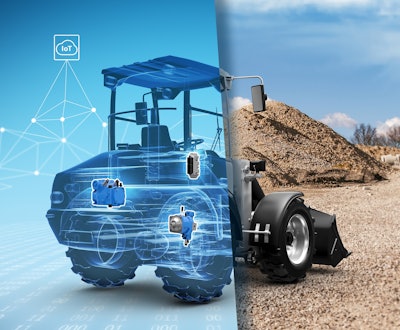
Selecting the optimal hydraulic pump is crucial for improving the performance of off-highway machinery, especially when considering energy savings and efficiency. Specific pumps that excel in delivering these two benefits have been shown to improve the overall functionality of these machines. Depending on the type of machine and an original equipment manufacturer's (OEMs) main objective, the choice of pump type plays a pivotal role in creating the necessary flow to ensure the appropriate pressure required for a system’s power output.
In addition to evaluating efficiency, estimating a machine's total cost of ownership (TCO) is crucial in identifying the return on investment (ROI) when implementing a new application such as a pump. This is a key consideration in which OEMs can ultimately save money while developing smoother, more efficient machinery. Furthermore, off-highway vehicle operations can also be improved through the implementation of interconnected, electronic control of hydraulic pump systems and mobile machines.
Variable piston pumps’ adjustable flow rate is desirable for off-highway machinery’s energy efficiency and total cost savings.Bosch Rexroth
Cost savings vs. efficiency
Gear and piston pumps remain the most widely used pumps in mobile machinery and considering the right pump system requires OEMs to determine the top priorities of a machine’s output. Pump systems and their flow illicit different results, with gear pumps promoting more cost savings and easy maintenance, and piston pumps resulting in higher efficiency and power density. Historically, many OEMs have chosen the former due to their reputation for total cost savings and perceived lower maintenance compared to piston pumps.
However, axial piston pumps are being utilized as a more efficient pump alternative in mid and large off-highway machines, specifically those with variable displacement. Variable pumps are ideal for machine efficiency as they generate the exact flow required for a system, using less fluid.
Gear pumps have fewer moving parts and a fixed displacement, which requires a constant flow of hydraulic fluid. Because of the fixed flow, many often consider gear pumps to be the most cost-efficient option. However, more energy savings and lower cost of operation are seen with variable pumps due to the adjustable flow rate.
Many off-highway machines have mobile hydraulic components like variable piston pumps working inside to help the overall system precisely control flow.Bosch Rexroth
The formidable power of variable pumps
A major differentiator between gear pumps and variable piston pumps is how efficiency is measured and optimized within hydraulic systems. The total efficiency of gear pumps is typically analyzed from a comprehensive, bird’s-eye-view of the entire hydraulic system rather than focusing solely on the component itself with its fixed flow characteristic. With variable piston pumps, the component makes the system efficient. The component is designed to do so by adapting to changing demands while being precisely controlled to generate the exact amount of flow required for the entire system. This adaptability results in significant energy savings with minimal energy waste, particularly in machinery with fluctuating loads.
Regarding power density, variable piston pumps have a significant advantage in maintaining high-pressure levels, typically up to 6,000 PSI, which enables the actuation of high-power consumers without increasing the flow. Without wasting energy, machines equipped with variable pumps can maintain full power potential and run continuously for extended periods, maximizing productivity, operational efficiency and machine lifespan. Additionally, the precise fuel consumption control offered by variable pumps is a crucial practice in determining not only the output of the machine but also the ROI.
Electronics’ impact on energy efficiency and cost saving
The main benefit of electronics is the possibility to change pump control method dynamically via a controller area network (CAN) protocol message. When you have a mechanical controller in the piston pump, you should select one control mode, either flow control, pressure control, or power control. From there, all machine movements need to be performed with this type of control, forming a more complex control strategy in the control block.
With this electronic control in the variable pump, you can perform the same control strategy with software, thus enabling the possibility to change the control strategy accordingly to the specific movement needs at that given time.
Gear pumps can offer up-front cost savings some attribute to its fixed displacement.Bosch Rexroth
Cost-benefit analysis
In the final analysis of selecting a hydraulic pump for an off-highway vehicle, the choice often comes down to a comprehensive TCO analysis of a machine equipped with each type of pump. This analysis ultimately considers the up-front cost savings of a gear pump and the long-term, total efficiency of a piston pump.
In making a case for variable piston pumps, it’s important to note the cost savings may not be immediately apparent. Instead, the benefits will accrue over time, resulting in a smoother, more energy-efficient machine that will provide superior results in the long run.