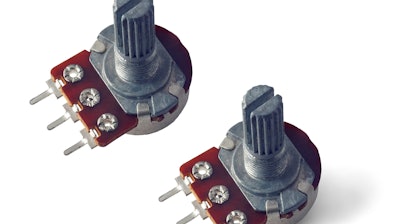
Many linear motion applications that employ rod-style electric actuators require information on the position of the load at every point of travel, but because stroke lengths and applications vary so wildly, finding the ideal position feedback solution can be challenging. One of the most common methods for determining where the actuator is in its stroke uses potentiometers, also called pots, to track changes in electrical resistance or related voltage drops as the actuator extends and retracts.
To function as position-recording devices, potentiometers must maintain an electrical connection to the actuator power circuit. Designers can accomplish this using contact or non-contact potentiometer architectures. Contact-based position measurement has been the simplest and most economical approach but is limited in resolution, design flexibility and durability. Non-contact architectures overcome many of those drawbacks but have traditionally been too expensive to justify for many mainstream applications.
Today, however, the market for non-contact potentiometers has matured, and prices have dropped. The benefits of non-contact position measurement are available for a broader range of applications. Understanding the advantages of non-contact potentiometers will help motion system designers determine the most effective way to meet customer requirements.
Potentiometer Basics
Feedback voltage from a potentiometer typically changes from 0.5 to 4.5 Vdc as the actuator extends. Potentiometers are generally rated in ohms of resistance across their entire range and on the shaft's number of turns (revolutions) from zero to full coverage. The most common units are 10k (ohms) 10 turns.
As the actuator screw extends or retracts, there is a discrete step-change in resistance, which can be converted into linear position measures. The more turns the potentiometer takes before it reaches its full resistance range at the end of the stroke, the more precise the position measurement capability it can deliver.
A contact-based potentiometer reads these voltage changes by gliding its wiper across wire-round resistance coils, counting each move from one wrap to the next. Non-contact potentiometers read the voltage changes as well but do so with electromagnetic sensors instead of contacting wipers. The designer's degree of flexibility in implanting contact or non-contact-based potentiometer position sensing depends largely on user requirements.
Customer requirements for resolution and durability will impact a designer's options to use contact or non-contact position measurement.
Requirements for accuracy, flexibility and durability will determine whether contact (left) or non-contact potentiometers (right) are a better fit for a given application.Thomson
Designing for High Resolution
With contact potentiometers, the designer's primary option for increasing resolution is modifying the gearing to correlate potentiometer turns with motor or actuator screw turns. Designers who need position feedback across a full long-stroke application might gear the potentiometer to turn less as it moves. For example, in a short-stroke application, if the customer required position information for only 40% of travel, they would sacrifice resolution because there would be less resistance change of the shorter travel time.
Because the number of wraps in the coil of a contact-based architecture is physically limited, there are only so many step changes to count, limiting the resolution of the position information it can deliver. And once a manufacturer has configured it for a specific number of turns needed to achieve the desired resolution, the design is set.
Non-contact potentiometers, on the other hand, enable higher resolution because they do not rely on physical wipers or gearing. Like contact-based potentiometers, non-contact sensors determine position by recording resistance changes across the stroke length, but instead of getting this information from a physical wiper touching a coil, they use an electromagnetic sensor that detects pulse changes in the surrounding magnetic field.
The sensor outputs this digital signal to a non-contact potentiometer's own integrated circuit, which converts it to analog for reading by the actuator's onboard electronics. This signal represents the analog values as position. Because these signals do not need to correlate with physical constraints, the non-contact potentiometer gives virtually infinite granularity in measuring the stroke position.
Programmability Translates to Design Flexibility
This ability to record infinitesimally small voltage changes without physical contact and manage them through a software interface makes resolution programmable. If the end-user needs tighter resolution, for example, the designer can change it through the interface. For instance, if the application requires a high resolution between 0.5 and 4.5 volts, they can program the system to accomplish that. If they didn't need as much resolution, they might program it to go to 2.5 volts at the end of the travel. The designer can do it all with software rather than physical gear reductions.
Such programmability can be valuable, for example, in applications needing to change the stroke to compensate for different geometries. Actuators with contact potentiometers, for example, might return different feedback from different strokes. Correcting this would require dedicated gearing for each stroke length. With a programmable non-contact device, the designer can maintain the same feedback over the stroke regardless of changes in geometry. A user can keep that consistency without having to modify the physical architecture.
Non-contact potentiometers would also make it easier for the designer to program more complex movement profiles, for example, seeking forward a few millimeters or making a small set of movements back and forth to zero in on the desired position.
Non-contact potentiometers can be valuable in any application requiring the actuator to move repeatedly and consistently to the exact location, such as managing the flow gate in a seeding application. In such applications, the actuator operation may be under the control of a PLC and perhaps hidden from an operator's view, so there is no visual feedback to help determine whether the actuator has traveled far enough.
The programmability of non-contact potentiometers also makes them excellent for developing custom applications. One part number, for example, can be programmed to handle multiple stroke lengths, making it much more efficient to test out prototypes in real-world settings.
Due to eliminating gearing and wipers, non-contact potentiometers better absorb shock and vibration from heavier-duty applications. These potentiometers, along with many other control and performance features, can be found in select electric linear actuators on the market.Thomson
Implementing Non-contact Potentiometers for Durability
Non-contact potentiometers have durability advantages as well. Eliminating the gearing makes for a more durable and reliable actuator. Gearing is subject to routine wear, contamination, and misalignment resulting from vibration and shock. As such, they are excellent candidates for replacing hydraulic cylinders that might otherwise be specified for environmentally challenged applications needing position control.
Eliminating the need for wiper contact and gearing gives non-contact potentiometers another durability advantage over contact devices. In an application in which the actuator does not change position for an extended period, the wiper can vibrate and wear a dead spot on the coil, which would drop the signal and cause the potentiometer to fail.
When this happens in a system that is running process logic, it loses track of the position and can also interfere with some controlled moves. A movement profile that depends on a particular value will not find it, which could replace the potentiometer or the actuator.
Non-contact potentiometers are ideal for applications such as mobile off-highway/agricultural (left) and factory automation/automated guided vehicles (right); in such applications, the actuators might be hidden from view and under the control of a PLC. The potentiometer can be programmed to drive the same distance and travel the same length every time.Thomson
Breaking contact
Designers who have believed that non-contact potentiometers were only for high-precision applications would do well to revisit them for all applications. Even if high resolution is not critical, removing gearing from the BOM, programmable position feedback and a more rugged solution could offer significant advantages.
As the design and specification process becomes more iterative between engineering and customer teams, programmable capabilities such as the non-contact position sensing will deliver more tailored solutions in less time, without creating additional tooling.