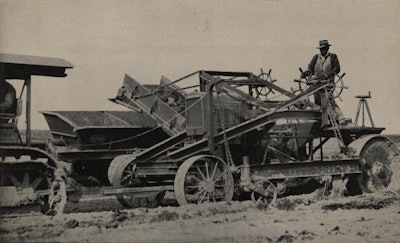
Let’s continue our look at how Stroud Road Machinery Company of Omaha, Nebraska, trained salesmen to promote its elevating graders in 1930 and 1931.
Originally, an elevating grader’s conveyor was powered by chains or tumbler rods, connected by u-joints, from its back axle, and the rear wheels were cleated for traction. Stroud used chains because they were simple, efficient, flexible and easy to service. But compared to chains, tumbler rods were more expensive to buy and maintain, used three times as much power, and had to be disengaged when the conveyor was raised or lowered as sometimes had to be done while loading.
A drive shaft from a power take-off (PTO) came into use with tractors strong enough to pull and power these machines. The angle of the universal from the tractor PTO to the grader drive shaft ranged from 12.5 degrees to 20 degrees on competitive machines; but for Stroud's, it was only 5.5 degrees for Cat or Monarch tractors and even less for Cletracs. The lower this angle, the more efficient the transmission of power to the grader, and the less thrust was placed on the bearings on both the grader and the tractor when traversing rough ground.
By mid-1931, onboard engines were the power of choice for elevating graders because of their greater productivity. Stroud recommended purchase of a new engine grader to replace an older one, rather than retrofitting. But because dealers usually sold both tractors and elevating graders, salesmen could be tempted into trying to sell a contractor a new, larger tractor and a PTO or traction grader rather than only an engine-powered grader suited for his existing smaller tractor, such as a Cat Sixty. Stroud warned that savvy buyers would see through this and go elsewhere to buy only the engine grader they wanted. The strategy Stroud recommended was to sell the engine grader now and, when the buyer saw how much more dirt he could move with it, he would come back to the Stroud dealer for a new tractor when the time came because he was so pleased with the grader.
PTO drives could also be retrofitted to traction graders at a cost of $450 or $550 depending on the age of the grader, and traction and PTO elevating graders could be retrofitted with engines. If special parts were needed due to frame damage or standard parts not fitting, the owner was responsible to provide his own parts, and credit would be given for factory parts not used. Stroud retrofits could be used on competitive machines, but only at considerable expense.
One man working alone in the field without a good machine shop could perform a retrofit in a couple of days, and Stroud offered to send a factory service rep to repower their machines for $7 per day plus travel expenses. Some contractors tried their own retrofits, but ended up with unsatisfactory, crude-looking, jury-rigged affairs, often at far higher cost than a factory retrofit.
Stroud engine and PTO graders could also be equipped with traction drive for use in event of engine failure, rather than shutting the grader down until repairs could be made. It added $275 to the purchase price, but keeping the grader working with a dead engine made that up in a day or two.