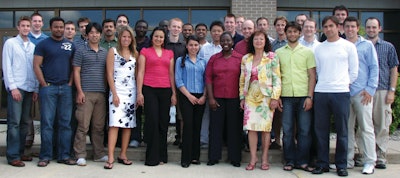
Research is essential for the progression of technology and our engineering capabilities.
The Center for Compact and Efficient Fluid Power (CCEFP) was established in June of 2006 as a National Science Foundation (NSF) Engineering Research Center (ERC). Headquartered in Minneapolis at the University of Minnesota, the center connects fluid power researchers with university faculty in an effort to fill a research void that has developed in the fluid power industry.
The CCEFP is currently engaged in over 20 research projects organized into three groups with different goals. One seeks to create more efficient fluid power technologies to reduce petroleum consumption, energy use and pollution. A second focuses on finding a more effective fluid power technology that will be cleaner, quieter and safer for its users. The third will create a more compact fluid power technology to work more cohesively with the evolving equipment landscape.
Project 1A.2
One such project is 1A.2: Optimal Power Management for Mobile Fluid using Displacement-Controlled Actuators. The project is lead by Professor Monika Ivantysynova at the Maha Fluid Power Research Center at Purdue University, West Lafayette, IN.
One of Ivantysynova's graduate students, Chris Williamson says, "The focus of the project is on machines with multiple actuators that work simultaneously, such as excavators and telehandlers."
Williamson is responsible for developing the excavator controls.
"The main source of power losses on these machines is the flow control valves," says Williamson. "Even load-sensing systems have high throttling losses when multiple cylinders and motors operate at different pressure levels. Our mini-excavator simulations are showing that more than 40% of the total engine energy is wasted in valve losses during a typical trench-digging cycle.
"The solution we propose is displacement-controlled actuation, using variable displacement pumps to control the cylinders directly. This eliminates the power losses inherent to valves and allows energy recovery as the pumps can run in motoring mode."
It will also reduce overall machine fuel consumption by avoiding throttling losses and allowing energy recovery. Path optimization and effective engine management could see additional fuel savings.
Simulation testing is finding 30-45% savings in total energy (see chart below). The team is currently building a prototype and expecting to have it running by March 1 to verify these findings.
According to the CCEFP website, "The number of professors, graduate students and research projects in hydraulic and pneumatic technology is on the rise.
"If these projects are successful, there will be tremendous improvements in components, systems and fluids.
"If not, a new generation of engineers and scientists with fluid power training will revitalize academic and industrial research in this country for years to come."
Industry members benefit
"Our members are companies, not engineers," says CCEFP Director Kim Stelson, Minneapolis. Engineers of member companies can participate actively as a Project Champions.
Members have opportunities to meet the researchers and their students, and receive regular updates on the progress of the research projects. All have royalty-free licenses to non-patented discoveries and inventions.
They also have access to CCEFP student resumes online, enabling them to identify students available for internships and those approaching graduation.
"Getting trained engineers has been a huge problem in fluid power, and we're contributing to that solution," says Stelson. "Our goal is to have every mechanical engineer, and closely related disciplines such as agricultural engineering, know what fluid power is."