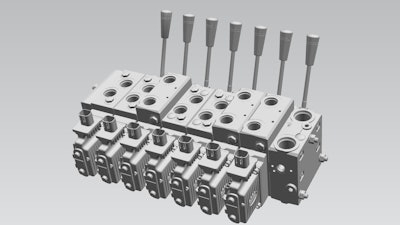
Mobile hydraulic valve systems have evolved in several ways due to ever-increasing work function control requirements driven by mobile equipment manufacturers. Whether controlling a backhoe outrigger stabilizer or a truck crane hoist function, balancing cost, performance, efficiency, space-claim and reliability are paramount in optimizing work function performance.
Work function valve manufacturers have overcome many of these barriers through widely proven and now sought-after load-sensing technology. Known mainly as a method of calling for flow on demand, load sense technology has been used in many ways to enhance flow and pressure control. For instance, the pre-compensator that controls flow similar to a restrictive flow regulator valve can be converted to a variable flow shut off valve by varying or removing the amount of load-sense pressure seen in the pre-compensator spring chamber. This, in effect, can operate as a variable horsepower limiter feature integrated within the pre-compensated valve work section.
The greatest challenge inherent to the pre-compensated load sensing valve is maintaining flow regulation when there is little or no load, or negative load pressure for the load-sense pump and pre-compensator to correctly operate as a flow regulator. The only method to overcome a negative load condition is to create an artificial positive load pressure. This is commonly achieved using externally mounted counterbalance valves attached to the work function motor or cylinder. Counterbalance valves are typically required to ensure that the actuator does not creep from possible spool valve leakage and serves as a safety device in the event of a hydraulic hose breaking between the work function control valve and work function actuator. Counterbalance valves also serve as motion control devices that require a pilot command from the work function valve to open, which provides the desired pre-compensator positive load pressure.
Counterbalance valves are typically only found on larger machines where functions may or may not require safety. Negative load conditions become a challenge on smaller, lower horsepower machines designed for cost-sensitive markets that do not require safety but require flow regulating stability. There are other more inefficient and costly methods of creating artificial load pressure to ensure pre-compensated flow control stability. These all require special work function valve parts and an additional valve that, in most cases, requires fine-tuning on the equipment manufacturer’s machine, slowing down the development cycle.
The PVBM contains two additional compensators integrated into the module design that act similar to counterbalance valves.Danfoss Power Solutions
The innovative approach to pre-compensated work function flow control
Danfoss has 40 years’ experience of continuously developing modular, pre-compensated valves for the global mobile hydraulic industry. The company’s mid-flow range PVG32 pre-compensated valve has broken new ground, providing increased pre-compensated flow control stability. The PVBM is a pre-compensated work function module capable of ensuring a constant positive load pressure condition regardless of work function operating conditions. It can be added to any PVG32 work function control valve. The PVBM contains two additional compensators integrated into the module design that act similar to counterbalance valves, though work in natural harmony with the main pre-compensator.
These two extra compensators allow for regulated return flow on each work port and ensure that positive load pressures are always seen at the main pre-compensator. Intended initially for medium- to low-horsepower propel applications and other non-differential work function actuators, PVBM fundamentals are designed around a meter-in/meter-out principle. When using the PVBM to control propel function in an aerial lift application or similar open circuit propel system, the unique module design will allow for smooth control of the propel system during uphill (positive load) and downhill driving (negative load).
One pump provides all machine functions
Mobile equipment manufacturers of small- to mid-size machines are always looking for ways to reduce costs and gain space claim by reducing the number of pumps. Most mobile equipment that requires both work function flow control and propel flow control systems creates a space claim concern for the smaller machine development. When integrating the PVBM into the open circuit work function valve, the only pump required for both propel and work functions is the single open circuit pump.
PVBM advantages over closed-circuit pump propel systems
- Shorter installation time
- Fewer required components
- Easy configuring and tuning
- Natural braking with no engine overspeed
- Improved energy efficiency
PVBM advantages when replacing work functions
- Shorter install time
- Fewer special components and connections required
- Improved stability
- Increased productivity
- Increased efficiency
- Improved controllability
PVBM applications
- Mini to mid-size HP propel circuits
- Slewing work function circuits
- Winch work function circuits
- Gravity-down work function circuits
PVBM features
- Linear or progressive control flow from 5 lpm (2.3 gpm) up to 100 lpm (26.4 gpm)
- Work port relief valves including integrated anti-cavitation valves
- Work port load pressures to 350 bar (5,076 psi)
- Manual, hydraulic or electro proportional control, including CANbus
Danfoss Power Solutions