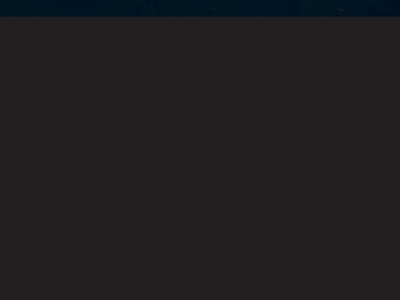
Vehicle system applications bring with it a unique set of environmental and situational challenges to address emergency fire suppression system development. Off-road and on-road mobile equipment is never in the same place when in operation. As a moving target, in the event of a fire on the vehicle means that any externally located suppression systems would have to take time to travel to the location to address the incident. A waste vehicle atop a garbage mound will be difficult to reach in a timely manner to supply adequate assistance before significant damage is done to it. It is because of these challenges that vehicle manufacturers began investigating on board fire suppression systems years ago.
Since then, on-board systems have evolved to accommodate new fuels such as natural gas, at which point Amerex Corp., Trussville, AL, developed its AMGADS (Amerex Gas Detection System) product line. The third generation system, AMGADS III, uses multiple Solid State sensors to identify misdirected gas—compressed natural gas (CNG), liquefied natural gas (LNG), propane (LPG), hydrogen and any other hydrocarbon fuel vapors—and alert the operator of potential danger with visual or audible warnings. AMGADS III also features an optional internal relay for automatic control of auxiliary devices like engine shutdown or fuel valve shut-off.
“New types of fuels, more advanced vehicle system technologies, higher demand for longer run times, and emerging industries and techniques that have higher risk and/or more extreme environments, increase the risk for more intense fires. Various hot spot areas with high-pressure and highly flammable fuels demand greater attention,” says Mark Neumann, Director, Standard Products, Tyco Fire Protection Products, Marinette, WI. “Suppression solutions for today’s vehicles need to have a holistic approach to protect these valuable assets.”
Actuation, detection and suppression methods
While each system will be a custom variation for each vehicle and customer need, there is a conscious effort to make the system scalable and modular for design and integration flexibility depending on the size of the vehicle and operating conditions. “We try to design our systems so they’re an adaptable, plug-and-play design,” says Ed Ruggles, VP of Sales, Amerex Defense. “On a dozer, I may need one agent tank with six nozzles, but on a larger machine we may need two tanks and ten nozzles. It all depends on the hazard analysis to ensure there is proper protection for the specific application and vehicle configuration.”
Systems typically have both manual actuation and automatic detection and actuation systems. Detection is done by spot sensors that act as a thermostat reacting to a breach in max temperature set by the customer. Other methods include linear wire systems that, when heated to a certain point, make contact and prompt an automatic deployment.
Firetrace International LLC, Scottsdale, AZ, manufactures automatic fire suppression systems utilizing its proprietary red tube system, Firetrace Detection Tubing (FDT), which bursts after it reaches a set temperature and releases the valves containing the specified dry, liquid or foam chemical agent to be discharged through the strategically placed nozzles.
The FDT system can be either direct or indirect; a direct system is localized to a target area such as a brake system for underground mining vehicles, and the chemical is distributed directly from the tube to where the burst is, whereas an indirect system would be total flooding of an area from the nozzles. A significant parameter when designing a direct system is the length of the tubing. “The reason for the length limitation is because of friction losses,” explains Mark Bowen of Paragon Fire Protection Inc., a distributor of Firetrace automatic fire suppression systems. When further than 100 feet away, the tubing will not be able to release the valve fast enough to discharge the chemical.
Tyco Fire Protection Products developed and recently launched the ANSUL LVS to combine cooling and fire suppression technology in a single agent. When engaged, the LVS liquid agent is targeted to address both fire suppression and cooling, and is effective in suppressing fires involving both Class B flammable liquids and combustible materials that result in Class A fires (i.e., wood, cloth, paper, rubber and many plastics). The LVS liquid agent can cool high-heat surface areas, such as turbochargers and exhaust manifolds, to temperatures below the ignition point of flammable liquids such as diesel oils and hydraulic fluids, and also safeguard areas on the vehicle where flammable liquids can settle by cutting off oxygen and minimizing the risk of re-flash.
In addition to the ANSUL Liquid Vehicle System, Tyco Fire Protection Products offers the ANSUL A-101 Dry Chemical Fire Suppression System, as well as the A-101/LVS Twin-Agent Fire Suppression System.
The A-101 Dry Chemical system is an automatic or manual fire suppression system that can address Class A, B, and C (energized electrical equipment) fires. The pre-engineered systems are designed for use on large, off-road equipment, have a wide array of nozzles and tank capacities (10 to 250 pounds), and are available in low temperature models that perform reliably in extreme temperatures. The dry chemical agent quickly knocks down flames, by flooding entire volumes or targeting specific high hazard areas.
The A-101/LVS Twin-Agent Fire Suppression System provides the joint performance of the LVS liquid agent combined with a dry chemical agent system to simultaneously suppress flames while cooling surrounding, specific high-heat components using the liquid agent.
Programmability
“Everybody starts with a panel that operates the system,” says Ruggles. The panels allow the customer to download operation data to help troubleshoot the system and do hazard analysis for maximum temperature mapping for target areas and program a specific sensor for that area. Amerex’s panel is made in house and controls the system electronically, supervises the current and provides back-up power if the vehicle loses power temporarily. “The panel can interface directly with the operator panel to show if there is a heat event and its location, as well as notify the operator with an alert or even initiate a system shut down if programmed to do so.
“On our new panels, I can plug into a port on the front of the operator display and download data and look at the last 1,000 events that happened on another device. If someone is having issues with the system discharging, I can look at those past events and see if the heat sensor on the hot side of the engine bay met its temperature peak and discharged the system, and then reevaluate if the maximum temperature is set too low for that sensor. Or you can see if someone hit the manual release button and what time it happened,” explains Ruggles.
“The next step is to have that information to go right back to the CAN bus system, which is something we’re working on now. That will allow us to feed information back into the system to allow the vehicle systems to modify their behaviors without operator intervention, or at least alert someone else besides the operator if there is a problem. We’re being asked by many OEMs to find a way to have fire suppression integrate with vehicle operation.
“Programmable heat detection was released a couple of years ago to the military, and now we’re bringing it to the commercial vehicle space,” says Ruggles. “It allows customers to choose which type of response they want, whether it be fixed temperature, rate-of-rise or both.”
Future considerations
The speed at which a chemical agent is released is not technically a standard to be met, but rather a general rule of thumb. But, when the system is for the military vehicle industry, there are more stringent requirements in place. In the crew cab, for example, there are millisecond detection and extinguishment standards to meet. “You’re looking at detection of the fire within two to five milliseconds, having the agent discharge in 25 milliseconds and complete extinguishment in less than 250 milliseconds,” says Ruggles.
When it comes to integrating the fire suppression system, installation needs to balance a close proximity to the potential hazard areas with easy accessibility for maintenance and replacement after a suppression event. “There is a science to strategically locating the system in the optimum location,” says Bowen. Splitting suppression systems to be zonal also prevents failure of one system impeding the operation of another, but ultimately it is up to the customer if they want them separate or connected for full vehicle suppression. A forestry OEM, for example, may want all external suppression systems to deploy at once to avoid debris fires in the outside environment.
As extinguishment rates get faster and programmable expectations continue to rise, the heat is on for fire suppression system manufacturers to continue to develop intuitive, innovative solutions to protect the operator and the assets in every vehicle arena and environment.