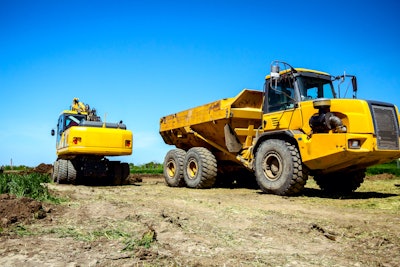
Off-highway vehicles are commonly called upon to do much more than just drive around jobsites. They often perform a wide variety of tasks, whether they have tool attachments, payload handling gear or other related equipment, and these accessory operations are increasingly handled by a degree of automation and digital controllers. In fact, some off-road vehicles might be outfitted with automated electro-mechanical systems, much like would be found in any modern factory or manufacturing site.
Whenever users are working with automation, designing for safety becomes a prime consideration. Safe design takes the form of easily recognized and usable user control devices, mechanical guards and electrical sensors, integrated to provide a functional yet protected working experience. Emergency stop (E-stop) switches are a recommended element for most types of automation systems, and are sometimes required by regulatory authorities, so designers should familiarize themselves with the options when selecting these devices.
Switches for Industrial Service
Pushbuttons, switches, pilot lights, and other operator control and signaling devices for industrial service commonly are sized to mount through round 30mm, 22mm, or 16mm holes. These sizes ensure the products are big enough to be easily usable, and built tough enough and with the necessary provisions to protect them from the harsh environments, such as those often found in off-highway environments.
These devices should be manufactured from robust materials, such as polyamide 66 (PA66), yet designed with user ease-of-use ergonomics in mind. Resistance to vibration is a must for vehicle and industrial applications. Once installed, the devices need to maintain a front sealing rating of at least IP65, indicating a degree of resistance against dirt and liquids, to make them suitable for typical applications. Also, contacts and terminals should be made from silver-plated brass for maximum conductivity and corrosion resistance.
Specifiers also need to ensure that these devices meet agency approvals, such as UL, TUV, and VDE. Switch devices in general, and e-stop switches in particular, should comply with industry standards such as IEC 60947-5-1 for low-voltage switch gear and control gear, and IEC 60947-5-5, which specifically relates to electrical e-stop devices with a mechanical latching function. These standards address many device characteristics. One example is a requirement for testing to ensure devices can deliver electrical lifecycles of at least 6,050 operations at full load, and up to 50,000 cycles at a lower load to represent mechanical cycling.
Compact Control Choices
While there are many devices on the market meeting these requirements, most of the existing form factors are at odds with the limited installation space available on many types of off-highway vehicles and other industrial equipment.
This is partly because of the size of the device visible above the installation panel, but the dimensions of the wiring portion beneath the panel can also cause issues. Many industrial pushbuttons use contact blocks that need to be big enough to incorporate screw-based terminals, and sometimes the terminal blocks are stackable, which can add to the behind-the-panel dimension.
For off-highway vehicles, robotics, autonomous guided vehicles (AGVs), and other industrial-grade automation applications where space is often at a premium, specifiers need product choices with specific features to overcome these and other constraints. Figure 2. Compact estop switches, such as the APEM A01ES, EC and EC PCB series, are designed with the form factor, ergonomics and low-profile electrical connections required by off-highway vehicles, robots and industrial applications.APEM
In the case of e-stop switches needed for limited-space applications in off-highway and other harsh environments, the device should have the following features (Figure 2):
- A compact yet ergonomic and modern button cap design in high visibility red, but with a green ring below the cap to provide clear unlocked status indication.
- A simple push-to-latch, twist-to-release operation.
- Easy and safe panel mounting that maintains IP65, with an extra locking ring to avoid a “floating” mount.
- Dual-pole normally closed contacts for safest operation.
- Extra-low-profile terminal block options, allowing vibration-resistant solder terminal or printed circuit board (PCB) connection.
With the right devices available, designers can support a wide variety of applications.
E-Stop Applications
Almost any industrial vehicle or equipment with moving apparatus should probably be equipped with some form of e-stop function so workers can quickly place the equipment into a safe state. For a tractor, scissors lift, boom lift or similar equipment, the typical design is to install an e-stop switch on an armrest console or dashboard, within easy access of the operator.
In other cases, especially for certain types of heavy equipment, robotics, and AGVs, a remote wired or wireless pendant control — sometimes called a belly box — is carried or even worn by the user. These control options are obviously quite small compared with a full control panel or dashboard, so the e-stop switch needs to be compact to work in these applications (Figure 3).
Figure 3. Pendants and belly box controls are ideal applications for the compact APEM EC PCB e-stop switch. Even large vehicles and industrial equipment often have small areas for dashboards and armrest consoles, so compact e-stop switches are needed.APEMEquipment designers and OEMs of off-highway vehicles and other industrial systems need to prioritize safety for the products they create, sell and support. These applications operate in challenging environments, so control devices must be tough enough to survive, while complying with all related standards and certifications. Choosing the right compact e-stop switch to work in these situations will ensure that designers are delivering reliable and safe automation to their customers.
___________________________________________________
Chris Do Vale is the senior component product manager for APEM, Inc.