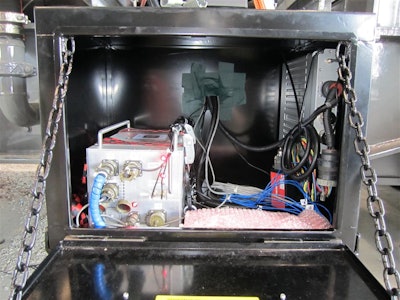
On the surface gaining access to equipment operating data seems simple enough. Prepare the mining truck with strain gages, accelerometers and other sensitive data collection instrumentation, record the forces as the truck is filled with dirt, rocks, gravel or coal and run the analysis to determine the results. While this might seem like a straightforward approach, the fact is that such short-term or controlled tests often bear little resemblance to what actually goes on when the camera isn’t rolling. For example, knowing they're being observed, load operators might take extra care when filling the truck. While other times they might be less cautious crashing the bucket into the side of the truck bed, exceeding recommended load capacity, or dropping the load with greater force from a higher release point. At the same time equipment usage and its reaction to the environment can vary greatly depending on the operator, environmental conditions, location and any number of other factors.
While one can assume the normal operating conditions of virtually any piece of machinery, there are certainly occasions when equipment experiences an event outside of the range for which it was designed. For example, the drivetrain assembly of a fast-moving mining truck collides with a protruding boulder, an engine mount unexpectedly fails leading to excessive vibration, a front-end loader attempts a maneuver for which it was never intended, and so on. Observing performance over extended time periods in the system’s natural operating environment helps to ensure the likelihood of capturing the full range of conditions to which equipment is subjected - including rare but significant events. Armed with this information manufacturers can better quantify and predict future performance and develop products that satisfy the complete range of actual customer usage.
So what’s the problem?
For all of its advancements, the challenge that the testing community has long faced has been with observing the normal, daily operation of a piece of equipment in its natural environment over an extended period of time – a process that would include the collection of massive amounts of data. After all, physically manning test equipment all day every day simply isn’t practical.
Long-term unattended data collection was not limited by hardware. A number of rugged, portable and compact data recording systems have been available for some time now. Rather, the issue lies with recording software. Limited storage meant that long-term testing required constant data downloads. This could mean continually interrupting operation and/or frequent and costly on-site visits by engineers or technicians download the data and check to ensure that quality data is being captured.
Unattended Data Acquisition & Analysis
Today there is a way to move high sample rate structural tests, which were previously limited to a laboratory, out of the simulation setting and directly onto equipment in the field, where more authentic measurements can be gathered. Among the key advantages of this integrated testing approach is the ability to gather a month or longer snapshot of high-frequency data measuring such things as vibration and strain through dozens of channels, and all from a single site visit for the initial install.
Unattended Data Acquisition and Analysis provides the ability to gather, process, and interpret terabytes of data captured during months long, high-frequency tests of equipment on the fly. As a result of these deep-dive testing and analysis methods, manufacturers are gaining invaluable snapshots of in the field stresses that can then be used to troubleshoot equipment failures, tweak product designs or even adjust validation tests to more accurately reflect real world environments. This long-term approach to field testing and analyzing off-highway and construction equipment provides engineers with a far more complete picture of the actual environment and stresses that lead to structural failures.
How does it work?
Employing sophisticated testing software, the system captures and streams data to a portable USB hard drive with on-board analysis results files and data plots uploaded to a cloud server. Within minutes of a data set being recorded results can be viewed or downloaded on a PC or mobile device. Allowing data to be remotely accessed, downloaded, and checked provides a whole new level of visibility and control. Furthermore, the two-way communication process allows testing to be modified without visiting the site or interrupting the operation.
In the past, testing was limited to collecting only low frequency data. Today, one might need to sample at a rate of 5,000 Hz (or 5,000 data samples per second). Now employing an unattended testing approach a tremendous amount of data can be sampled, up to 30-200 channels, taken over weeks or months and stored on the equipment for analysis. This has ramifications throughout a wide variety of industries: off-highway, construction, aerospace, transportation, medical and so on. In fact, it’s difficult to imagine an industry where unattended testing will not have an impact.
As an example: The recent announcement of tighter Tier 4 emissions standards sent the off-highway industry scrambling for answers: How are exhaust treatment systems best mounted on equipment? Will the design/structure withstand long-term engine vibration and operating conditions? What is the normal and extreme range of conditions to which the exhaust treatment system be subjected? To what degree will electronic components withstand vibration?
Because engines and electronic emission control components are subject to different environments, operation and vibrations, a way was needed to determine the best design for mounting the emission control system to the engine. Accurate long-term field data was needed to create baseline data for simulation, laboratory, mass table testing and accelerated testing. This proved to be an excellent application for unattended testing. With this detailed information, off-highway manufacturers can incorporate the necessary changes to meet rigid emission standards without introducing new mechanical problems.
Putting the Data to Work
When testing a new line of off-highway equipment, such as mining trucks, the manufacturer might want field data to enhance the design of a particular component. Hundreds of thousands of data points can be reduced from weeks of testing into a report that allows the manufacturer to quickly see rare events such as off-the-charts vibration levels that could potentially cause a failure. That point can be isolated in time to interrogate any of a hundred other channels recorded and do enough data mining to explore exactly what else was occurring in the vehicle to help pinpoint the problem.
Real-world operating data, collected in a product’s natural environment, continues to be the best source of baseline information needed to validate designs. Simulation applications allow designers to quickly and accurately evaluate a large number of design alternatives while ensuring that durability, quality, production and time-to-market targets will be met. The process is critical to ensure that components, sub-assemblies and assemblies are designed to meet the requirements for which they are intended and guard against over-design (resulting in excess material, weight, and cost) or under-design (leading to failure, safety issues and excessive warranty claims).
For manufacturers and suppliers in the off-highway equipment industry, extended data sample sets provide a far more accurate representation of how a product will react to forces, vibrations, heat, fatigue and the occasional anomaly than data collected through a tight window. Unattended testing provides the solution to capturing the quantity and quality of data needed to drive today’s accelerated product development processes.