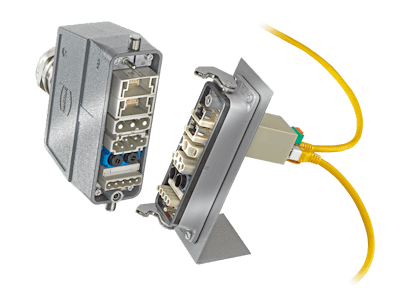
Connectors play an important role in heavy-duty vehicles and equipment as a means of joining electrical components and transmitting data and power. As the amount of electronics being incorporated increases, so will the need for connectors with higher performance and new functionalities.
In a recent report from MarketsandMarkets, it’s stated the heavy-duty connector market will achieve a CAGR (compound annual growth rate) of 4.6% between 2018 and 2023, reaching a value of $3.51 billion. This is attributed to the rise in the adoption of industrial automation solutions, says the report, as heavy-duty connectors are necessary for enhanced signal and power transmission, and for increased robustness in harsh environments.
The “Connector Market Report” from Research and Markets puts the global connector market at a CAGR of 4.9% from 2018-2023, reaching a value of $80.4 billion. This report says the market is seeing increased demand for high speed connectors, a shift toward compact and thinner connectors, and development of high power connectors.
“The trends for connector design are following the trends in vehicle architecture,” says Joseph Bolewitz, CTO Industrial & Commercial Transportation (ICT), TE Connectivity. “More electronification within vehicles is driving the need for higher pin count connection systems.”
In addition, he says inclusion of advanced driver assistance systems (ADAS) and their associated components—cameras, antennas, radar, etc.—require the use of high speed data connectivity solutions which are designed and manufactured for harsh environments.
Creating more robust solutions
“Our end customers are seeking higher levels of robustness for harsh environment applications,” says Bolewitz. Because of this, TE Connectivity has developed technologies such as its TE LITEFORCE for use with high pin-count connectors. It features a wave structure contact geometry on the terminal beams, helping to achieve improved vibration resistance and current carrying capacity.
TE LITEFORCE features a wave structure contact geometry on the terminal beams, helping to achieve improved vibration resistance and current carrying capacity.TE Connectivity
“This revolutionary terminal design can reduce the terminal mating force which is a challenge associated with high pin count connection systems arising from higher electronic content within vehicles,” he explains.
There has been a focus in the industry toward using molded connectors versus field wireables in order to reduce environmental resulted downtime. Exposure to moisture, humidity, UV, fluctuating temperature (both cold and hot) and vibration accelerate the aging process of seals and gaskets commonly found in field wireables, says April Ankrum, Senior Product Manager for Connectivity at Turck Inc. Overmolded solutions fully encapsulate critical wiring points which result in long-lasting protected solutions.
According to Ankrum, customers are looking to make their entire assemblies—cable, connectors and wires—as robust and long-lasting as possible. “For years the focus was only on specifying IP rated connectors, but recently we’ve seen a jump in the demand for advanced cable jacketing materials such as our Extremelife-60 cable with superior outdoor performance in installations with oil, grease, gasoline and UV exposure. Complex vehicle harnesses can contain many meters of cable and wire,” she says. “Customers are seeing the benefit of investing in superior, longer lasting solutions which ultimately helps their bottom line.”
The desire for more robust solutions is also a growing trend for the connector harnesses. Todd Baumgartner, Business Development Manager for Harness and Cable Assemblies at Turck Inc., says solutions similar to a molded backshell of a connector help to ensure longevity of the harness in rough operating environments. “What we’re doing is incorporating Turck molded cordset solutions into harnesses, and converting traditional wire harnesses into cable harnesses, and customers are really open to [these] harness solutions,” he says. “They really like that alternative approach because it is more robust and provides added protection to the connections.”
Space savings and technology integration
Miniaturization and space savings are necessities for many industries, says Nirav Patel, Senior Product Manager, HARTING Inc. This has become especially important as manufacturers look to integrate more electronics, and thus more connectors and associated wiring. Because of this need to integrate more components without taking up valuable real estate, HARTING developed its Han-Modular® portfolio which Patel says allows engineers to “build up an industrial connector that is customized to their exact requirements using off-the-shelf components.”
Han-Modular® enables different signal and multimedia types—such as power, signal and data—to be combined into a single connector unit. Standardization of the module sizes provides flexibility as modules can easily be changed without affecting the footprint of the connector. Engineers pick each of the modules they want to use, with over 100 modules available. “The Han-Modular® series allows for [the] utmost customizability with standard part numbers,” says Patel.
“This keeps the customer’s choice as flexible as possible,” he continues. “For example, some machinery customers require power, signal, and pneumatic connections. With Han-Modular®, that is possible with a single connector.”
Bolewitz agrees that smaller connector designs are important to providing customers with more design flexibility, as well as space savings. He notes a connector often dictates the package size of a module as it can be the largest component mounted onto a PCBA (printed circuit board assembly). “By having a smaller connector, the PCB space required for the header is minimized, allowing additional components/functionality to be added to the same size PCB or a reduced size PCBA to be used,” he says.
With electrical content of vehicles continuously increasing, he says the use of smaller terminal systems enables a much denser packaging of electrical circuits within the same area. To help with this TE Connectivity looks at using mat seal designs in a connector to provide tighter centerline spacing of terminals versus use of individual wire seals. “This allows OEMs to pass more circuits through the same size space to address the higher amount of electronic content on a vehicle,” says Bolewitz.
In addition, he says TE Connectivity aims to design products which use as few components as possible in order to achieve their necessary function. “We also look for opportunities to integrate multiple functions into a product, such as integration of sensors or electronics. Integration of functions can offer a more compact solution as it offers a smaller package size as compared to packaging individual components/sensors into an application.”
Integration of electronics into a connector module can provide multiplexing capabilities to simplify system architecture by enabling a distributed architecture to be created with a significantly reduced number of wires or connections. Bolewitz says integration also simplifies the supply chain as a single part is provided instead of having to procure and assemble multiple components. Engineers pick each of the modules they want to use for their Han-Modular system, enabling them to customize it to their exact requirements.HARTING Inc.
HARTING has also built intelligence into the smart Han® modules which are part of its Han-Modular series. “Industry 4.0 allows more and faster communication from the process level up to the ERP level, resulting in increased industrial efficiency,” says Patel. “This is especially true in the process level, where connectors are installed. Smart products in Han-Modular® moves intelligence from the panel to inside the connector.”
The technologies and features of smart Han® vary by module. Patel says initially the company focused on them providing intelligence in machine identification, fast Ethernet switching and surge protection. Expansions to the functionalities will include current and voltage measurement, and signal conversion.
Baumgartner says Turck has seen with some customers the desire for components, such as resistors or capacitors, to be incorporated into the circuits of cordsets and harnesses it develops, as well as incorporating devices into the harnesses and cordsets in order to create more integrated and intelligent products.
He also notes the company will often incorporate other companies’ connectors into harnesses to give customers an integrated solution. As the connectors have gotten smaller, he says the equipment necessary to work with them has become more elaborate and technical. Because of this the company works with employees to train them on use of this more advanced equipment, ensuring the company keeps up with the ever-evolving industry.
To aid troubleshooting, Ankrum says there is a movement towards incorporating more visual indication. Cordsets or wiring harnesses are often tucked away and hidden from view within a machine design for protection, making them difficult to find if an issue occurs. With a visual indicator such as a red light, a customer can look inside the machine and see immediately where the problem is without having to use a flashlight and try to determine exactly which wire it is that needs fixing.
Turck recently introduced such a product, an LED Deutsch connector, which Ankrum says has been well received in the marketplace. The company has gotten requests for other varieties of the product due to the strong push for visual indication, she says.
While LED technology is not a form of active intelligence, “I think of it as smart system design because it allows you to diagnose problems quickly,” says Ankrum, which is beneficial to reducing the amount of time it takes to troubleshoot and ultimately limit unplanned downtime. Turck's LED Deutsch connector includes a visual indicator to help ease troubleshooting, particularly when the device is tucked away or hidden from view in a piece of equipment.Turck Inc.
As far as embedding intelligence into a connector, she does not foresee the industry moving in this direction. “The connector is a singular passive device, part of a larger control or wiring system. Multiple connection points through control boxes, custom enclosures or wiring harnesses provide easy access and customization for signal, data and power transmission. Moving active intelligence into a singular connector isolates data into a singular run and you lose the benefit of consolidation. In the end, it’s a balance between the complexity of the wiring system and the cost.”
As manufacturers look toward doing more system simplification, Ankrum notes it’s important to not get tunnel vision about doing so without considering the risks. Depending on the system and application, it can actually be cost prohibitive to over consolidate.
She says Turck worked with a customer which had consolidated its wiring to a single large, complex wiring harness within a vehicle design. However, the customer found that when damage occurred to the harness it was cost prohibitive to repair it because of its complexity. Instead of being able to go in and do a quick fix or section replacement, the whole harness had to be scrapped and replaced. “They were asking for our help in breaking the harness back out into manageable pieces so that when damage occurred it would be not so detrimental,” she says.
By working with the customer, Turck was able to recommend a three-piece wiring solution which made servicing easier.
The desire for more electronics, intelligence and simpler systems will likely progress further as vehicle and equipment designs continue to evolve in the coming years, and especially as automation and electrification increases. As such, connector manufacturers will also continue advancing their product designs to meet the needs for higher levels of data transmission and faster communication, and working with customers to find solutions which best meet all aspects of their application requirements.