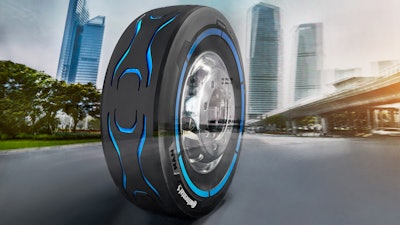
With autonomous and electric vehicles continuing to become more commonplace, their designs are impacting many components and systems including the tires. Research firm Smithers released a report earlier in 2020 examining the impact of autonomous vehicles on tires. It found tire materials and components, tire retail and tire marketing will be the most affected.
Smithers’ report went on to note tires for autonomous vehicles will:
- place a greater emphasis on durability, over handling and other performance criteria;
- accelerate the adoption of smart tires with sensing and reporting functions;
- see more use of low maintenance or planned tire monitoring platforms to manage fleets of shared AVs;
- demand lower weight tires to extend mobility, especially for electric vehicles.
Continental says with the trend toward automation, the impact of the driver on driving behavior and operational processes will become obsolete. As such, tire designs will need to evolve to account for these changes in driving behavior.
“Electric and autonomous vehicles are becoming more popular due to operating efficiencies,” says Ron Tatlock, Manager – Training & Engineering at BKT USA, Inc. “Designing tires for optimum tire and vehicle performance on electric and autonomous vehicles will help owners maximize the efficiencies and control the cost of operation.”
In the future, the design of and technologies used in machinery, including tires, will be even more tailored to their working environment.Continental
Special considerations based on vehicle type
Aaron Dahl, Chief Engineer Americas at GKN Wheels, says it is important to note design challenges raised by electric vehicles and those by autonomous vehicles are different and therefore require different solutions. Dahl says autonomous vehicles in general require wheels and tires that provide increased durability, strength, and longevity whereas the challenge with electric vehicles comes in the application of torque and the different demands this imposes on wheels and tires.
Julian Alexander, Product Line Manager Material Handling at Continental, notes the different requirements required by both vehicle types places great demands on tire manufacturers. Forklifts, for instance, are already electric and are quickly becoming more automated. Tires for these vehicles must be robust, heat resistant and durable, especially if automated Alexander says, because they are able to run 24 hours a day, 7 days a week which can create a lot of wear. However, electric vehicle tires must have as low a rolling resistance as possible. Alexander says these requirements are contradictory, making it integral for a tire manufacturer “to keep close relationships with the customers to understand their specific needs [and] keep coming up with the right fit for their vehicles.”
Tires for forklifts which are both autonomous and electric will need to meet contradictory requirements of high durability and low rolling resistance.Continental
READ MORE: Continental and MAN Present Tire Design for Electric Trucks
Tatlock says lower rolling resistance is an important feature for electric vehicles to help preserve the stored electrical energy on a vehicle—decreased rolling effort of these tires leads to a reduction in the amount of energy needed to move the vehicle. Minimizing the amount of energy used by the tires helps to ensure the vehicle can operate as long as possible before recharging is necessary.
Design considerations to minimize tread wear from tire to surface slippage when the vehicle begins to move is also integral for electric vehicles, says Tatlock. This is because electric drivetrains are capable of nearly instantaneous torque at the full motor power, eliminating motor ramp up or drivetrain slippage. The full torque of the drive motors is thus instantly applied to the tires which can increase the amount of wear they will experience over their lifetime. “Also, tire casings must be robust enough to handle this unthrottled torque,” he adds.
Tire slippage between tire and rim as well as tire and ground surface must be taken into consideration due to the increased amount of torque being placed on the tires of electric vehicles, says Gianpietro Bramè, Global and European Chief Engineer Wheels at GKN Wheels. This is already a common problem in the agriculture industry due to the increasing size and horsepower rates of equipment. As such, GKN Wheels developed its Profi-Grip wheel rim which has demonstrated the ability to eliminate tire slippage. “We are therefore confident that we have the experience, expertise and necessary tools to respond both to tire slippage, and to completely new challenges that the use of electric vehicles may present,” says Bramè.
Dahl says tire slippage will likely be an issue for electric vehicles in the construction industry as well. Both Dahl and Bramè say wider tire bead designs may be one of the methods used to overcome this. However, this will impact rim design, making it integral for tire, wheel and equipment manufacturers to work together to achieve the right design for an application.
Dahl notes wider tires and larger diameter wheels to help spread the torque could also be a solution to overcoming tire slippage. Increased torque application associated with electric vehicles may lead to challenges with bolted joints and disc designs, as well, which he again notes GKN Wheels has the knowledge and experience to help OEMs overcome. “It is possibly too early to know with certainty what all the challenges are which lie ahead in these sectors, but we are prepared and equipped to meet them, and our R&D team will work with OEMs, tire manufacturers and operators to develop and test appropriate and effective long-term solutions,” he says.
Tire slippage is a growing issue in the agriculture industry and will likely be a challenge with electric vehicles due to increased torque being put directly to the tires.GKN Wheels
Tatlock says autonomous vehicles will require robust compounding and overall designs with extra protection for tire sidewalls and tread. “The autonomous vehicle may not drive around a rock or other tire hazard or avoid hitting the [side of a] wall as consistently as a good operator,” necessitating a more durably designed tire. And because autonomous vehicles are running continuously, a special design may be required to lower heat generation and retention to avoid heat related damage.
Reliability and assurance of long-life performance are critical requirements in the design of wheels and tires for autonomous goods vehicles (AGV), says Bramè. “Standard wheels are simply unable to cope with this extraordinary operating environment and so our experienced R&D team worked closely with OEMs, tire manufacturers and port authorities to develop a solution to meet their needs, developing a wheel better able to cope with the increased stresses and so have significantly more resilience to fatigue,” he says.
This solution, the Infini-Forge wheel, is manufactured through a hot induction forming (HIF) process which makes the wheel 50% stronger and last 50% longer compared to conventionally manufactured, multi-piece wheels. The HIF process allows material to be placed where it is needed, and taken out where it is not, leading to an increase in rim strength without a significant increase in weight.
“Whereas traditional wheels would have a lifespan of some 37,000 hours in these challenging applications, AGV Infini-Forge wheels, with customized geometry, have demonstrated in field tests a lifespan in excess of 90,000 hours and so are considered to be a structural component of the machine,” explains Bramè.
In some sectors, like agriculture, the use of autonomous vehicles is more complicated due to the varied and less predictable environment in which the machine is working, says Bramè. Duty cycles are not necessarily as repetitive as those of other applications, such as port or surface mine operations, and he says it is unlikely farmers will require 24/7 operation. As such, the challenges for agricultural autonomous vehicle tires and wheels may be different.
“Although we have a good understanding of what the issues are likely to be in [the off-road equipment] sectors, to fully understand each market’s requirements, we will continue to work closely with OEMs, tire manufacturers and end users to make sure we develop solutions that are right for each of them and put the solution through its paces in field tests,” says Bramè.
More monitoring tools will be necessary to ensure optimal performance of tires in various applications.Continental
Smarter tires will be essential
Reinhard Klant, Product Line Manager Earthmoving at Continental, says autonomous equipment in the earthmoving sector is often operated in a convoy to increase efficiency and enable smooth processes. However, if one of the vehicles breaks down due to an issue with a tire or other system it will not only stop the entire fleet but also increase the risk of a collision. As such, it will become increasingly more important to use monitoring tools such as sensors which can send alerts to other vehicles as the problem occurs and thus prevent possible collisions.
The company’s ContiEarth tire range is one example of how intelligence is already being added to tires to improve operations. An integrated tire sensor alerts the equipment operator when pressure and temperature of the tire deviates from the norm. This helps to increase efficiency and safety by allowing fleets to better plan for maintenance and avoid costly downtime.
READ MORE: Smarter Tire Technologies
Dahl agrees the next stage of development for tires and wheels will be creation of more monitoring tools such as sensors capable of detecting cracks. “This technology will be invaluable in ports, but will also help unlock the potential for autonomous vehicles in sectors such as underground mining, where the risk of a vehicle failing 3 mi. (4.8 km) underground is an obvious barrier to their introduction in these environments,” he says. “Clearly if preventative maintenance can be accurately predicted, then vehicles can be taken to the surface at the right time, rather than waiting for a failure to occur.”
ContiPressureCheck features a sensor embedded in the tire to monitor tire performance and issues alerts on an in-cab display.Continental
Continental says that in the future, the design of and technologies used in machinery will be even more tailored to their working environment. Demands for a more sustainable world will also continue to increase. Because of this, tires of the future will be intelligent, sustainable and environmentally friendly. “The tire of the future will therefore need to be as efficient as possible in order to save fuel and emissions,” says Continental. “At the same time, it will have to be made of recyclable and biodegradable materials.” (See sidebar below.)
In general, manufacturers agree that traditional tire and wheel designs will not be able to meet the requirements demanded by autonomous and electric vehicles, so new solutions will be needed. “Rather than being completely new designs though, these new [tires and] wheels are likely to be evolutions of existing technologies, both product and process, building on the benefits of proven solutions in use globally to respond to the needs of these new machines,” agree both Bramè and Dahl.
“BKT expects to see more of these vehicles appearing in more diverse applications as the technology and ingenuity of equipment designers continues to grow. We are ready for the challenge,” concludes Tatlock.