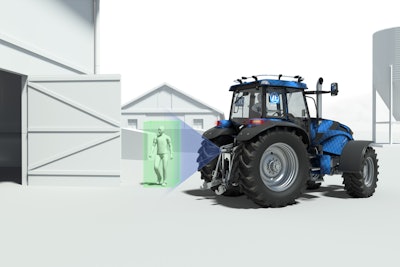
According to Dr. Stefan Sommer, CEO of ZF Friedrichshafen AG, automated driving, safety and efficiency are the megatrends of the future. As such, the company is focusing much of its efforts into developing intelligent systems which meet the requirements of these trends. ZF’s goal is to be a one-stop shop for these technologies by working together with other suppliers in the industry to provide complete system solutions such as the recently introduced Evasive Maneuver Assist (EMA) technology.
EMA was jointly developed by ZF and WABCO Holdings Inc. The system safely steers a truck around an obstructing vehicle or object in the roadway and brings it to a complete and safe stop to help drivers avoid a collision.
The system utilizes the control logic of WABCO’s OnGuardACTIVE radar-only collision mitigation system to identify when EMA should be activated by sending a sudden “pulling” sensation to the steering system as well as an audio and visual warning to the driver. EMA calculates the evasive maneuver that should be taken and steers the truck accordingly. While all of this is automated, the driver can override the system if necessary and take over control of the steering wheel, brakes or throttle.
Watch a video of the EMA system in action.
In addition to OnGuardACTIVE, EMA makes use of WABCO’s electronic braking system (EBS), advanced emergency braking system (AEBS) and electronic stability control (ESC) and vehicle dynamics control systems. All of these are connected to the ZF elecrohydraulic ReAX power steering system.
Bringing automotive features to commercial vehicles
The EMA system is one of the many new technologies included on the ZF Innovation Truck 2016, designed to demonstrate current and future technologies available from the company.
Included on the truck is Highway Driving Assist (HDA), a system designed to actively keep the vehicle in lane and at an appropriate distance from the vehicle in front through the use of various sensors. Mounted on the front windshield of the truck is a camera sensor which monitors road markings while a radar sensor measures distance. The radar sensor is able to provide a broad field of view at low speeds and long range detection at higher travel speeds. ZF specially designed into the HDA control unit a feature for virtually calculating where markings on the side of the road should be if they are missing. The company says the HDA system should be ready for volume production within the next couple of years, and will meet the needs for truck platooning.
Learn more about the concept of truck platooning in the article “Follow the Leader.”
HDA is one of the company’s many technologies initially developed for use in passenger cars, but now being transferred to commercial vehicles as part of the company’s efforts to further develop and demonstrate its capabilities to meet the needs of the megatrends of the future.
The Innovation Truck also features the ability to remotely maneuver the truck for docking operations. Once at the appropriate destination, drivers can exit the cab and control the truck’s steering via a mobile app which communicates wirelessly with the truck. The driver simply has to press a finger onto an image of the truck within the app and drag the trailer left or right to make the truck move in the desired direction. Being able to step outside the vehicle improves the driver’s visibility and accuracy when parking the truck.
Read more about this technology and the first iteration of the ZF Innovation Truck in the article “Autonomous operation goes mobile.”
Watch ZF demonstrate the remote maneuvering capability for docking operations.
Innovations for the off-road market
ZF’s new Innovation Tractor demonstrates the ability to bring driver assist technologies to off-highway applications, as well.
Similar to the Innovation Truck, the tractor’s Hitch Detection feature enables operators to remotely maneuver the vehicle using a mobile app. Once an operator has the tractor within range of the trailer or other implement with which it will be hitched, he or she can step out of the cab and use the mobile app to remotely drive the tractor towards the trailer until it reaches the optimum position for hitching the two pieces of equipment together. While physically hitching the two pieces of equipment together is still done by hand, ZF says it could be possible in the future that the company will work together with implement OEMs to automate the hitch connection process, as well.
Hitch Detection uses two cameras—one at the top of the cab and one positioned at the lower end of the tractor—to detect target shields placed on the implement to which the tractor will be hitched. The cameras continuously monitor the position and angle of the trailer in relation to the tractor to ensure it moves in the correct direction. The system currently operates at a distance up to 10 m (32.81 ft.).
As ZF continues to develop the system, the target shields will no longer be necessary. The company says in the future it will use optical cameras and a laser system which is more accurate for determining distance and changes to the environment.
To move the tractor, operators push a button on a mobile app which displays a 360 degree birds-eye view of the tractor and trailer. No steering is required; the operator simply presses down on the app’s ‘Start’ button and the tractor moves autonomously in the direction of the implement. The moment his or her finger is lifted off of the button, the tractor stops moving. Once the Hitch Detection system senses the tractor is in the appropriate position for hitching, the tractor stops automatically. With this system, operators can improve their visibility during hitching operations which leads to a safer working environment.
ZF says this system is also the first step towards developing fully autonomous capabilities. Though development of autonomous vehicle technologies is nothing new, and already in use in various off-highway applications, changing weather conditions and more limited windows for getting into fields is further driving the move toward autonomy in the agricultural industry.
In addition to the cameras used for the Hitch Detection system, the Innovation Tractor includes six more cameras designed to provide a 360-degree view of the vehicle and its surroundings. This surround view system features two cameras placed at the front of the tractor and four at the top. ZF says could work with just four cameras, as well, but to ensure optimal safety it has chosen to use six.
The tractor also includes two more cameras for its Pedestrian Detection feature, a technology ZF has brought from the automotive industry. Pedestrian Detection automatically stops the tractor if a person is detected behind it. The system currently has a 7 m (22.97 ft.) range and 180-degree angle of visibility.
All of the of the cameras included on the Innovation Tractor, and their associated hardware and software algorithms, were developed by ZF to provide OEMs with a complete system solution. ZF says the cameras are capable of sensing details in any light conditions—whether it’s bright and sunny or there are shadows—and that their visibility is better than that of the human eye. While there are currently several cameras on the tractor for the various systems, the goal is to use the same cameras for the Hitch and Pedestrian Detection systems and integrate them with the 360-degree surround view system.
Another feature of the Innovation Tractor is the Traction Management system which enables the tractor and attached implement to more easily maneuver through muddy conditions and on slopes with up to a 30% gradient. In the tractor is a 50 kW (67.05 hp) generator connected to its power electronics. As the tractor attempts to move on a slope or through muddy terrain, an electric current is transferred to the rear wheels of the trailer by the generator and power electronics system to power and control the rear wheels and axle to optimize traction between the tractor and the trailer. The idea is to create traction where there is weight to better transfer it to the ground. When Traction Management is engaged, steering is automated and controlled by the tractor’s on-board computer system.
Watch the Innovation Tractor climb a 30% slope using the Traction Management System.
See up close the various components and systems used for the Traction Management system.
Through the Innovation Tractor, as with the Innovation Truck, ZF is looking to identify new product ideas and develop the means of transitioning technologies from other applications to the commercial vehicle segment. Doing so not only provides the potential for improving operation and safety of heavy-duty vehicles but also the possibility for bringing them to market faster. Autonomous operation, for example, will most likely be more widespread in the off-highway segment first because these vehicles are not operating on public roads and therefore not as heavily regulated.
With its innovation vehicles ZF is focusing development on technologies which are feasible today so customer can take advantage of the benefits these new technologies provide—such as improved efficiency, safety and productivity—as soon as they’re available.