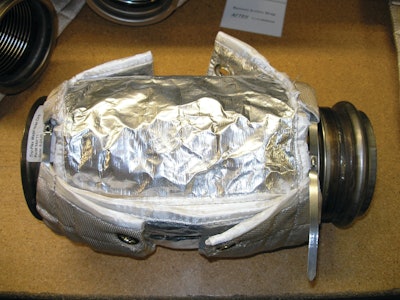
The additional components in the engine system used to meet emissions regulations have pushed system designers and equipment manufacturers to get creative on design and layout configurations. “Anything you can do to minimize the footprint of the engine package is going to be beneficial to the OEM,” says Mike Teso, International Business Development, Tru-Flex Metal Hose, LLC, West Lebanon, IN.
According to 2013 emissions standards for on- and off-highway vehicles, exhaust systems are required to be leak-free from the turbocharger through the treatment system. The standards also place stringent requirements on heat loss, limiting the amount of heat loss form the turbocharger to the inlet of the diesel particulate filter (DPF) by an additional 10 F. Current EPA regulations allow a temperature drop that does not exceed 35 F, whereas in 2013, heat-loss tolerances will be limited to 25 F.
“Temperature is only allowed to drop by certain temperature percentages because if it goes into the emissions treatment system and isn’t as hot as it needs to be, the system can’t eliminate the NOx or soot as effectively as it could,” explains Teso.
To meet emissions standards, leak requirements and heat-loss tolerances, Tru-Flex created its internally insulated, zero-leak torsional exhaust bellows. The internal insulation allows design engineers, who are often restricted to exterior insulation systems to regulate heat, to consolidate system design footprints while still meeting emissions requirements.
Tru-Flex did not start out manufacturing bellows. Formed in 1962, the company began manufacturing spiral-wound interlock flexible metal hose, but by 1989 the company’s president, Win Thomas, began investigating additional market segments for the company’s expansion to provide a more stable demand than the seasonally fluctuating flexible metal hose market.
“He researched the upcoming U.S. Clean Air Act of 1990 set to establish air quality standards for all on-highway vehicles and off-highway equipment and found that a corrugated product was going to be more widely used, which is how we got into manufacturing bellows,” explains Teso. “Since we got into the corrugated product market early, we had a lot of time to innovate.”
Tru-Flex today manufactures both spiral wound flex hose and corrugated bellows for the heavy-duty commercial vehicle market globally, including agricultural, construction, on-highway and military equipment. “I think once we get closer to Tier 4 Final design and on-road 2013 designs, there will be a lot of use for this part,” Teso says.
Design with a twist
Between the rocking movement of the engine and the hard mount of a flex pipe to the turbo charger to a rigid pipe exhaust system, bellows were cracking. To combat this problem, Tru-Flex developed and patented its torsional bellows. These bellows are particularly well suited for engine layouts that have exhaust outlets in parallel with the crankshaft, or that demonstrate torsional outputs that create more than two percent displacement at the site of the exhaust outlet.
The design of the product features an inner spiral wound flex hose, available in inside diameters (I.D.) ranging from 2.5 to 6 inches (63.5 to 152.4 mm), and an outer corrugated bellows. Between the inner and outer product portions is approximately 0.25 inches of free space to allow for relative movement between the two parts. It is in that free space that Scott Thomas, Engineering Manager for Tru-Flex, decided to put the system’s insulation. The internal insulation does not impede the system’s movement, S. Thomas notes, and actually enhances the fatigue life of the exterior torsional and non-torsional bellows by reducing their exposure to superheated exhaust gases.
The portion of the insulation that comes in contact with the flex liner is a woven material to prevent any fibers from the insulation from getting into the exhaust stream. “Over time, as the system vibrates, the concern was that fibers would migrate into the exhaust stream, so we added the extra layer of woven material to our internal insulation to prevent it,” explains S. Thomas.
“There are also vibration damping benefits achieved by putting insulation between the flex hose and bellows,” says S. Thomas. The dampening effect of the internal insulation provides a 70% noise reduction over non-insulated systems, greatly enhancing operator comfort.
The elimination of the external insulation system—often blanket-like wraps made of thick insulating material structured around a metallic wire lattice—reduced overall system space while maintaining its heat-loss tolerances. An external blanket’s wire mesh can, over time, cause wear on the bellows, and the insulation material itself exposes the engine exhaust system to corrosive moisture and debris that can cause system failure.
Tru-Flex’s internal insulation material never requires replacement like external insulation which can decompose over time from environmental elements. “We’ve been told by two different engineering groups that the failure rate of an external blanket is about nine months to a year,” says Teso. “This consolidated, leak-free, engineered system reduces OE acquisition cost on the front end and their exposure to warranty and replacement issues on the back end,” confirms W. Thomas.
A smaller, more consolidated engine system package is important to any OEM dealing with less under-the-hood space. Tru-Flex’s innovative leak-free torsional bellows with internal insulation offer a creative solution to a challenging emissions requirement.