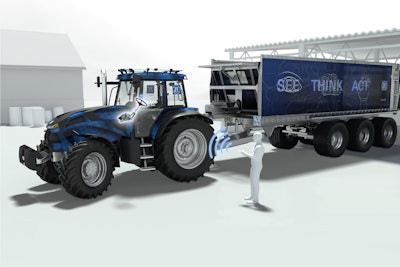
ZF Friedrichshafen AG has designed an Innovation Tractor to demonstrate how safety, comfort and efficiency can be enhanced by applying intelligent systems from the passenger car and commercial vehicle segments to off-highway vehicles. The Innovation Tractor is equipped with environmental cameras in order to monitor its surroundings; the data from these cameras is then utilized to enable the vehicle to maneuver semi-autonomously or via mobile devices operated outside the driver's cab, making it easier to hitch implements. Cameras with pedestrian detection capabilities help to further enhance the safety of such operations. Drivetrain electrification in the Innovation Tractor comes courtesy of the powerful ZF TERRA+ generator module, an electric single-wheel drive for trailers and implements. Coupled with specially developed traction management, it provides optimum off-road maneuverability.
ZF is one of the few companies to introduce autonomous driver assist systems (DAS) across all vehicle segments. ZF's expertise in networking sensors, intelligent electronics and mechatronic systems is key to giving vehicles the ability to see, think and act. This enables end customers in the construction, agricultural and other off-highway segments to use entirely new automation approaches.
The Innovation Tractor is a standard tractor, upgraded with groundbreaking ZF components and assistance functions. “Our systems expertise enables us to combine established stand-alone systems to create a network so we can make vehicles see, think and act,” says Dr. Harald Naunheimer, Head of R&D at ZF Friedrichshafen AG.
Eyes and brain
Six cameras mounted on the driver's cab and the hood act as the vehicle's “senses.” A computer analyzes the images from the camera and generates a surround-view image of the tractor's spatial environment. The driver can view this image on a tablet from various perspectives, including a bird's-eye view. The driver can also see an overview of the tractor's movements.
Additional cameras are available at the rear of the tractor with a separate data processing unit and are used during automatic hitching and for pedestrian detection while changing implements. ZF provides customers in the off-road segment with unprecedented levels of safety and comfort. These systems can considerably reduce the risk of accidents - particularly in narrow depots.
Mechatronic systems in the chassis and driveline
An electric steering system, required for automatic driving functions, has been built into the control network and the driveline includes ZF's TERRAMATIC transmission and TERRA+ generator module. This system generation can provide 60 kW of continuous electrical power and serves as the power source for the electrical consumers in the trailer. The trailer features another key innovation - an electrical wheel head with a three-phase asynchronous motor developed by ZF specifically for use in agricultural and construction machinery.
Additional electrical power
The all-wheel-drive function of the ZF tractor and the electrical boost function from the single-wheel drive on the trailer interact and complement each other delivering optimum Traction Management. The tractor/trailer combination can negotiate muddy or loose ground, and with electrical assistance from the trailer, the tractor successfully tackles uphill gradients of up to 30%, terrain normally off-limits for a conventional tractor/trailer set-up. The additional power from the trailer allows a higher payload to be transported with a downsized tractor, ideal for users who tow a fully laden trailer only occasionally.
Two liquid-cooled, high-power, three-phase asynchronous motors with a downstream transmission stage drive the trailer axle. The electric motors are integrated into the wheel heads, saving space. The nominal voltage is 400V, and the system can also be fitted with a wheel brake. Forces can be transferred to the field more carefully with the tailor-made drive concept, and trailers of the future could even be able to move autonomously.
Automated driving functions negate manual operations
The SafeRange function allows the driver to leave the vehicle and remotely control the tractor/trailer combination from a safe distance. The Innovation Tractor and trailer are outlined as a bird's-eye view on a tablet display and all the relevant driving and steering commands are managed from here. The vehicle components can be moved intuitively on the screen. Dragging the tractor or trailer to the right or left on the screen with a finger causes the actual tractor/trailer combination to maneuver in the chosen direction. When it comes to complicated reversing, the user simply needs to specify the direction in which to steer the trailer and the system calculates and executes all the necessary steering movements. The speed is set by swiping the screen from the center to the edge, across the tractor model or the trailer. The further toward the edge, the faster the tractor/trailer combination moves. The maximum forward speed is 4 km/h, with the top reversing speed limited to 2 km/h. When contact with the screen is removed, the vehicle stops automatically. The same happens if radio contact is lost between the tablet and the Innovation Tractor. SafeRange also works when maneuvering the tractor without a trailer.
Maneuvering using the tablet may become more taxing when hitching implements; however, ZF engineers have addressed this issue by introducing the Hitch Detection function to automate the process. The system uses a camera to detect the exact position and angle of the relevant agricultural implement in relation to the tractor by using special targets installed on the trailer or implement. The position is continuously measured during the hitching process and the angle of the steered wheels corrected. The Innovation Tractor maneuvers automatically until it reaches the optimum position for hitching, which is then done by hand.
The Pedestrian Detection function helps ensure the Innovation Tractor works as safely as possible while using the tablet for maneuvering and hitching. The cameras detect pedestrians located between the vehicle and trailer and this information, along with the individual's location, is displayed on the tablet. If the person controlling the tractor fails to respond, the system stops the vehicle. The interrupted hitching process can only be restarted once there is no one between the tractor and trailer.
“True to the ZF innovation concept, the Innovation Tractor brings together in a test prototype all the new functions we believe are practical for agricultural and construction applications,” says Naunheimer. “The focus was on demonstrating what is already possible and technically feasible today, but sets a benchmark on future innovation.”