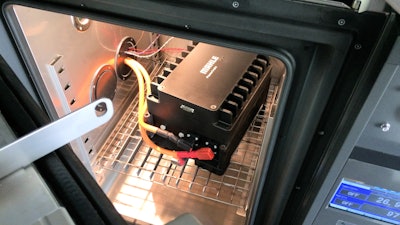
As a response to the growing time and cost pressures facing vehicle manufacturers seeking to develop latest generation electrification technologies, MAHLE Powertrain has opened a new, dedicated facility for the extensive testing of battery modules. The facility, based at the powertrain specialist’s Northampton technical center, enables the strip-down and disassembly of modules and compact vehicle batteries for post-test assessment, and provides a climate-controlled environment to carry out real-world simulated testing with the aim of streamlining the test and validation stages of emerging technologies.
“With electrification seemingly the automotive industry’s preferred method for achieving stringent future emissions targets, there is a very time and cost-sensitive need to develop enabling technologies such as the battery module,” says Simon Reader, MAHLE’s Director of Engineering Services. “The new facility has been carefully developed to provide an extensive capability that aids battery assessment, test and optimization. In-house development of such a facility would be time and cost-prohibitive for OEMs and so it makes perfect sense for MAHLE Powertrain, which can provide an end to end powertrain solution, to offer a broad range of expertise and capability that’s able to accelerate development time while reducing cost, in one place.”
The company notes it will also work with commercial vehicle manufacturers, many of whom are developing electric-powered vehicles and equipment, as well.
As well as offering post-assessment suitability analysis, the battery pack assembly and testing facility enables testing under simulated drive-cycle conditions to evaluate the performance of battery systems in real-use environments. Included within the testing remit is the ability to assess cells, modules and battery packs for steady state testing of open circuit voltage, storage capacity and thermal characteristics, including voltage response under high discharge, thermal behavior and internal resistance.
Assembly of new prototype units is also possible at MAHLE Powertrain’s new highly modular facility, which can conduct dynamic test cycles and steady state characterization testing with or without battery management systems in-situ. The facility can conduct tests within the temperature range of -40-100 C (-40-212 F) with precise humidity control and protection from a EUCAR 5 fire detection and suppression system. The remote-control chamber receives bi-directional power supply suitable for module testing with cycling software and control of the environmental chamber.
“The significant investment into this facility reflects MAHLE Powertrain’s commitment to providing our customers with services and solutions that are directly relevant to their requirements,” concludes Reader. “The needs of the automotive industry are evolving and by working with a trusted powertrain partner for testing or development work, OEMs are able to combat challenges while streamlining new vehicle development processes.”