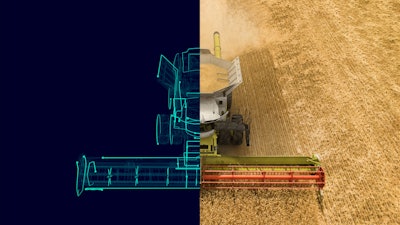
The demand for heavy equipment and off-highway (HE/OH) vehicles is growing. Heavy-duty machinery like agricultural tractors, excavators and haul trucks are critical for many industries and the sourcing of the raw materials needed to manufacture a variety of consumer and commercial tech products. The need for these vehicles is increasing as global urban populations rise and industrial customers and consumers demand greater capabilities in various products.
Meanwhile, new regulations and sustainability mandates require companies in all industries become more efficient, accomplishing greater productivity while using less energy and resources. Heavy equipment and off-highway original equipment manufacturers (OEMs) must innovate, delivering vehicles and equipment that are smarter, more connected and more efficient. Traditionally hydromechanical systems are being replaced with advanced software and electronics that can support core functions while also providing a platform for more advanced features and functionality now and in the future.
The next generation of heavy equipment and off-highway vehicles will be the most complex ever. Traditional approaches to vehicle development, manufacturing, and service will not scale to meet the demands of these vehicles, driving heavy equipment and off-highway OEMs to seek new methods that align with the growing need for innovation, agility and speed.
Business, tech trends for HE/OH manufacturers
There are a few challenges for HE/OH manufacturers as they navigate this industry. In addition to the transition toward software-defined products, HE/OH products must become more efficient and sustainable to meet various regulations and environmental targets. And while the need for innovation is high, manufacturers must be careful to keep pace without overspending on programs that will not deliver near-term value.
HE/OH manufacturers also are investing in electrification and autonomous driving and robotics to achieve a future of smart, efficient and high-value products. From a business perspective, these same innovative capabilities can provide opportunities to create new value-based business models that generate more stable high-margin revenue.
Figure 1: Digital transformation is critical to meeting the growing demands on the heavy equipment and off-highway industry for advanced vehicles that support efficient production of food, raw materials, and more. Courtesy: Siemens
Electrification, alternative fuels drive gains in efficiency
Heavy equipment and off-highway industries are exploring electrification as a means of improving equipment efficiency and industry sustainability. Electrified powertrains, whether they’re full battery electric or hybrid diesel-electric, have shown potential in several applications common to the HE/OH industries.
Battery electric vehicles (EVs) are already being deployed in high-load and low-range applications and in smaller vehicles like skid steers and small excavators. These applications are well-suited to the high torque and precision of electric motors. They also enjoy additional benefits of reduced noise, vibration and emissions producing a healthier and more pleasant job site. Long-term cost of operation and ownership of these vehicles is often lower than their diesel counterparts.
Electric power delivery has also increased in viability thanks to improvements in the practices of HE/OH customers. In the agricultural sector, many farmers are reducing or eliminating soil tilling as a part of their growing practices, opting instead for direct seed drilling or minimal tillage approaches. By minimizing or eliminating the ploughing process, the average power required to sow a field is reduced. This reduction in average power demand means that battery-powered vehicles can operate longer on a single charge, ensuring the farmer can keep up with tight planting and harvesting schedules.
Many HE/OH OEMs also are developing equipment that can be powered by hydrogen and other alternative fuel types. These fuels can reduce combustion emissions and the overall carbon footprint of vehicles without imposing long refueling times. These alternative energy sources also offer different range and load characteristics, making them well-suited to different applications to battery EVs.
Some challenges prevent battery electric and alternative fuels from being a scalable solution in the near-term for all segments and applications. Charging time is the most salient drawback, particularly for remote job sites where high-quality, fast-charging connections are likely not available. Electrification also tends to increase the upfront cost of machinery. At the same time, reliable supply of alternative fuels remains a hurdle because fueling infrastructure and supply chains for alternative fuels is nascent.
Figure 2: Autonomous machines must navigate work sites and operate robotic components without human intervention but can deliver significant gains in productivity. Courtesy: Siemens AG
Automation’s future role in self-driving and autonomous robotics
In the longer term, heavy equipment and off-highway OEMs are focusing on the development of autonomous driving and robotics for farming, construction, mining and other heavy-duty applications. The development of an autonomous machine that can independently navigate and manipulate its environment is complex, requiring integrated systems of sensors, on board and cloud computing and precise actuation.
These machines face other unique challenges. Due to the low production volumes common to the industry, the cost of custom sensors and computer chips is more difficult to recoup. As a result, HE/OH OEMs often relies on off-the-shelf sensor and compute components to enable autonomous functionality, which places additional constraints on engineering and design.
Autonomous machines also may require greater object recognition abilities to that of a self-driving car. An autonomous sprayer, for example, would need to be able to distinguish between crops, harmful weeds and other non-crop plants that may be beneficial.
These OEMs, however, have the advantage of working in relatively controlled environments, at least compared to dense urban environments or highways full of other drivers. An autonomous tractor or haul truck, for example, will only ever operate within a limited area, such as a crop field or quarry, which makes routing and navigation simpler. Even when moving to a new field or job site, these relatively small areas can be digitally mapped in detail, providing the autonomous system with accurate topological information to guide routing and navigation. With controlled, predictable routes, human operators’ safety is easier to ensure.
Electrification, automation and the underlying shift toward software-defined vehicles and machinery also are being pursued in response to customer and regulatory demands, and to capitalize on new business opportunities. Incorporating and scaling these technologies depends on the ability of companies to manage cost, overcome complexity in development and produce reliable and robust systems.
Digitalization as foundation for the future
Digital transformation of the entire lifecycle from design and engineering through to in-field service and maintenance can help OEMs design, produce and service the connected, smart, and reliable HE/OH vehicles and equipment their customers need.
Through the digital twin, HE/OH vehicle manufacturers can drive engineering activities that span multiple disciplines, domains or even lifecycle stages. Such an approach incorporates software, electrical, electronic and network domains into a holistic system-level development program. Requirements for the vehicle’s mechanical, electrical, electronic, network and software systems can be defined and integrated at the earliest stages of development, ensuring domains are synced from the beginning.
As development progresses, the digital twin ensures engineering data stays in-sync and is available where and when it is needed, preventing miscommunications and guaranteeing decisions are made based on the latest information.
Advanced simulation tools also facilitate continuous verification and validation, promoting the optimal balance of multiple aspects of vehicle performance. When applied in automated scenarios, simulation can be used for design exploration, algorithmic decision-making, or to virtually execute a massive number of duty cycles for the certification of autonomous systems.
Digitalization can also extend into the manufacturing and service lifecycle for HE/OH vehicles, helping develop smart and flexible production systems and master mixed-model production in a complex global manufacturing ecosystem. HE/OH vehicles are either highly customized or even unique; often about 20 percent of the final configuration of a vehicle is specific to the customer. The digital twin helps companies create flexible and adaptable production systems that accommodate these unique configurations while maintaining high throughput.
The comprehensive digital twin also supports a closed loop between design, manufacturing and the product in use where data from throughout the lifecycle can be captured and turned into value for the OEM and their customers. Manufacturing data, such as quality reports or scrap rates, and real-world product performance data can be leveraged to improve product designs and production systems. Critically, real-world data can also be used to provide high-quality customer service and technical support as OEMs transition from machine vendors into solution partners.
By capturing live operational data, OEMs can provide customers with targeted and efficient diagnosis and repair services and even help prevent unscheduled downtime by anticipating issues and recommending interventions before they take a machine out of service. These capabilities will only become more important in a future of automated vehicles and machinery, as robust operational data can be analyzed with industrial artificial intelligence (AI) to guide the development of new software features and improve machine performance.
Figure 3: Digitalization and the digital twin ensures that product development starts integrated and stays integrated, and it connects product design to manufacturing and service lifecycles. Courtesy: Siemens
Digitally constructing the products of the future
Innovation in the HE/OH industry is being pursued to develop capabilities that will support construction, farming, mining and material handling sectors in a future in which efficiency, sustainability and productivity must be addressed simultaneously. As pressures mount, these companies are looking to transform for the future and enabling innovative designs in an industry characterized by low volumes, small margins and demanding applications.
The comprehensive digital twin will act as the foundation for the collaborative, integrated approach demanded by modern vehicles, bringing the mechanical, electrical, electronic and software domains together to design a complete system. In addition to improving data sharing between all stakeholders, the comprehensive digital twin facilitates the translation of that data into actionable insights that can help reduce cycle times, increase efficiency and improve market agility. The result is a distinct competitive advantage in meeting growing customer demands for greater performance and smarter features while also helping to overcome the challenges of growing complexity, shifting workforces and the need for sustainable designs for HE/OH vehicles.