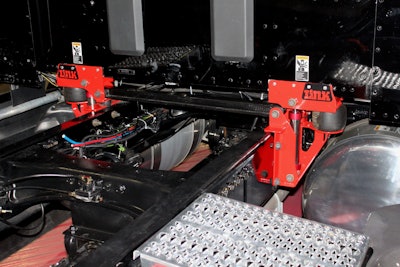
Today, operators of vehicles transitioning from on- to off-road terrain put themselves and their assets at risk.
It’s a common scenario: a fully-loaded dump truck hauling gravel makes its way off-road to deliver its cargo to a jobsite. The vehicle is relatively easy to handle because its heavy-duty springs have been painstakingly engineered to provide a moderately smooth ride, as long as the frame rails are under load.
The operator successfully dumps the gravel and begins the trip back, but this leg of the journey is a considerably different experience. The suspension system that performed so well while bearing the full load is now rebounding vigorously on the uneven terrain, making the cab, its occupant and all the contents therein bounce like an amusement park ride, minus the amusement.
The above sequence isn’t just played out across our continent, but throughout all continents globally, and the magnitude of their impact is stunning to contemplate. Cabs routinely sustain structural damage, vehicles become harder to handle and drivers decrease speed to avoid losing control, but are still exposed to dynamic forces that, according to ISO 2631-1:1997 standards, can ultimately cause internal injury over prolonged durations. The resulting asset destruction, erosion of driving effectiveness and health risks all create a wholesale reduction in productivity and revenue potential.
Some OEMs, fleets and owner-operators have tried to mitigate part of the problem with advanced seating technology. While better seating may alleviate some driver discomfort while traversing rough terrain, it doesn’t address the other issues. Though the driver will remain more stable, he may still proceed with great caution, because steering wheels, gear shifters, accelerator and brake pedals will all still move with the same dynamic forces as before. Vehicle structures may still be compromised and the contents of the cab, including a team member who may be occupying a sleeper compartment, are still at risk.
There is only one solution that addresses all the problems stemming from energetic cab movement, and that solution must focus on mitigating the mechanical forces that seek to act on the cab itself. Enter Link Manufacturing’s Cabmate Semi-Active Cab Suspension.
Link’s 10-year quest for a viable, practical and affordable semi-active cab suspension
As the innovator behind the 1980 introduction of the Cabmate Cab Air Suspension System, Link Manufacturing understood early on the positive impact that could be achieved through independent cab suspension management. The industry agreed and today, Cabmate is the standard in premium cab suspensions, and Link supplies more OEM cab suspensions than anyone else in the world.
In 2008, Link began exploratory efforts surrounding the development of a semi-active cab suspension. Its experience with Cabmate helped Link focus on the basic premise that the cab is already a mass on springs. A vehicle’s primary suspension is designed to deal with the dynamic range of road conditions, so Link could direct its efforts to the interaction between the frame rails and the cab.
It soon became apparent that there were gaps in the available technology and that the expense of the needed components would make the endeavor and the byproduct cost prohibitive.
Fortunately, time and technology march on, and in 2014, the engineering staff at Link began pursuing a semi-active cab suspension again, assembling a skunkworks-esque project team to revisit the task.
As the group began in earnest, it became immediately apparent that not only was their objective achievable, but that most of it could be accomplished in-house.
Link created its own control system, writing proprietary algorithms that would govern the system's performance to Link’s high standards.
Link began and continues to work with its shock absorber suppliers to perfect a shock absorber that will be exclusive to the Cabmate application. At this writing, both magnetorheological dampers and hydraulic actuation are being explored.
The only off-the-shelf equipment that Link needed to buy was a single electronic control unit (ECU), which accounts for the initial 1-lb. (0.45 kg) weight the system will add to a cab. Once OEMs begin to integrate the new Cabmate Semi-Active Cab Suspension System into their equipment builds, even that weight will be eliminated if they load the licensed software onto their resident ECUs.
When it came to testing the working models, Link’s 38 years of cab suspension experience positioned it like no other to put the prototypes through their requisite paces. Link’s is certified to IATF 16949 standards (previously TS16949), and over the years, has assembled a world-class testing operation.
How the new Cabmate Semi-Active Cab Suspension System works
The system takes in environmental information through two accelerometers positioned on either side of the cab. Each accelerometer continuously measures acceleration at the top of the suspension.
Additionally, the system relies on data coming from two position sensors, also located on both sides of the vehicle. The position sensors constantly monitor the position and velocity of the vehicle’s primary suspension.
The Cabmate Semi-Active Cab Suspension System’s ECU reads information from the accelerometers and position sensors and determines the optimum settings for the shock absorbers to maximize ride comfort. The ECU also uses the information to determine whether it needs to fill or exhaust air from the system’s air springs.
The ECU’s adjustment command signals are output directly to the shocks and air valves. These signals and the resulting dampening adjustments occur hundreds of times per second, resulting in a dynamic dampening state that is optimized for each instant.
With the use of a magnetorheological approach, voltage from the ECU causes the fluid in the shock to thicken very quickly, which makes the shock stiffer when needed. In the case of the hydraulic method, an orifice rapidly adjusts its size to either admit or impede fluid migration as needed to mitigate the activity of the frame rails. Neither system requires more than 10W of power to operate.
Both intelligent magnetorheological and hydraulic shocks deliver a clear benefit that is both fluid and instantaneous in its expression. With an intelligent system, drivers and passengers have a very soft shock, as desired while traveling down a smooth highway, and a very stiff shock, as desired when driving in uneven or off-road conditions.
The Cabmate Semi-Active Cab Suspension System also features electronic height control. The system minimizes air consumption compared to traditional height control valves, because it does not fill or exhaust air in response to dynamic suspension motion.
What Link’s Road Optimization Intelligence (ROI) will mean for OEMs, fleets and owner-operators
The OEM
OEMs spend significant time measuring cab suspension performance on proprietary test tracks of their own design. With accelerometers mounted on the frame rails and on the cab seat, they adjust the overall suspension system to perform optimally in their unique environment.
Using ISO 2631-1:1997 standards, the OEMs calculate a “ride number” that provides a tangible cross-vehicle method of comparison for ride quality. Based in part on NASA experiments to measure the physical effects of human exposure to mechanical vibration and shock, the number has become the gold standard within the industry. A vehicle’s ride number can also be used to calculate how many hours a driver can be exposed to the forces associated with that ride number, before internal injury may be imminent. Link Manufacturing
Link’s perspective is that its products are designed to make its customers' products better. Over the years, Link has had the honor of working with many OEMs on their test tracks, but in reality, the real world presents variables that simply can’t be recreated on any test track. Therefore, Link’s objective with the Cabmate Semi-Active Cab Suspension and its associated ROI acronym was to create a system that delivered a better overall ride regardless of road surfaces or even atmospheric forces, such as wind sheer.
One such OEM relationship has led to a golden opportunity to compare the efficacy of a great cab suspension with that of the Cabmate Semi-Active Cab Suspension. The Peterbilt 579 is known for its outstanding ride quality and features a Link Cabmate Cab Air Suspension System.
In 2016, Link purchased a Peterbilt 579 80 in. (2.03 m) sleeper cab with the express intent of testing the Link original equipment cab air suspension’s performance in comparison to the new semi-active cab suspension system.
As testing has continued, the data collected indicate a significant improvement in all areas of measurable ride quality performance. The quantitative difference can be examined by comparing the vehicle’s ride number before and after, but the qualitative difference has left many who have experienced it first hand, in a word, impressed.
The Fleet
Fleets will find numerous advantages associated with any vehicle fitted with Link’s Cabmate Semi-Active Cab Suspension System, beginning with protection of the whole cab asset. Now, the cab, its structure, its operator and any passengers will benefit from a greatly enhanced ride quality, regardless of the on-road or off-road surface conditions encountered.
Less stress on the cab and driver means lower maintenance costs, better vehicle handling and reduced injuries. Driver fatigue is also lessened and the enhanced ergonomics may enable drivers to traverse an uneven route more quickly, enabling productivity to rise and additional runs to be made. Most important is an improved work environment for operators, which could logically be expected to be a positive factor in the area of driver retention.
Owner-Operators
Independents and owner-operators will protect their personal investment in their vehicles, and will enjoy a ride quality like they’ve never experienced before. They can also expect to pay significantly less for the Cabmate Semi-Active Cab Suspension System than they would for an advanced seating package that doesn’t protect their overall cab. With the amount of time many owner-operators spend in their vehicles, a true quality of life dividend can be expected.
Ready for Prime Time
Link is currently in discussions with multiple OEMs and the industry can anticipate seeing the Cabmate Semi-Active Cab Suspension System available on select 2020 and 2021 model vehicles.