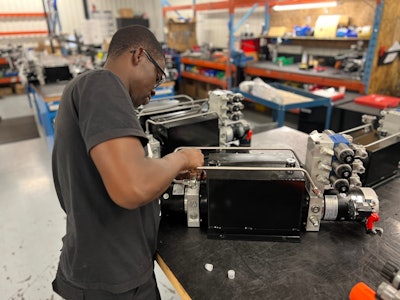
For equipment manufacturers, integrating pumps and motors with other system components is crucial for efficiency and performance. This is especially true for vehicles in the off-highway industry, which often deal with challenging and potentially dangerous conditions and are expected to endure wear and tear.
System integrators and engineers face the complex challenge of ensuring compatibility while minimizing disruptions during the integration process. Here are some best practices that can help mitigate these obstacles.
Figure 1: Most companies like Bailey also offer standard, ready-to-ship motors and pumps.Bailey Hydraulics
The importance of standardization
Standardization is crucial for smooth integration. When manufacturers follow industry standards for interfaces and connections, their products tend to work well with various components and systems. This not only simplifies integration, but also cuts down on customization, leading to more efficient operations and easier collaboration with other manufacturers. Operations benefit from standardization in two ways:
- More streamlined processes: Industry standards play a crucial role in removing uncertainty about compatibility, reducing the time and resources that would otherwise be spent developing custom solutions. By adhering to these standards, businesses can focus on innovation and efficiency, knowing their systems will seamlessly integrate with others in the industry. This not only saves costs, but also accelerates project timelines, allowing companies to deliver products and services to the market faster.
- Enhanced collaboration: A standardized approach facilitates better communication with partners and suppliers by creating a common framework that everyone can follow. This consistency helps reduce misunderstandings, align expectations, and streamline processes, leading to more efficient and productive collaborations. It also helps build stronger relationships by fostering trust and transparency.
Figure 2: Hydro Custom motors fall under one of Bailey's signature in-house brands, along with Chief, Maxim and Sure Grip Controls.Bailey Hydraulics
Modular design for flexibility
Designing modular pumps and motors is a smart way to boost flexibility. With modular parts, original equipment manufacturers (OEMs) can upgrade and replace components without having to redo the entire system. This approach not only suits different machinery setups, but also helps equipment last longer and improve productivity. For industries such as mining, having their vehicles and equipment running longer is critical
Modular design advantages include:
- Cost efficiency: Modular solutions significantly reduce the need for complete system replacements, offering a cost-effective approach. By allowing individual components to be updated or replaced as needed, these solutions enable businesses to maintain and enhance their systems with minimal disruption and expense, saving on costs and extending the existing infrastructure’s lifespan.
- Future-proofing: Easily upgradable systems help ensure operations remain at the forefront of technological advancements by allowing seamless integration of the latest software and hardware updates. This adaptability provides a competitive edge in rapidly evolving industries.
Figure 3: Bailey Engineers carefully inspect each custom product before it leaves the facility.Bailey Hydraulics
Ensure comprehensive documentation
Having detailed technical documentation is another key to successful integration. When engineers and technicians have access to all the specs, wiring diagrams, and installation guides they need, they can integrate components more effectively. Good documentation acts like a roadmap for smooth integration and helps teams troubleshoot issues that may come up, which can help get off-highway vehicles on the road faster.
Key elements of effective documentation include:
- Clarity and precision: Clear and precise documentation plays a crucial role in minimizing errors and misinterpretations. By providing comprehensive and detailed information, all parties involved can have a shared understanding of processes and instructions. This attention to detail helps reduce the likelihood of mistakes and streamlines communication within a team.
- Ease of access: Easy documentation access is crucial to ensure that all team members can quickly reference the necessary information. This saves time and helps maintain consistency across various projects and tasks. By having a centralized repository of documents, teams can reduce misunderstandings, leading to more streamlined workflows and successful outcomes.
Collaborative development practices
By teaming with component manufacturers during design, OEMs can spot and solve potential issues early. This hands-on approach sparks innovation and leads to a final product that satisfies everyone involved. Collaborative practices include:
- Joint development initiatives: Engage in strategic partnerships to co-develop solutions that enhance compatibility, allowing seamless integration and improved functionality across diverse systems. By collaborating with key industry players, companies can create innovative solutions that meet current demands and anticipate future needs.
- Open communication channels: Encourage regular dialogue between teams to address concerns and brainstorm solutions. Encourage team members to share updates, identify any challenges they face and collectively explore creative solutions. Open communication creates alignment on goals and strategies.
Rigorous testing and validation benefits
OEMs should thoroughly test and validate pumps and motors as part of the entire system before starting full-scale production. Catching and fixing compatibility issues during testing helps avoid expensive problems down the road. Comprehensive testing benefits include:
- Quality assurance: Rigorous testing helps ensure that all components work together. By thoroughly examining each part and its interactions, the team can identify and resolve potential issues, leading to a more reliable and efficient system.
- Risk mitigation: Early detection reduces the risk of operational disruptions and uncovers potential problems and addresses them before they escalate into major setbacks and downtime, which can have an adverse effect in many ways.
Figure 4: Bailey’s MVP program includes custom motors, pumps and valves.Bailey Hydraulics
Customizable interfaces and software solutions
Providing customizable interfaces or adapters is a wonderful way to address compatibility issues. These tools simplify the integration of new parts, which helps the system stay flexible and responsive to change. It's also crucial the control systems for pumps and motors can talk to other system parts. Strategic integration tools include:
- Custom interfaces: Tailored solutions that align with specific system requirements are essential for compatibility. By customizing approaches to meet unique needs, custom solutions can lead to effectiveness within various operational frameworks.
- Flexible software: Adaptive software solutions are designed to enhance communication across various system components. By facilitating efficient data exchange and interoperability, these solutions help optimize system performance and reliability.
OEMs know making sure pumps and motors work well with other system parts is more important than ever. By focusing on standardization, modular design and thorough documentation, along with collaboration, testing and adaptable interfaces, OEMs can build efficient, forward-thinking solutions. For the off-highway industry, this reduces potential downtime and improve their longevity and makes operations more efficient.