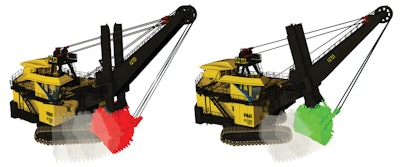
Regardless of the application, whether it's in a quarry or construction site, there are large machines interacting with each other, smaller vehicles and workers on foot. All of these scenarios present risks of collision between equipment, as well as the possibility for equipment to collide with itself during operation. Whether the way operators are using the equipment is changing as performance expectations evolve, or simply operator inexperience, collision mitigation is becoming essential for maintaining the integrity of expensive assets and human safety.
According to Caterpillar, collisions between heavy and light vehicles are one of the most common types of accidents on mine sites, usually caused by poor visibility during equipment startup and slow movement. Lower speed does not mean the damage cannot be extremely disastrous, even if no injuries occur. A single accident can put site operations on hold resulting in maintenance costs and productivity losses, which is why collision avoidance technologies are becoming increasingly popular in OEM designs.
"I think site managers and equipment owners are looking to do anything they can just to make the site safer and prevent vehicle accidents and worse, injuries," says Gary Cook, Black Belt II, Marketing Consultant at Caterpillar Inc., Peoria, IL, (company information, 10055175).
Somewhere in between manned machines and fully autonomous vehicles lays the advanced software systems for collision avoidance. "With the advances of the automotive industry and what it is doing now with safe following distance tracking, lane departure notifications, etc., we [have gotten] a lot of interest over the last few years in having our machines be able to do that. It seems to me that it's getting to the point where mining customers want an autonomous truck with an operator in it—automatic functions that command the truck to slow down, speed up or remain stopped. That's how customers are driving this technology," says Cook.
Caterpillar's Detect on-board vehicle technology suite gives operators better visibility, object detection sensing and increased proximity awareness through satellite location capabilities. Detect falls under Cat's MineStar System (learn more, 10815623), a broad and integrated operations and mobile equipment management system. When there are multiple large pieces of equipment working within a defined and possibly restricted space in close proximity, a collision even at low speed can cause serious injury to operators or site workers and can result in thousands of dollars in damage and lost productivity due to vehicle downtime.
Joy Global Inc., Milwaukee, WI, (company information, 10284986) addresses another collision avoidance problem specific to a machine's interaction with itself through its Track Shield Collision Detection & Mitigation System (product information, 11296267). The system aims to reduce track-dipper impacts for its electric mining shovels (watch a video demonstrating the system in action at www.oemoffhighway.com/11296292). As shovels got bigger, the problem of the dipper's range of motion allowing it to strike the tracks became more prominent. "That's when Joy Global started thinking about how to address the challenge to see if there was anything we could do on the OEM level in terms of machine design and technology products to address the customer's problem," explains Eric Hsieh, Product Manager - Technology at Joy Global Surface Mining.
Both systems rely on precise mathematical modeling and prediction based on readings from vehicle-mounted sensory devices and work to prevent unnecessary damage, downtime and productivity losses.
Safe distance between machines
Caterpillar uses a building block approach to build its vehicles towards full autonomy. "We may start with cameras, add radar and GPS capabilities for proximity detection and keep the technology scalable," says Cook. "A scalable approach allows us to give a customer the level of collision avoidance detection they need. If they just want vision with cameras to display on an in-cab monitor, we can do that. Then we add radar to detect objects and provide the next level of avoidance with visual and audible warnings."
The next step is Proximity Awareness, a GNSS-based product system that allows the machine to see the location of the other vehicles on site on the in-cab display. If a machine's path of travel intersects with another machine's path, the operator is notified with a quick audible alert and visual information. This is especially beneficial for large mining trucks that have longer stopping distances as it allows operators to get a good look at their surroundings before moving in any direction. Speed zones and limits can be set for specific areas on the jobsite for a more advanced form of the detection system and requires a wireless network infrastructure to function.
Object detection was launched by Caterpillar back in 2010 and has had few changes to its components since. "We've made some improvements such as reducing the number of radars while retaining the same amount of coverage, but mainly in terms of improvement we've tried to listen to the customer and improve functionalities such as eliminating a physical acknowledgement of a detection," says Cook. "The first system that was launched required the operator to interact with the screen by pressing to see what was detected. The feedback was negative on that feature, so we removed it. Another feature change was to enlarge the cameral view to occupy 90% of the screen. We've also added proximity bars to let the operator know the approximate distance of the detected object, whereas with the original detection product it only indicated a general zone location—front, left or right side, or back."
Caterpillar is working on software upgrades to be able to provide No Alarm Zones where a designated area on a map will not alarm for object detection. As a truck is backing into a covered hopper, radar is going to pick it up as an object and alarm, but with Caterpillar's zoning capability, that can be avoided.
One thing Caterpillar will not do is take control away from the operator to avoid a collision. "We are exploring the possibilities, but at the moment we do not do that. In a similar fashion, however, we do give the operator warnings and we do supply collision course information if a vehicle's path is overlapping with another vehicle; so, we'll warn you, but we will not slow or stop the machine by overriding the operator," says Cook.
While safety is the primary driver behind collision avoidance systems, there are additional benefits gained from these integrated monitoring systems. "With the proximity awareness system, we have the ability to capture incidents. Any time body-to-body avoidance occurs, the incident is available for playback and reporting. Customers will be able to use that information to track performance improvements over time," Cook says.
Protecting the machine from itself
There is related investment by the OEM to deliver collision mitigation for repeated strikes between machine parts. Common in mining shovel operation is dipper-crawler impacts which are a major contributor to reduced crawler shoe life and structural cracking. Just as with machine-to-machine collision, this eventually leads to unplanned downtime to repair or replace a shovel's shoe, pin and hardware in the short term, or more costly frame and body repairs in the long term.
"Dippers are increasingly becoming larger and deeper. Mining operations in applications such as oil sands require wider tracks to accommodate floatation," says Hsieh. "Under these circumstances, it is difficult even for the most experienced operators to avoid repeated dipper-track strikes." The Track Shield system allows operators of any skill level to optimize cycle time and productivity, as well as assisting new operators by reinforcing best digging practices.
Joy Global's Track Shield Collision Detection & Mitigation System helps electric mining shovels avoid dipper-track collisions through predictive modeling. The Centurion® control system runs Joy Global's electric shovels. "It translates the shovel operator's control signals into the controller and turns them into commands for the motors to act," explains Hsieh. "Track Shield is an industrial computer along with a couple of additional sensors that stands as a middleman between the operator and the motion of the shovel."
In cases where no collision is detected—and Track Shield has a two second predictive window of where the dipper is expected to be—then the operator's input is passed directly through. If a collision is detected, the system will not interfere if it calculates that an operator has adequate time to adjust the trajectory of the dipper. Once it is determined that there is not enough time for the operator to avoid the collision, the system will determine the best motion (typically hoist) to lift the dipper out of the way of the tracks in a minimally invasive way that has the least amount of momentum reduction.
"Momentum and flow is really important in terms of shovel operation, and when that momentum is interrupted, the shovel's productivity is affected," Hsieh says. "Even if there is no direct damage or no significant damage to the tracks, if a dipper hits the tracks during a dig cycle, the interruption causes an operator to have to reposition the dipper and change the trajectory in order to have the appropriate momentum for the cycle to finish. Track Shield can mitigate that pause in the operation."
The system does not prevent collisions, however, clarifies Hsieh. Many times, an operator of an electric mining shovel has to dig extremely close to the tracks. A system that completely prevented any minor touch would not be accepted in the industry. "We had to make a compromise somewhere and tune our system to mitigate the strongest collisions and the most impactful in terms of energy of the collision. That is tunable according to the mine's practices because different mines with different commodities in certain geographic regions and company cultures will adjust to their specific needs," Hsieh says.
The reality is the operator is in control the entire time, and if an operator is working close to the tracks and the kinetic energy is not as high as if the dipper handle is rapidly coming down toward the tracks, it is possible to hit the tracks. "We're a lot more tolerant because the speeds and the kinetic energy are lower when an operator is just cleaning up around the tracks or doing fine digging," Hsieh clarifies.
"We are not displaying for the operator where the dipper is in relation to the tracks. Track Shield is not that kind of system. We trust the operator is going to get the dipper in the right place but may need help with blind spots." So, the controls for Track Shield are integrated into the shovel control screen in the options menu. "It should be mostly transparent to the operator running in the background," says Hsieh.
Currently Track Shield is specific to Joy Global's Centurion System, not transportable to other OEM shovels, but the company is currently working on a project to develop shovel-to-other-machine collision avoidance. It is safe to say that collision avoidance technologies are becoming almost expected by industry vehicle operators, but it should be clarified that these systems will never replace standard safety and operating procedures.