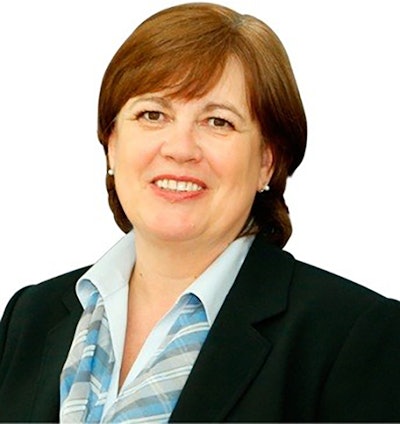
GLOBAL ECONOMIES
What economies are your primary international targets for new investments and continued growth?
Eaton is a global company with local reach, operating in every market around the world. Developing and investing in a worldwide presence continues to be a priority.
GOVERNMENT
What government regulations, standards or bills were passed in the past year that most affected the way you do business and go to market?
Many regulations around the world have been passed with goals to achieve reductions in energy consumption – in the U.S., we have Horizon 2020 and Productivity 2030. In Germany, we have Industry 4.0. China has also set some aggressive energy reduction goals.
These government-supported programs are looking to drive change in manufacturing and ultimately reduce the energy consumption in manufacturing, a trend impacting companies across many industries. This change is a part of business, and Eaton remains adaptable and flexible to meet the needs of our customers while following all regulations.
DIVERSIFICATION MARKETS
Any new products on the horizon for new markets to broaden your market reach?
Our primary focus has been on digitizing our portfolio and embedding computational HP on many of our individual components. Eaton’s advanced mobile valves are among the most advanced intelligent valves available on the market today. Our Pro-FX Electronic Controls and Software provides a complete suite of electronic components and a software architecture connecting them all together, helping customers in the mobile off-highway equipment market create custom control solutions for precise and efficient machine control. Of course, we also have intelligent solutions for industrial markets, such as the AxisPro valve, which partners flexibility, reliability and simplified diagnostics for a wide range of industrial applications.
What particular markets are NOT looking like opportunities anymore, and why?
Many markets are currently going through swings, and while one segment may not look as attractive today, that does not mean that the segment will not show promise tomorrow. Eaton is working to take advantage of the R&D opportunities across many markets.
TECHNOLOGY OF THE FUTURE
Are you seeing a shift toward overall part reduction and system simplification? If yes, how are you participating in this movement?
Reduced parts and simpler systems fit into a broader goal of creating systems that are more effective, more efficient and safer. These high-level design goals closely describe the mission statement of Eaton’s Hydraulics Group – so while we are certainly experiencing this shift, Eaton does not see the development as new. Improving the effectiveness of machines, which in many cases includes simplification, is a longer standing goal that has been in play for some time on the system level.
As the industry has become more digitized, with more embedded electronics, Eaton has been working to embed electronics and controls into our products. For example, adding a capability to put logic variation onto hydraulic components such as valves, pumps and more. As purely mechanical hydraulic systems give way to electrohydraulic systems, we are simplifying systems by paring one set of hardware components with a software system that allows the end user to configure the component in multiple ways – going from many parts doing many things, to fewer parts performing even more functions.
As this happens, the topic of complexity has shifted to software. While electronics and embedded software are not simple, they do make variation and customization easier to accomplish than what would be possible using only hydraulic hardware. OEMs are looking for differentiation, the freedom to customize their products for multiple markets and customer needs – and with that flexibility comes the complexity of multiple software configurations.
The management of complex software, hardware and calibration variants is the next challenge. At Eaton, we ask the fundamental question: How many variants does the customer really need. This allows a renewed customer dialog surrounding how common systems and software strategies can be used across applications, and how modeling tools can be leveraged to correlate models for rapid optimization.
Where are overall vehicle electrification and hybridization efforts taking us as an industry? Where are the technology lags that still need to be developed in order to reach the end goal?
Long-term trends in energy costs are driving serious customer consideration and opportunities for hybrid designs on machines that have high kinetic loads to harvest. Eaton has been [at] the forefront in hybrid technology, with our hydraulic hybrid technology being recognized as offering the best [at delivering] power (storing and delivering energy very quickly).
Integrating these types of system solutions leads to another opportunity of coordinating power demands with the prime mover – the engine or electric motor. Significant energy saving opportunities are available, but require access and collaboration between engine and hydraulic manufacturers to get the most out of these total system solutions.
To further maximize benefit from total system solutions, we need greater intelligence around components and systems. Hydraulic components play a big role in many machine designs, but the need for smarter solutions is driving components to come together as intelligent electrohydraulic solutions. Electrohydraulics must move well beyond simple proportional controls. Advanced electrohydraulic controls allow hydraulic components to act seamlessly with the rest of the system, providing advanced control capabilities for the devices they are driving. This will require sophisticated sensing of elements both inside and outside the electrohydraulic component itself.
What technologies on the horizon will affect your existing and future product development?
The handshake between hydraulics and electronics is key. We are hearing this more and more from our customers in both the mobile and industrial space. When hydraulics only looks at hydraulics, and electrics only look at electrics, no one is looking at compatibility.
As a power management company with a broad range of both hydraulic and electrical components and expertise, Eaton is well positioned to address this need. Our variable speed drive system is a great example of integrating electrical and hydraulic components; in this case a variable pump and electronic drive combine to provide as much as 70% energy savings.
In the mobile equipment space, solutions like our Pro-FX technology help make machines more precise and efficient. Recently, working with Phoenix Curb Machines and distributor Spencer Fluid Power, the team utilized the Pro-FX technology to develop a custom controller solution, complete with a self-diagnostic function, which helps machine operators control every system function on the slipform curb machine and allows them to quickly pinpoint and troubleshoot problems as they arise (read more, 12114219).
Have you seen a shift toward smaller equipment? Is that effecting your product offerings?
There is certainly a shift to make all equipment more capable and more powerful while driving efficiency in the market – though the shift has not necessarily been to make equipment smaller. In some cases, this added capability and efficiency would allow customers to purchase a smaller piece of equipment – or use a smaller pump or engine – without sacrificing functional capacity.
Within Eaton’s Fluid Conveyance business, we also wouldn’t characterize any shift as a target desire to be smaller. Again, the overriding goal for those designing equipment and hydraulic systems is to develop a system that is more efficient, effective and safer than the current system. These overriding goals can sometimes result in smaller equipment – but not always.
On the components side, we are constantly challenged to reduce component size while maintaining or increasing flow and pressure capability. How much power density can we get into the smallest package? Smaller, more power dense products are expected for hydraulic components. Customers are looking for less material, a smaller footprint and lower pressure drops as part of the efficiency equation in component and system design.
What are the key customer requests that are most driving technology and vehicle development? How?
The key drivers in the hydraulics space are increased safety, increased reliability, increased power density and increased use of on-board intelligence which drive efficiency improvements. Our customers want a product that is safe to use, meets all regulatory mandates and is certified to do so. Regulatory mandates from governmental bodies are also driving many of the changes in equipment – for example, the European Union Machinery Directive and Tier IV and V emissions standards. Along with these increased regulatory requirements comes the growing requirement for smaller footprints and lighter packaging for both design and fuel efficiency.
Increased reliability, especially in developing economies, is also pushing designers to develop products that are both economically feasible and have a long working life. Finally, our customers are looking for on-board intelligence to optimize vehicle performance to help maximize functionality and minimize operating costs.
A broad driver of new technology development is the need for increased safety. The need is universal and applies to many, if not all, markets and customers – even though each market may have its own drivers and each customer may have a unique set of strategic initiatives. Eaton is responding to the opportunity to improve safety – we are heavily invested in LifeSense technology to help drive safer hydraulic systems. Within the off-highway markets, we have focused significant energy on increasing safety for CNG and traditional fuel systems.
MATERIALS
What material advancements are influencing your product lines?
We are seeing customers looking for significant improvement in coating technologies, particularly in applications with demanding environments like chemicals and sea water. Advances in these technologies, such as Eaton’s Dura-Kote plating technology, which is rated for up to 1,000 hours of corrosion resistance, are offering significantly improved life for components in these corrosive environments.
INFORMATION TECHNOLOGY
How is your company participating in the information technology movement?
Eaton’s first hydraulics product connected to the Internet of Things (IoT) is our LifeSense hose product – the only hose that self-diagnoses its health. IoT then utilizes the infrastructure of the Cloud to report on the hose’s status. Eaton has been offering IoT connected devices for many years – items from Uninterruptable Power Supplies that report their health to connected human-machine interface panels that can email the energy consumption of the machine being operated, or fluid condition monitoring to ensure the health of the overall system is intact.
Providing customers the means to collect data on their machines through the IoT, Eaton can help read the patterns and raise the signal before equipment fails – allowing companies to schedule downtime and maintenance, rather than face unplanned downtime.
Where is Big Data in your company’s equation?
Eaton is investing heavily in Big Data – and the ability to deliver not just data, but the information and knowledge that can be gained from applications. We see a broad range of ways in which this data will be used. Everything from machine health, operator behavior and energy efficiency at the individual machine level – all the way to informing the duty cycles we use to design our future products.
How important is automation to your future outlook and design considerations?
Automation is not just important for us, but for our customers too – it affects everyone, and Eaton is well positioned to take advantage of it. We are looking to design components with automation in mind, thinking about automation from a customer perspective. Before components can be automated, we need to understand how the machine is being used.
EDUCATION
What education programs do you offer or participate in to help cultivate the next generation of engineers?
Eaton offers a variety of educational programs – from leadership development to rotational engineering programs, mentorship, intern programs and outreach to universities. We are also working closely with the Center for Compact and Efficient Fluid Power (CCEFP) to support and attract engineering talent.
CHALLENGES & HURDLES
What new challenges have arisen that effect the way you design or manufacture your product? How you do business? How you go to market?
Greater intelligence and more complete system interactions require a level of design skills to properly apply these solutions in the marketplace. Engineers are constantly honing their skills in advanced controls and mechatronics, pushing innovation forward and helping our customers to utilize these advanced solutions to [get] the most out of their machine designs.
Speed of execution is another challenge we are facing. Development speed to meet customer requirements in our industry is increasing, and Eaton is at the forefront of developing innovative energy efficiency solutions to help meet those expectations.
Electrification is also a potential opportunity. We need to assure that we have products that focus on the strength of hydraulics, and continue to marry those with the strength of electronics. Helping customers to see the benefit of these combined technologies is a challenge we are continuing to train for.
Finally, talent will be key moving forward. Combining a slower growth environment and the ongoing retirement of the Baby Boomer generation means that our industry is challenged with a smaller and less experienced workforce. Eaton is working to attract top talent to help bolster the workforce and speed up the R&D execution to meet customer requests.