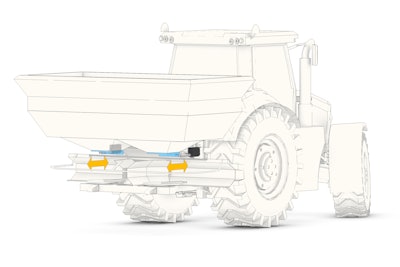
Electric linear actuators are gaining ground in mobile off-highway (MOH) machine design applications. In the past, electric linear actuators could efficiently replace a single hydraulic or pneumatic cylinder in simple, end-to-end motion applications using up to 100 watts of power. Today, they can perform complex motion profiles drawing power up to 400 watts. Part of this new functionality stems from embedding microprocessors into the design, creating smart actuators.
Designing with Smart Actuators
Smart actuator applications may be as simple as low-level power switching or as sophisticated as implementing a control deck across a CAN bus network. Having a microprocessor in the actuator enables access to functionality and data that might otherwise require incorporating external components. Before a smart actuator starts to move, it checks the environment to be sure it is safe for the user and the application. Once it starts, it measures its position along the stroke. Collecting this data without adding external sensors and other equipment also reduces the number of components needed and simplifies installation.
Image 1. Embedded electronics synchronize multiple smart actuators to control the opening and closing of storage bin doors on a grain harvester.Thomson Industries, Inc.
Self-driving agricultural equipment is a good example of a smart actuator application. Some grain harvesters, grape harvesters and farm tractors, for example, already operate autonomously. Because of this, actuators must control stroke and force on their own. Without an operator who might otherwise control operation based on visual clues, an autonomous system must rely on electronic feedback. Most smart actuators have built-in fieldbus capability to provide this feedback. Some, for example, have CANopen masters so you can connect to a vehicle control directly without drivers or other components needed to access operating data. The vehicle's built-in logic manipulates speed, force and position from the master control unit and provides precise control of the actuator and knowledge of its position at every point of the stroke.
Electric Actuator Advantages
The ease with which electric actuators control stroke, speed, position and force is an advantage when compared to hydraulic and pneumatic systems, but there are others. Energy efficiency is another important benefit. In traditional MOH applications, the hydraulic or pneumatic system must operate all the time. Electric actuators, in contrast, are power on demand, consuming power only when movement occurs and without parasitic power loss.
Image 2. Because they use no oils, electric actuators are often preferred for food-related MOH applications, such as this seed planter.Thomson Industries, Inc.
Therefore, electric actuators are evolving to perform tasks that were once the sole domain of fluid technologies. Electric actuators can manage loads up to 16,000 Newtons. Another traditional limitation of electric actuators has been withstanding shock load handling, but even this is being addressed to some extent by hybrid electro-hydraulic actuators (Image 3).Image 3. Hybrid electro-hydraulic linear actuators can perform some tasks that were once the sole domain of fluid technologies. Their ability to withstand shock loading for applications, such as this utility vehicle, makes them ideal solutions for the MOH industry.Thomson Industries, Inc.
The Next Frontier
As electric actuators advance, off-the-shelf options are also growing. Probably the biggest challenge is identifying the existing and new areas in which intelligent actuation brings value and mapping them to the wide range of available options. Once OEM teams get used to designing with electric actuators, they find possibilities everywhere. They may provide a safety benefit. They could lower costs. Electronic actuators could be a way to add efficiency to a machine. They may also provide ergonomic benefits, such as automating a tedious task or adding more precision or repeatability.
As new motion control application needs evolve, the intelligence, compactness and flexibility of electric actuators will give them an advantage in overcoming obstacles and leveraging new opportunities.
Håkan Persson is global product line director, linear actuators, for Thomson Industries, Inc.