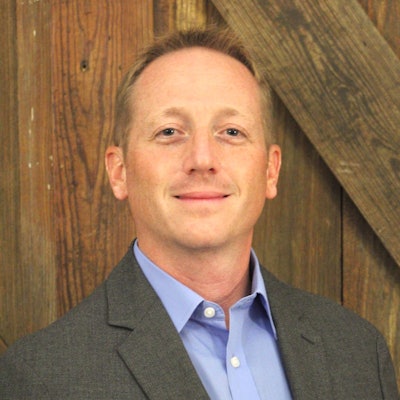
Each year, our State of the Industry issue looks at the top trends and technologies within the heavy equipment industries. We also dig into current and future market conditions, as well as regulations which may currently or in the coming years have an impact on how the industry will go about designing its equipment.
To get the best insights, we speak with executives from a variety of companies working in the industry—everyone from associations, to OEMs to component suppliers. Below are responses provided by responses provided by Brian Kreifels, Vice President OEM Sales North America, Jeff Hemphill, Chief Technical Officer, and Shoukat Ali Bhamani, Chief Information & Digital Officer, Schaeffler.
Read all of this year's executive Q&As.
Diesel, Electric & Other Power Alternatives
How, if at all, do you see the role of diesel engines evolving in the coming years?
Kreifels: The continued need for diesel engines to power commercial equipment looks to remain quite strong, especially in the near to intermediate term. While there are some applications – such as compact construction equipment – that can be more readily electrified, there are many more applications where the available on-board electric generation or storage capacities are simply insufficient at this time. As a result, it will be necessary to continue to improve diesel engine technology to meet legislative requirements and market expectations which will drive efficiency improvements, enhanced in-cylinder emissions controls, and reduced total cost of ownership (TCO).
With regard to improved efficiency, future diesel engines will increasingly rely on technologies that minimize friction and thermal losses. Here we see opportunities for technologies such as next-generation rolling element bearings from our INA and FAG product brands, low-friction coating solutions as well as waste-heat recovery that have yet to be fully exploited. Variable valve actuation strategies (e.g., variable cam timing, valve/cylinder deactivation, cam profile switching, etc.) as well as active, controlled management of the engine and vehicle systems’ cooling circuits can deliver further engine efficiencies.
With respect to cleaner emissions, “in-cylinder” technologies can reduce or even eliminate the need for external aftertreatment devices – such as particulate filters and selective catalytic reduction (SCR) – while still achieving increasingly stringent overall emissions mandates. Indeed, many of the variable valvetrain technologies mentioned above can also be used to reduce in-cylinder emissions.
In-cylinder solutions offer the inherent advantage of being able to eliminate the packaging and installation challenges posed by external aftertreatment devices. In addition, in-cylinder solutions offer better and more consistent emissions control over the engine’s entire lifecycle.
With regard to controlling emissions over the engine’s lifecycle, we are also seeing increasing interest in our company’s INA hydraulic lash adjuster (HLA) technology – not just with regard to eliminating lash maintenance, but also as a means to reduce the need to open up the engine for service (which can adversely affect vehicle emissions). Additionally, HLAs allow more precise and consistent control of the opening and closing ramps to help optimize combustion efficiency.
What alternative fuels do you foresee entering the heavy equipment industry in the next 5-10 years?
Hemphill: The U.S. is one of the few countries where all forms of transport collectively represent the largest source of CO2 emissions. This leads to continued pressure to reduce CO2 as well as other forms of emissions. Hydrogen is gaining momentum as a fuel with strong support from the federal government. This includes fuel cell-powered vehicles as well as new efforts to burn hydrogen directly in combustion engines. At Schaeffler, we have experienced this momentum directly as we develop bipolar plates for fuel cells as well as subsystems like thermal management modules. Biodiesel remains a viable alternative as it can make use of existing infrastructure, though it still faces cost issues. CNG (compressed natural gas), meanwhile, has an attractive cost basis with natural gas prices remaining low. However, this option would require a new infrastructure, and the investment has not yet justified itself. We are involved in development efforts for these alternative fuels, such as coatings for engine components or variable valve trains to better utilize the fuel. So, while a clear winner is not yet in sight, the industry is learning rapidly, and we are prepared to support the eventual leader. Jeff Hemphill
How will electrification—or other alternative energy/power systems—continue to advance in the heavy equipment industry?
Kreifels: The momentum towards electrification continues to build each year. As automotive manufacturers continue to advance electrification technologies, the costs will come down and market acceptance will go up in the off-highway market, too. However, the uses and requirements for electrification technologies in the off-highway sector will be unique and require optimization to meet these needs. Likewise, on-vehicle energy storage/generation will be a key factor that will restrict how quickly and in what ways off-highway vehicles will employ electrification technologies.
While there has been a concerted focus on electrifying drivelines within the heavy equipment industry, there is also strong interest in electrifying the vehicle’s other mechanical or hydraulic systems. For example, hydraulic cylinders are utilized in many positions on industrial vehicles. By their nature, hydraulic cylinders have a variety of limitations with respect to efficiency, controllability, connectivity, NVH (noise, vibration and harshness) as well as their environmental impact. Technological advancements such as our innovative electromechanical rod-style actuators can mitigate these limitations by serving as outright replacements for the hydraulic cylinders inside industrial vehicles.
Data, IoT & Connectivity
What potential do you see in the use of artificial intelligence (AI) and augmented/virtual reality (AR/VR)—both for the design and manufacture of products as well as within equipment?
Bhamani: We have seen a tremendous growth of AI and AR/VR in our personal lives over the last few years, especially through consumer electronics. This includes a number of sensors on our phones to collect the necessary data and provide analytics in the form of AI. It is imperative that people apply this technology to their professional lives to gain business value.
Several business segments took a lead to become early adapters (e.g., online retailers, insurance companies, etc.), whereas the manufacturing sector is only now catching up. At Schaeffler, we started our digital journey a few years ago, and we quickly started seeing the business benefits of AI and AR solutions in areas such as:
- AI visual inspection to improve work center performance
- Digital asset tracking and building digital data as “asset” to develop AI
- VR-based remote services (e.g., customer support, factory maintenance)
- Condition monitoring to minimize downtime/increase machine run time
Earlier this year, Schaeffler launched its award-winning OPTIME condition monitoring solution for rotating machines. Data collected from this innovation could be further analyzed to provide artificial intelligence. Shoukat Bhamani
The future development and implementation of AI and AR/VR will be crucial to building autonomous factories, supply chains and vehicles. End-to-end product tracing – from components to end usage – as well as product warranty, maintenance and lifecycle management will be possible thanks to AI. More realistic forecasting, made possible by AI, will reduce manufacturers’ inventory and improve customer delivery. Moreover, AI-based business models will open up new markets & opportunities. In addition, AI definitely has the potential to greatly enhance the employee experience – i.e., motivation – in a manufacturing environment. Ultimately, all of these improvements will lead to faster, simpler and smarter business operations. I believe we have just scratched the surface; real value will be realized in the coming years.
Challenges & Opportunities
What are the biggest challenges facing the industry currently, or do you see the industry facing in the coming years?
Kreifels: In a future filled with vehicles powered by battery-electric motors and alternative fuels, one area of concern is how the necessary recharging/refueling infrastructure will be built – and how it will be paid for.
As a supplier to vehicle OEMs, Schaeffler must constantly balance the cost of implementing new technologies against overall product cost. We need to focus on bringing value to our customers that will also directly benefit the end user. Such cost concerns can be mitigated by encouraging customers to focus on total cost of ownership (TCO), because reducing unplanned downtime, increasing productivity and reducing fuel consumption all provide a direct economic benefit for the machine owner. The challenge is to demonstrate an acceptable payback period for the additional costs associated with the new technologies required to meet various government and market mandates.