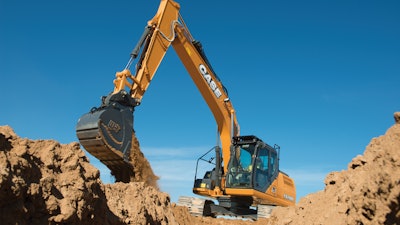
Many of the features on the most recent generation of excavators enable semi-automatic operation of critical functions. This increases operator efficiency and productivity.
“Grade control is quickly moving into the construction industry like a hurricane,” says Adam Woods, Manager of Innovation and Technology Integration, LBX. “Link-Belt recognizes this and has developed an integrated grading solution powered by Trimble Earthworks, called Link-Belt Precision Grade. The system works in unison and is seamlessly integrated into our proprietary hydraulic system, which is called Spool Stroke Control.
“Link-Belt Precision Grade was developed and launched for many purposes, but curbing the impending labor gap was one of them,” he continues. “With more of the seasoned operator force retiring, the industry will see an increase in a younger generation coming in to fill those positions.” With this comes a need to educate, train and learn. This is where the integrated grading solution comes into the picture. “Taking new operators and getting them to productivity levels of seasoned operators in a matter of hours and/or days, Link-Belt Precision Grade looks to cut the learning curve to get customers productive and efficient as soon as possible.”
Automated features are a great tool for newer or less skilled operators. “It helps them maintain grade by aiding them once the bucket has reached grade and [allows them to] get the feel for it,” says Ryan Neal, Market Professional, Caterpillar Inc. “And for skilled operators, it is another tool in their belt. If they already understand reading the grade stakes and have a feel for depth and slope, this will only advance them in being more accurate for longer periods of time and help with operator mental fatigue.”
Automation Aids Accuracy
Standard Cat Grade with Assist automates boom, stick and bucket movements to deliver more accurate cuts with less effort. The operator simply sets the depth and slope into the monitor and activates single-lever digging.
“We offer our Cat Grade with Assist on most of our lineup, from the 313 to the 352, as standard,” says Neal. “It enables the operator to maintain grade and keep the operator more accurate and less mentally fatigued from digging on grade all day. We have a standard 2D solution for those who want to maintain a specific depth, as well as a 3D solution from the factory or from a SITECH dealer.
John Deere has simplified operation with SmartGrade technology. “We’ve equipped the 210G LC, 350G LC and 470G LC with SmartGrade to give operators at entry level of experience the ability to achieve grade quickly and confidently,” says Justin Steger, Solutions Marketing Manager, Site Development and Underground. “By controlling the boom and the bucket, this semiautomatic technology frees up the operator to concentrate on the arm function, resulting in fewer periodic grade checks every time. SmartGrade technology will make novice operators good and good operators great.”
Komatsu’s intelligent Machine Control (iMC) excavator allows the operator to focus on moving material efficiently while semi-automatically tracing the target surface and limiting over excavation. “Starting with our PC210LCi-11, we’ve launched iMC 2.0,” says Andrew Earing, Product Manager for Tracked Equipment. “With iMC 2.0, we’re going to be offering the bucket hold control as well as optional auto tilt bucket control, two primary features that are going to help with overall productivity and efficiency on the jobsite.”
Bucket Angle Hold and optional Auto-Tilt control are newer features on Komatsu iMC excavators. With Bucket Angle Hold, the operator sets the desired bucket angle and the system automatically maintains the angle throughout the grading pass. Auto-Tilt control automatically tilts the bucket to the design surface and returns it to horizontal to unload.
Auto Tilt control boosts jobsite efficiency. “No longer do you have to move the machine every single time you want to make a finish grading pass,” says Earing. “You can now do that from one position and still grade the surfaces with very high precision.”
Auto grade assist makes it easier to hit grade. The operator moves the arm, and the boom adjusts the bucket height automatically to trace the design target surface. This allows the operator to perform rough digging operations without worrying about the design surfaces and to fine grade by operating the arm lever only.
As a first step toward automation, CASE Construction Equipment entered the realm of factory fit machine control with its D Series excavators earlier this year. You can now order and take delivery of a Case excavator with 2D or 3D excavation system already installed and tested by the OEM.
“What we are doing here is matching, installing and testing 2D and 3D systems from Leica Geosystems with Case D Series excavators up to the CX 350D,” says Nathaniel Waldschmidt, Product Manager - Excavators. “It massively simplifies the acquisition process.
“Machine control has the ability to transform the productivity, efficiency and long-term profitability of excavators,” he continues. “We’re now making the addition of machine control with excavators completely turnkey, allowing contractors to experience those benefits in an extremely seamless experience with their Case SiteControl Certified dealer.”
Measurable Productivity Improvements
Tests performed by several of the major excavator OEMs demonstrate impressive productivity enhancements when implementing semi-automated grade control functions.
“In a controlled planar slope grading test, we measured speed and accuracy for a novice and experienced operator in manual mode vs. [John Deere’s] SmartGrade 3D control. The results were SmartGrade made the novice operator 90% more accurate and 34% quicker. It made the experienced operator 58% more accurate and 10% quicker,” says Steger.
Productivity and efficiency studies show gains that are hard to ignore. “When we’ve done case studies in the past, we find anywhere up to 63% improvement in time,” says Komatsu’s Earing. “The reason we are able to get there is this technology greatly reduces or even eliminates staking. Grading is much more efficient, and inspection can literally be done with this technology instead of having to bring somebody back out on site.” As-built verification can be performed by the excavator. “Overall, the time savings are huge.”
The technology also greatly compresses the learning curve. “The days of waiting months and years for new operators to gain the skills required to cut accurate, precise grades are gone,” says Woods. “Months and years now become hours and days with the help of Link-Belt Precision Grade semi-autonomous Machine Control and indicate Machine Guidance systems.”
The technology shortens cycle times, as well. “By relying on the machine and system to do all of the exact calculations and thinking, the operator can get into the dig and out quicker by allowing the machine to do the fine grading function for them,” Woods explains. “With the system always staying on the operator’s correct depth and slope path, the function is completed more efficiently without guesswork.
“Productivity has been tested and studied to show improvements as high as 50%, depending upon the job application,” he notes. “Automation clearly takes the guesswork out of the task on the jobsite, allowing operators to focus on other things. Automation also enables jobsites to function without the need for additional surveyors and grade checkers within the working area. This vastly reduces the chances and risk of bystanders being injured during previously routine operations.”
Over-dig Protection Equals Large Savings
The lost productivity and excess material costs associated with over excavation is a major cost driver on many jobsites.
“With thousands and sometimes tens of thousands of dollars lost to over digging...to things like backfilling materials needed, time lost over digging and time spent checking accuracy and grade, over dig protection can save money,” says Woods. “In addition, with some businesses being pushed into ‘the red’ because of miscalculations, which hit the businesses’ bottom line, some companies may stay afloat thanks to over-dig mitigation.”
Having to continually monitor progress to grade and possibly slow down as you approach final grade is counter-productive, so Link-Belt offers over-dig protection technology, as well. “Over-dig protection keeps operators performing at their max potential, reducing the need for as much expensive backfill materials and mitigating the issue of lost time, fuel and wear and tear on the machine digging beyond grade unknowingly,” Woods explains.
John Deere has two features that automatically serve as a defense mechanism against time wasted by digging too deep. “The first is Overdig Protect, a safeguard for the design surface that prevents the operator from digging beyond the engineered plan,” says Steger. “The other is Virtual Front, a stopping of the bucket cutting edge before it contacts the front of the machine at an operator preset distance.”
The Cat Grade with 2D system automatically guides digging depth, slope and horizontal distance to quickly and accurately reach desired grade. Users can program up to four of the most commonly used target depth and slope offsets so the operator can get to grade with ease. Best of all, no grade checkers are needed so the work area is safer.
Cat Grade with 2D system is upgradeable to Grade with Advanced 2D or Grade with 3D to increase productivity and expand grading capabilities. GRADE with Advanced 2D adds in-field design capabilities via an additional 10 in. high-resolution touchscreen monitor. GRADE with 3D adds GPS and GLONASS positioning for pinpoint accuracy. Plus, it’s easier to connect to 3D services like Trimble Connected Community or Virtual Reference Station with the excavator’s built-in communication technology.
Komatsu’s iMC technology utilizes 3D design data loaded in the control box to accurately check its position against the design target grade. When the bucket reaches the target, the software prevents the machine from being able to over excavate.
This factory-installed integrated intelligent machine control system comes standard with stroke-sensing hydraulic cylinders, multiple Global Navigation Satellite System (GNSS) components and an Inertial Measurement Unit (IMU) sensor. The stroke-sensing cylinder provides accurate, real-time bucket position information to the large in-cab monitor, while the IMU reports the machine orientation.
The iMC technology does require 3D models. “The direction that we’ve gone as a company is to be able to make any 2D site into a 3D site,” says Earing. “The entire industry is moving toward 3D. We know that is the overarching future of this industry.”
John Deere offers four grade management options: SmartGrade, SmartGrade-Ready with 2D, 3D Grade Guidance and 2D Grade Guidance. Upgrade kits for each option enable customers to adopt the technology at their own pace.
“By incorporating precision technology such as SmartGrade on our excavator lineup, we are boosting jobsite productivity and efficiency while enhancing the capabilities of our operators,” says Steger. “However, there isn’t a one-size-fits-all solution, and contractors need options to pair the right technology with their business needs. This is where customers really benefit from the flexibility of our grade management path.”
The SmartGrade excavator automates the boom and bucket functions, allowing the operator to more easily achieve an accurate finish grade. The system uses GNSS positioning technology for accurate horizontal and vertical positioning.
Defined Work Area Improves Safety
By always understanding exactly where the boom and bucket are positioned on site, such technology can be used to restrict the defined operating area and give operators warnings if they are approaching areas with obstacles, such as overhead power lines, buildings, walls, etc.
“Automation in excavators has come a long way,” says Neal. “Our Ease-of-Use features can create a ‘safety bubble’ around the machine that will help prevent the machine from striking an object, as well as keeping people safe around the machine. We have the ability to create virtual ceilings above and below the machine, in front of the machine and side to side, as well as cab avoidance.”
In addition to standard cab avoidance, Caterpillar provides a 2D E-Fence that keeps the front linkage within a predefined work area to avoid hazards on the jobsite. Whether you are using a bucket or hammer, standard 2D E-Fence automatically stops excavator motion using boundaries set in the monitor for the entire working envelope — above, below, sides and front. E-Fence protects equipment from damage and reduces fines related to zoning or underground utility damage. Automatic boundaries even help prevent operator fatigue by reducing over swinging and digging.
John Deere utilizes similar technology. “In addition to keeping the jobsite running efficiently and uptime at an optimal level, Virtual Ceiling, Virtual Floor, Virtual Swing and Virtual Wall monitor the machine’s surroundings,” says Steger. “As opposed to hydraulically limiting the machine, these virtual fence features audibly and visually alert the operator as the machine approaches the set limits.”
Expect Increasing Accuracy in Future
Automation technology is advancing at a rapid pace. As to where will it go in the future, increased accuracy seems to be a common theme.
“The most important innovation in automation would be accuracy,” says Neal. “If it’s not accurate, then there is not much advantage in the technology. And this technology is only going to get better and have better accuracy, more options, training tools, etc. I feel like the sky is the limit.”
Steger agrees, noting, “Over time, we’ll likely see grade management systems across more machines with even better accuracy. There’s always opportunity to automate more functions of the dig cycle, as well. The future is bright for this technology.”
Could full automation be on the horizon? “With systems in the industry today being semi-autonomous, meaning the system still requires an operator presence, one could assume and expect the future to include a fully autonomous worksite,” says Woods. “The future of this technology and our industry is limited only by the imagination and individuals within it.”