PTO by optimizing cooling system performance, overall machine efficiency.
• Lower Fuel Consumption: When the additional power is not required, the absence of slip or hydraulic loss in the fan drive system reduces fuel consumption.
• Improved Fan Efficiency: The ability to adjust the blade angle with Cleanfix®'s variable pitch system results in better cooling efficiency and less power required to drive the fan.
• Energy Savings with Hytronic: Cleanfix® Hytronic systems further enhance efficiency by offering a larger blade pitch range and lower fan speed requirements.
Conclusion: Unlock Latent Performance, Efficiency, and Uptime
Integrating Cleanfix® reversible radiator fans into your engine systems provides proven improvements in fuel efficiency, cooling performance, and overall reliability. The innovative design, simple integration, and low-maintenance operation make Cleanfix® fans a smart, cost-effective alternative to both viscous, and hydraulic fan drives. By improving engine cooling and reducing fuel consumption, Cleanfix® fans help reduce environmental impact while enhancing engine performance. Hands-free maintenance offers immediate returns in both manned and autonomous applications. It’s time to optimize your engine cooling system and embrace a solution that maximizes efficiency and performance.
Visit cleanfix.us to discover how Cleanfix® self-cleaning radiator fans can revolutionize your engine applications.