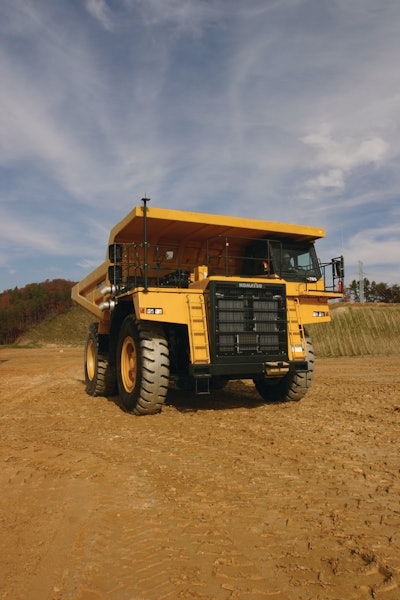
Over-the-road truck drivers are the first to say ride quality can make or break a new truck, and it's no secret to truck designers and manufacturers. Nowadays, providing a safe and comfortable work environment is crucial. By law, truck drivers are limited to driving 70 hours in eight days, with a maximum 10-hour work session before an eight-hour break. Drivers will see thousands of miles of interstate while staying within the limit.
Material extracted in mines and quarries make the strips of highway possible. Hauling that material at surface operations are trucks that make 18-wheelers look like minivans. Those off-highway trucks could be running 24/7 with different operators at the wheel; each driver might be in the seat as long as 12 hours a day.
The long-haul trucker can pull into a truck stop for country-fried steak and a change of scenery, but the mine haul truck's location around noon may be so remote the operator will stay in the cab for lunch. As with on-highway trucks, cab designers and manufacturers are also taking care of those operators.
In the next several months Tom Stedman, product marketing manager, Komatsu America Corp., Peoria, IL, will be spending a lot of time traveling North and South America's highways and haul roads. Komatsu's 100 ton HD785-7 off-highway truck has been working at many job sites for a year. Forty trucks have been shipped from Komatsu's factory in Peoria since March 2007.
For Stedman, it's time to visit the sites to see how the truck is working for owners as well as truck operators. For Komatsu, hearing the "voice of the customer" involves a process that is taken seriously.
"I'll talk to management and operators to complete a formal evaluation of what they think about the new truck," says Stedman. "We want to know what they like and what they don't like."
How comfortable the operator is up in the cab is second only to evaluating the performance of the drivetrain. For that truck to be running 24/7, high availability is required from the machine.
The meetings may be as simple as working through a survey in a one-hour visit. At other mines, Stedman might spend a week operating the truck. He'll note fuel consumption, tire wear, and the relationship between the truck and loading tools. "It is quite involved," he says. The mines are very busy, but the customers are understanding. They let us come in and talk or watch the machine's operation."
When Stedman returns to the office he will have volumes of data illustrating how the new trucks are performing in real-world conditions. Items noted for possible revision may be as minor as an interior console hinge that could be a little better to something that affects the day-to-day operation of the truck.
The data is used to develop a formal presentation that is reviewed with the decision making team: marketing and product support, application and design engineering, and executive management. Up to 24 months following the meetings there will be minor revisions to the HD785-7 which will incorporate some of the changes the customers suggested.
Komatsu has teams dedicated to cab design in Peoria and in Japan. The group covers Komatsu's wide range of products, from rear dump trucks to front end loaders. Within cab engineering, groups focus on specific product lines.
"Komatsu moves engineers around within the group," says Stedman. "When a junior engineer on truck cabs is promoted, it may be to senior engineer on excavator cabs." This helps Komatsu maintain consistency across cab lines while giving engineers knowledge across a range of development teams.
Comfortable equals safe
The HD785-7, or "Dash-7", as it's known around Komatsu, features a number of significant changes over the previous HD785-5 truck that keep operators safe as well as comfortable.
It means more than providing a car-like ride, however. "My feeling," says Stedman, "is safety is the driving force and the end result in operator comfort improvements."
If designers can simplify a machine's operation while placing the operator in an ergonomically correct environment, the user will have fewer distractions. "The driver will be able to pay attention to the operation of the machine and what is going on around the truck, such as topographical changes and where the other machines are working."
In the HD785-7, limiting distractions meant looking at the placement and the quality of virtually everything the operator would interact with in the cab, including gauges and switches. The engine power enhancement switch is within arm's reach, for example. The tilting and telescopic steering and five-way adjustable seat (for North American trucks, the best driver's seat Komatsu could find was specified) allows each driver to fine-tune the driving position.
After climbing the eight steps onto the cab deck, the driver's hard hat is 15.5 ft. above the ground. Inside the two-person cab, the design is remarkably familiar; the dash and controls aren't much different from a full-sized pickup. The design is also similar to cabs in other Komatsu machines. The HD785-7 shares its cab with two other Komatsu dump trucks (the HD465 and HD605), with some subtle differences depending on each truck's control requirements.
It's not possible to share cabs across all types of equipment, but "there is an effort on Komatsu's part to keep the same look and feel between different machines," says Stedman. "It's good from a marketability standpoint to have cabs with the same instrument layout, color scheme and similar material."
Comfort built in
Features designed to improve the operator's driving experience can be found much deeper in the truck than the placement of the AM/FM cassette radio and textures in the cab.
The Dash-7's cab is isolated from the rest of the truck with rubber bushings between the cab base and super structure of the truck. The viscous mounting system minimizes metal-to-metal contact to not only reduce vibration but the sound level inside the cab, as well. Hearing loss is an important issue with the Occupational Safety & Health Administration (OSHA) and Mine Safety and Health Administration (MSHA). Noise level at operator's ear in the truck's cab is 75 dB(A).
Well below the floor of the cab sits a Tier 2 Komatsu SAA12V140E-3 turbocharged, after-cooled V-12 engine putting out a maximum net horsepower of 1,178. It is sitting in the truck frame on rubber bushings, further isolating the powerplant's vibration from the rest of the truck.
The dump body control has been improved for the Dash-7, which was another modification in the comfort department. In the previous Dash-5, the controls were fully hydraulic. A lever in the cab directed fluid to the hoist cylinders, raising the body. In the new model, the lever communicates with an electric switch which sends a signal to a hoist control valve on the hydraulic tank, which then operates the twin two-stage telescoping hoist cylinders.
The arrangement provides for precise body control. Sensors monitor the body as it is lowered. When it is within 18 inches of the frame rail its descent is automatically slowed.
"On an older rear dump truck, when lowering the body it goes down fast, slamming down on body pads on the frame," says Stedman. "It's a jolt to the operator and places additional stress on the truck. Relatively speaking, the body isn't a lot of weight when it is empty, but slamming it down on the rails every 10 or 12 minutes, all day every day — that adds up."
On the HD785-7, the operator sees a light on the dash, ensuring the body is fully down.
The long-haul trucker spends most of the time between Points A and B. So it is with the haul truck driver, as well. Comfort, safety, and reducing distractions the driver may be faced with comes down to making the machine easier to drive on the haul roads.
To that end, Komatsu engineers worked with the truck's front and rear suspension to improve rebound control, helping to reduce the rolling and pitching that is typically found in large trucks. An optional three-mode (soft, medium and hard) automatic suspension system control senses the road conditions and adjusts the ride stiffness to match the road conditions.
The three-mode system has been popular with buyers. "With the truck being able to dial in the proper setting, the operator is not bouncing around inside the cab, pitching forward and back," says Stedman. "He can concentrate on his environment and maintain control of the steering and braking."