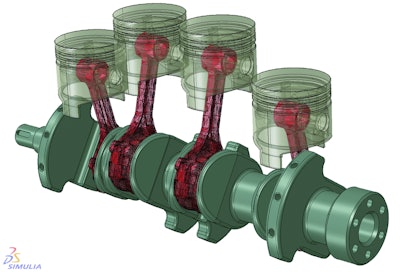
Dassault Systèmes (DS) a world leader in 3D and Product Lifecycle Management (PLM) solutions, announces the availability of Abaqus 6.10 Extended Functionality (6.10-EF), a unified Finite Element Analysis (FEA) and multiphysics product suite from SIMULIA, the Dassault Systémes brand for realistic simulation.
- Delivers a number of powerful, customer-requested enhancements for modeling, visualization, contact, mechanics and performance
- Improvements enable customers to reduce development time and costs, while increasing the efficiency of the product development process through highly accurate simulations of real-world product and material behavior
- Modeling and visualization enhancements in 6.10-EF improve support for substructure modeling capabilities
- Easily create a substructure of a distinct region in a product, import it into an assembly, recover the results during an analysis, and reuse the substructures in future models
- Provides new contact and mechanics capabilities that improve the efficiency and accuracy of simulating real-world performance of designs, including fluid leakage between 3D bodies in contact
- Support for 3D pressure penetration loading can now be used with any contact formulation, allowing for higher-fidelity simulation results
The latest release also expands the capabilities of the Extended Finite Element Method (XFEM) in Abaqus, allowing users to predict crack growth due to low-cycle fatigue, such as with thermal analysis of the heating and cooling phase that occurs in an engine exhaust manifold. This capability can also be used to accurately predict the durability and damage tolerance of composite structures with complex failure mechanisms.
"The implementation of the Extended Finite Element Method (XFEM) within Abaqus provides us with a means to calculate stress intensity factors without explicitly modelling the defect,” stated Ian Symington, senior consultant at Serco, Technical Consulting Services. “This approach has the potential to save significant time during the mesh generation phase and reduce the prolonged effort usually associated with undertaking fatigue crack growth assessments."
Abaqus 6.10-EF also provides significant performance enhancements, including a new scalable, parallel execution capability within the AMS eigensolver, which significantly accelerates frequency extraction analyses required to study Noise, Vibration, and Harshness (NVH) behavior in vehicles. SIMULIA’s four-core AMS eigensolver is estimated to be 1.5 times faster than competitive solutions.