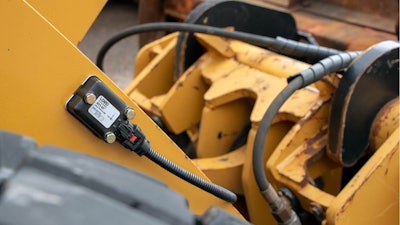
It’s no secret that manufacturers of off-road heavy-duty vehicles and machinery face unique challenges in ensuring not only equipment functionality, but operator comfort, productivity, and performance as well. As OEMs look to meet these needs, there is a greater emphasis on incorporating enhancements within their product lines to help them do so.
For years, inertial measurement units (IMUs) have allowed various industries to measure the angular rate and orientation of the object—either a vehicle or robotic equipment—that the unit is attached to, providing important data that enables the accurate control of the object’s performance. But beyond just controlling performance, this information leads to increased operator safety and productivity by setting limits or parameters on what the equipment can or should do. In the off-highway industry, this information is especially important. Both operators and the equipment are exposed to a variety of environments, as well as other conditions, that could make productivity difficult. Safety considerations are also an issue.
Choosing the right IMU sensor to provide accurate, real-time information is critical. But how do you determine which sensor will provide that reliability, all the time? The answer is pretty straightforward: You start with accurate testing based on real-world applications.
Not all testing is created equal
Off-road, heavy highway OEMs need to engineer products that can operate in both dangerous and unpredictable conditions. Sensors are meant to help compensate for those unknowns and provide valuable information that will prolong the lifespan of the equipment itself, as well as ensure the operator’s safety. It would make sense, then, to test the reliability of sensors in as close to real-life conditions as possible.
Too often, if sensors are tested at all, it’s done within a laboratory setting, which does not account for real-world application variances. As a result, the sensor does not live up to the standards indicated on the spec sheet and the OEM is left integrating a device in its product line that provides inaccurate measurement. The sensor can be replaced—as is often the case. But the time lost, or worse yet, jeopardizing the operator’s safety, is not a risk worth taking for most OEMs, or their customers.
“Testing has a direct impact on a manufacturer’s ability to produce a better-quality product and an optimal customer experience,” says Justin Bessette, Technology Manager, Parker LORD.
Relying on “what-if” laboratory testing can leave OEMs stranded, literally and figuratively. In general, you will never get the same kinds of results you’d get from real-world applications compared to testing results derived from a lab test. “There is really no way to understand the end result of combining various attributes without actually combining the various attributes,” Bessette says. “In a lab environment, you are typically testing one attribute at a time, sometimes two. In the real-world environment, the sensors will be subjected to everything at once.”
Testing MicroStrain inertial sensors against a competitor sensor, the chart shows the sensors being subjected to a random vibration profile of approximately 8G RMS. The ML5 and MV5 are orders of magnitude more stable than competitors when used in real-world environment that includes vibration.Parker LORD
The testing sweet spot: why it matters
In the off-highway industry, there are two critical considerations in keeping equipment functioning and operators safe—vibration and environment. Vibration is inherent in construction equipment, there is no way around that. The IMU sensor needs to be able to isolate that movement, and instead measure the position of the object that it is attached to. Otherwise, it will produce an inaccurate reading. Also inherent in the off-highway industry is the variety of environments in which the equipment will operate—everything from hot and cold, to rain and mud and dust. The sensor needs to be able to work in many different environments without malfunctioning.
If tested with these variances in mind, an IMU sensor can provide accurate, reliable data that can stabilize the equipment no matter the environment, no matter the job. Stabilization leads to operator safety as well an extension to the vehicle’s life expectancy. Both very important considerations for not only OEMs in the off-highway industry, but their customers as well.
“By working with customers, we were able to determine the exact environmental and performance tests that the product needed to be tested for as well as external certifications,” Bessette says.
In developing the MV5-AR and ML5-AR industrial tilt and angular rate sensors, the Parker LORD MicroStrain team did just that. They relied on real-world environments and conditions to gain an accurate reading that helped validate the performance of their devices.
Closeup of MicroStrain MV5-AR inertial sensor.Parker LORD
Setting the real-world bar for testing
To understand in-demand needs and expectations, one needs to go directly to the source. The MicroStrain team worked with several OEMs in its research for testing standards. As a result, they have more than 56 third-party qualified standards which include electrical, mechanical, vibration and environmental standards.
“We asked specifically about use-cases as well as the types of standards, whether environmental or otherwise, the OEMs wanted us to include,” Steve Mundell, Business Unit Manager, MicroStrain says.
The team then recorded data from real-world machines and equipment—both vibration and environmental data—and simulated those conditions in their test environment in a repeatable way to make sure the IMU sensors are designed to meet those very specific challenging conditions.
To really put the sensors to the test, they were then put toe-to-toe with those of competitors. “A lot of competitors test parts in a cookie-cutter format, but getting the true performance of a sensor is going to lead to a better-quality product,” Mundell says. “With these comparative tests, we were looking to show accurate readings in real-world conditions to validate the performance of our devices.”
The team placed its sensors, again in real-world environments, alongside its competitors’ sensors, then analyzed the data using measurements gained from that placement. First, in a high-vibration test, three sensors—MV5-AR, ML5-AR, and that of a competitor—were subjected to a known input vibration, which was collected through real-world field data. The goal was to introduce real-world occurrences during the testing phase while recording angular measurements.
Testing MicroStrain inertial sensors against two competitor sensors, the chart shows the sensors being rotated +/-90 degrees in pitch. The MV5 and ML5 performed several orders of magnitude better than some of the competitors.Parker LORD
A perfect sensor would have an angular measurement reading of 0 degrees. There is no such thing as perfect, but the two MicroStrain sensors showed a reading of near zero, while the competitor’s outputted a reading of 20 degrees. The competitor’s sensor was tracking rotations that it was, in fact, not being subjected to and therefore recording an inaccurate reading.
In the second, the pitch error test, the team took to task four sensors—MV5-AR, ML5-AR and two competitors’ sensors. All devices were rotated through the usable measurement range with the goal of showing a minimal difference in reported angle for similar angle readings.
An ideal sensor would have no error throughout this range, but the team saw significant errors on both competitors’ sensors, whereas the MV5 and ML5 showed minimal errors during this test.
The results for both tests were clear: conducting tests using real-world applications produced a better-quality product, bar none. “We’ve been doing this longer than almost everyone,” Bessette says. “We know and understand all the idiosyncrasies that go into designing a product that can be trusted. The point is to accommodate those idiosyncrasies upfront and produce a more reliable product, than to try to solve problems in the field or fix something when it fails. We don’t want it to fail.”
Sensors in the field, on the job
Knowing you have a product you can rely on is just part of the equation. Knowing you have a product that will work with your equipment and that you can confidently put your name on is just as important. OEMs want to know that the sensors will fit their needs now and in the future.
“Our field engineers will meet with the OEMs to help with process and integration, which at the end of the day, is just as important as the reliability of the product itself,” Mundell says. “The sensors are all interchangeable and customizable, making them an ideal solution for any customer need.”
The MicroStrain team will continue to test all its products in real-world environments and account for any changes in standards or customizations that require more work. It took about four months to qualify the first 56 standards it tests its products to, but that’s not the end of the line. “Some tests involve accelerated life testing, so with those we may try to simulate the unit for 10 years of wear and tear,” Bessette says. Real-world testing of sensors like the MicroStrain MV5-AR inertial sensor ensures accurate validation of sensor performance.Parker LORD
Every product that ships is 100% tested and calibrated to current qualified standards. “We learned a lot through the testing process,” Bessette says. “Some things even surprised us. For example, we determined that the torque limiters for the screws needed to be larger than our competitors. Our customers preferred to be able to use standard bolts that are used elsewhere and to be able to apply significant torque without damaging the sensor.”
Although a minor difference, the result is huge when it comes to customer satisfaction. At the end of the day, providing a sensor that will not only meet the customer’s specific needs, but also surpass their expectations is ultimately what separates one brand from the other.
“We have a high-performance sensor. We’re able to support extremely high-volume manufacturing, as well as provide personal support on a micro level,” Mundell says. We’re a good partner in both the design process and design phase all the way through the different levels of production.”
This article was contributed by Jody Dunklee, Field Applications Engineer, MicroStrain, a division of Parker Lord.