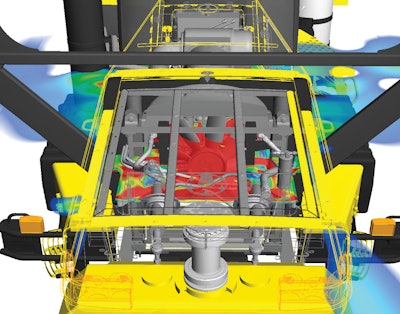
NVH (noise, vibration, harshness) is a common problem inherent to the base architecture of a vehicle. If it is ignored until the end of design, the tests run to find noise sources are only pinpointing “band-aids to put on the vehicle,” making the problem significantly harder to solve, says Steve Mattson, Chief Engineer at GLSV (company information, 10909374), Houghton, MI. Proper planning in the early stages of development can help address and mitigate noise and vibration issues. Factors to consider early in the process include adequately sizing a muffler; keeping in mind how air comes into and leaves a vehicle, and addressing noise control solutions on those penetrations; and considering the amount of room needed for a component or system to move around and isolating those significant forces.
On a wheeled vehicle, you can “almost always guess what the problems are going to be before you even get started,” Mattson continues. Four systems are the most common sources of noise on wheeled vehicles: exhaust, air intake, fan cooling systems and the engine mount system to the chassis. With those four systems typically high on the list of probable noise sources, the vehicle is then run through a pass-by test which measures and collects data on characteristic frequencies of sound and how they are distributed over the vehicle. “Then we look at the noise signature in detail in a spectrum which shows us noise energy distributed across frequency. It indicates the frequency of the noise that’s driving the overall level, which gives us clues as to which component is emitting the noise,” Mattson explains.
Solutions are either found jointly with the customer with a specifically designed system solution, or a commercial solution is used if possible. “If there is limited space for the muffler, you can end up with an oddly shaped component that has to be optimized for noise reduction needs. Often because of other prioritized design needs of the vehicle, a catalog solution is not a realistic option.
“One thing that has been very eye opening to me has been the general lack of exposure to the process of solving vehicle noise problems,” says Mattson. A systematic approach of diagnosing noise sources and addressing them based on their level of dominance until the noise level objective is met is typically followed, yet Mattson admits, “There is a lot of teaching of the process to put an appropriate plan together to achieve particular noise levels. There is a balance to achieving the customer’s noise requirements through selectively reducing each noise emission source by a given amount.”
Simulated diagnosis
Exa Corp. (company information, 10909378), Burlington, MA, provides analysis software to be used for simulated acoustical diagnosis. PowerFLOW creates high accuracy detailed simulations deciphering pressure fluctuations. PowerACOUSTICS is a post-processing analysis software for analyzing the results of the PowerFLOW solver simulation (product information, 10909387). “The two software applications work together,” says Dave Freed, Senior Director, Aeroacoutics Applications, Exa Corp. “We have several ways to analyze and visualize both the flow and pressure fluctuations using PowerACOUSTICS in time and frequency domains. When in the frequency domain, it is referred to as spectral analysis which allows you to see behaviors happening as a function of frequency, a very common analysis capability for NVH engineers,” he continues.
The company’s PowerACOUSTICS software contains three modules for specific types of sound analysis. The Signal Processing Module (SPM) allows for band filter pressure analysis to see what happens to pressure at specific frequency bands.
There are also two advanced analysis modules. One is the Interior Noise Transmission Module (NTM) which allows the transmission of acoustics through solid panels into the cabin of a vehicle virtually. The other is the Far-Field Noise Module to evaluate the noise at a particular distance from the vehicle.
Cooling off Tier 4 NVH
With the implementation of Tier 4 Final regulations for off-highway equipment looming, engine exhaust aftertreatment systems are placing increased loads on the cooling system, which in return is causing customers to use larger fans and rotate fans at higher rates of speed, leading to new NVH challenges. “We’re doing a lot of work with the off-highway engine cooling requirements,” affirms Doug Hatfield, Managing Director of Heavy Vehicles, North America for Exa Corp., Burlington, MA.
By letting the customer know what the dominant noise source is, such as the cooling system, the customer can spend more time shopping for the appropriate fan and comparing system design and its effects on spectator or operator noise with Exa’s software. “They can also determine what the influences of other underhood components are to the fan to create noise, such as the positioning of the fan within the shroud, the design of the hood enclosure or anything else that could alter the flow and thus alter the predicted flow-induced noise,” says Kevin Horrigan, Director, Application Engineering, Heavy Vehicles Group, North America, Exa Corp.
“The exhaust system is an extremely important part of the noise profile and an area where we can provide a lot of value simulating its flow and noise performance,” says Freed. The customers use Exa’s software to create complete solutions. “Typically it starts with building a model that takes the system’s detailed geometry into account. We work with native CAD geometry and build up a model of the entire system. This provides the highest level of accuracy for the prediction of the flow and acoustics,” says Horrigan.
Exa’s PowerFLOW system is not only able to predict noise of the cooling fan and exhaust system, but also temperatures of the radiator coolant, charge air cooler, oil coolers, as well as surface temperatures of components that are heat sensitive.
For the cooling system fan specifically, there are low hanging fruit noise reduction solutions. For example, if the flow path can be improved and parasitic losses can be reduced, fan speed can simply be slowed to achieve less noise, as long as underhood cooling requirements are still met. So what can be modified to achieve cooling requirements with reduced fan speed? “Optimizing the shape of an underhood shroud on the cooling module to reduce pressure losses is one way to meet requirements,” explains Horrigan. “You can alter the grill design to reduce pressure losses, too.”
There are still customers looking to use external insulating materials. “Part of the value we hope to provide is to improve the flow-induced noise to make the customer less dependent on adding cost, weight and potential thermal problems from having to add external acoustic absorbers in the compartment. However, if they still need to add acoustic absorbers, that is something we can include in our simulation to help them understand what sort of layout and material type is going to give them the additional absorption they are going to need,” says Freed.
There have been a number of NVH issues that have arisen from dust ejector systems on heavy equipment. Several OEMs have exhaust systems which utilize the low pressure created by the exhaust system to connect up with the air intake system and filter dust out of the engine combustion air. The flow design of the system can often lead to high flow velocities and consequently high levels of noise associated with the turbulence.
In addition to trying to find ways to improve the overall flow performance, another possibility is to identify unwanted interactions of turbulence induced by the fan based on fan installation in relation to the surrounding geometry. “It’s an important opportunity,” explains Freed, “because if you can identify that, you have a chance to identify the geometry problem, move things around and get a real noise benefit. It’s essentially cost free since you’re not adding materials or absorbers. Of course, there are constraints associated with shape, but very often a modest geometry change can offer a significant benefit.”
Eventual capabilities and demands
Exa’s software suite offers customers with the unique value proposition to be able to handle both flow and acoustics. “Where our customers find a lot of value is getting the flow and acoustics analysis together. We can draw more relevant conclusions because we are taking more conditions into consideration, and there is a strong relationship between flow and acoustics,” says Freed. “We are asking the customer to make million-dollar decisions based on our results, so they have to believe in the accuracy and the predictive capabilities."
And while the PowerFLOW and PowerACOUSTICS software offers well-rounded diagnostics and analysis support for the applications of today, Exa is investigating ways to enhance its product line for the applications of tomorrow. “There is a concept in the industry called TPA, transfer path analysis, and we’re working to expand our software platform to allow that complete TPA,” Freed says. “That includes not just flow-induced noise, but pulls in other noise sources and does a complete analysis of where all of the noise contributions are coming from, what they are, and where the most value lays for noise reduction.” The ability to include non-simulated noise sources, such as structural panel vibration or pump movement, to predict overall noise sources that go beyond aero-acoustic or flow noise is a logical next step in NVH reduction solutions. The non-simulated noise sources would be pulled in from test data and previously performed estimates based on simulations.
Along with more data to analyze, the customer is expecting it faster than ever. Currently it takes approximately one week to go from a CAD file to a result with Exa’s existing software, but there is increasing pressure from clients to get answers faster. “We have a number of ideas in the pipeline to take preprocessing time from five days to a single day,” says Hatfield.
“That level of automation and fast turn-around time opens the door to easier optimization,” Freed says. “At that point, an engineer would be able to ask for an entire series of runs with a wide variety of parameters and in a few hours would have a report which shows which parameter set gave the best results.”
As with the auto industry decades ago, once an operator discovers a quality parameter like the joy of peace and quiet, it becomes a standard expectation, regardless of whether a government regulation requires it or not. It takes one company to make the investment in significant noise reduction for internal operator comfort and safety, as well as external pass-by noise pollution, for it to become the essential competitive advantage when making a purchasing decision.