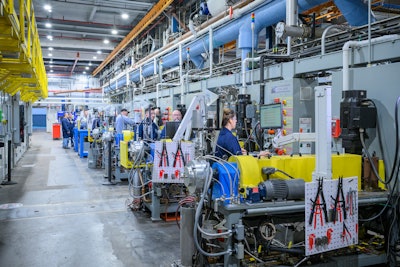
Several trends have begun to impact the off-highway equipment market in new ways over the past few years. For professionals in the field, it’s worth examining their impacts.
A good example can be found in the agriculture industry in the United States where several high-level shifts in the market have had numerous trickle-down effects on industrial farming equipment and the fluids that enable them. Broad demand for food production continues to grow with the global population. Crops feed the population. Greater consumer demand means the need for greater crop yield.
In the United States, industrial farms are meeting these demands in an interesting fashion. Across the country, farmland by square mile or acreage is decreasing. There are fewer farms by number and an increasing number of larger farms focused on optimizing yield with highly efficient acreage use. In fact, it’s estimated 42% of farmland is controlled by 2% of farms which make up the >5,000 acre category. Producing more with less is a major theme in the industry.
Because of this, major agriculture original equipment manufacturers (OEMs) have developed efficient, powerful new hardware to meet these needs. Larger engine sizes and torque requirements are now the norm to get more efficient work from a single tractor so they can harvest large areas in a short amount of time. This has major implications for the critical fluids that protect and enable the tractor’s transmission, hydraulic systems and final drive gears at the tractor’s axle.
Similar trends are impacting heavy-duty equipment in large scale construction and mining applications. Increasingly large equipment is performing more demanding work, necessitating higher and higher performance from hydraulic, transmission and final drive fluids. “More with less,” indeed, is becoming a trend not just in these industries, but everywhere off-highway equipment has a role to play.
Such equipment will require advanced, high-performance fluids to meet their full potential. It’s important to understand the importance of changing demands of such fluids, how next-level-performance is possible and why achieving such performance is so critical as industries continue to demand greater efficiencies in all applications.
Figure 1: There is a lot of research going into fluid and lubricant research for off-highway vehicles. Courtesy: The Lubrizol Corporation
Examining fluid performance requirements for today’s equipment
First, consider what’s at stake for fluid performance. The average market value of machinery and equipment per farm continues to rise (almost 3x in the last 20 years). These are major investments for end users, and they must be protected — all the more reason to leverage premium fluids in every application.
Modern industrial tractors provide an instructive example of modern performance demands. In this application, a single fluid is used to protect three critical drivetrain components, as noted: the transmission, the hydraulic system and the final drive. Such tractors commonly have one sump that supplies fluid to each of these important areas. The challenge here is each of these applications can have conflicting performance requirements.
For example, traditional gear oils that might otherwise be used in a final drive system have trended toward lower and lower friction performance to enable greater machine efficiency. As a result, less resistance between the moving parts enables heightened power economy.
Because the same fluid in a large tractor application is also used throughout the transmission, a very specific level of friction performance is required as designed by the OEM. Friction plates in the transmission and wet brakes in the final drive must be able to grab and hold together to provide functionality, and they must do so at high levels. This can become a complicated ask, especially as torque loads continue to increase in larger and more powerful machines.
Those high torque levels, as well as larger gears within the transmission, also necessitate higher levels of wear protection from the fluid—perhaps its most important job. Indeed, OEMs are specifying new heights in wear protection. We are starting to see higher levels of wear performance requirements from major driveline suppliers for large equipment. Balancing these requirements with adequate friction performance has proved a challenge for fluid formulators.
There also are the needs of the hydraulic system to consider, as well. Important performance characteristics, like a hydraulic fluid’s ability to maintain its designed viscosity throughout its service life, must also be balanced with friction performance and enhanced wear performance in such applications. Viscosity retention is important in low-speed, high-load applications where fluid flow is not robust enough on its own to create effective parts separation — if the fluid cannot deliver, wear performance can be further compromised.
Not all fluids found in the off-highway space must deliver this unique balance of performance. Construction and mining applications, for example, often see the use of dedicated fluids for hydraulic systems, transmissions and final drives, respectively. That said, many of the same demands still apply — machines are evolving to deliver more power and efficiency at higher torque levels, and fluid performance must continue to adapt. Meanwhile, there is end-user desire to utilize a single fluid in each of these applications as a means to eliminate complexity in their operations.
Figure 2: Fluids and lubricants affect many different aspects of an industrial tractor ranging from hydraulics to the brakes to the transmission. Courtesy: The Lubrizol Corporation
The necessity of next-generation additive chemistry
To meet the changing needs of today’s equipment, advanced additive chemistry must be deployed to deliver on increasing performance demands.
For instance, the heightened wear protection needs of modern driveline equipment that see higher torque loads have exposed some inadequacy in legacy chemistries. Zinc dialkyldithiophosphates (ZDDPs) have been one of the most reliable anti-wear additives in fluids and lubricants for many years, but they may have reached their limit in advancing off-highway driveline performance. Some ZDDPs used in off-highway additives (specifically aryl ZDDP) also have come under closer regulatory scrutiny—the European Union’s REACH regulation for chemical substances has enacted harsher labeling for products containing such chemistry. As industries continue to move toward more environmentally-friendly and sustainable operations, new alternatives have become a necessity.
It’s why advancing high-performance fluids with forward-looking additives to best enable off-highway equipment into the future is critical to satisfying modern demands. For example, through extensive testing and development, low-zinc anti-wear formulations have been designed to balance the range of performance needs of advanced off-highway equipment.
As critical equipment continues to evolve, it will be important that high-performance fluids are used across the board. OEM and industry specifications throughout the off-highway space will necessitate as much in the coming years as new needs are identified to best enable modern equipment to meet its full potential.
Fluids and lubricants are not just a component part of modern hardware operation — they must become technologically-advanced enablers in meeting the growing efficiency needs of the modern world.