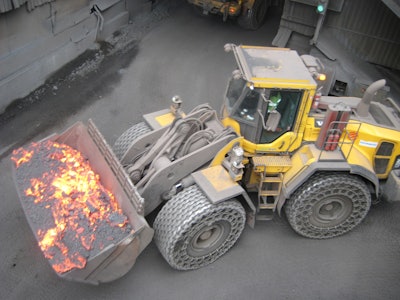
Of course, there is no disaster and what appears to look like molten lava is actually liquid slag – a glass-like by-product from melting scrap metal. Global steel mill service company, Harsco Metals, extracts the slag in liquid state at an incredible 1,300 C from its foundry in Mo i Rana, Norway, on a daily basis – making it one of the harshest working environments for a wheel loader imaginable.
Underneath the steel furnace in a narrow tunnel, workers tap out about 10 cubic meters of slag every 40 minutes, while constantly feeding the furnace with scrap metal. There is a tight turnaround between loads so machines need to work in pairs. With loads of such a high temperature, the machines stand 20 meters apart in case of a fire or an explosion.
“Safety is of the utmost importance on a site like this,” explains Ronald Utland, site manager of Harsco Metals Norway. “Our workforce undergoes rigorous training on an ongoing basis, and we make sure they have the safest equipment and protective clothing.
“We take every precaution to avoid explosions on site,” says Ronald. “But if one were to occur, it’s essential that our equipment can withstand the blistering heat and keep our operators safe in the event of a blast.”
The site currently operates a specially-modified Volvo L220F and two L220Gs that have steel plating fitted to the front and underneath of the machine for heat proofing and thermal protection. Volvo Construction Equipment (CE) and its local Norwegian dealer, Jern & Maskin AS, have worked with Harsco to provide special slag handling equipment since 2000. Next year Volvo CE will launch the new slag-handler application L220G – its first factory-ready slag handler.
Harsco has already purchased three L220G machines with pre-series options for slag-handling applications for use in Norway and Sweden. The machine will be available with 40 different options – straight from the factory – to make it suitable in the extreme temperatures of slag handling applications. The front windscreen is made of bullet-proof glass to stop the glass shattering into the cabin, and the frame is also reinforced to keep the window in place. Further modifications include a reinforced windshield and fire-protective material throughout.
“In the past we’ve experienced big problems with tires,” Ronald explains. “They would often catch fire or melt, and the average lifetime was just 450-650 hours. Now we use metal chains around the outside, which cause wear but they’ve increased the lifetime or our tires to around 3,000 hours.”
The machines each work four 24-hour shifts per week and the site shuts down for just 48 hours over the weekend. The rest of the time the wheel loaders are shifting the molten slag a distance of 60 meters to lay it out for cooling before it’s loaded onto dump trucks and taken for crushing.
“Buckets are a big problem for us,” Ronald admits. “Finding steel that doesn’t change structure when heated to more than 700 C is difficult, but essential in our business. We are currently trialing a new range of buckets made using more high tensile steel that could improve the durability compared to other buckets by up to three times.”
The slag is a valuable and useful by-product of smelting ore, Ronald says: “Unlike other industrial by-products, slag actually has many uses and rarely goes to waste. It can appear in concrete and aggregate road materials, to add a bulk consistency to the mixture. Harsco is very aware of its duty to care for the environment and recycling is one way to ensure materials do not go to waste.
“We have been working with Volvos for many years at our sites across the world,” Ronald continues. “The machines use less fuel and are easy to operate – two essential features in our working environment.”
Harsco Metals was established in 1953 when it was known as the Harris Steel Corporation, and in 1956 the Harsco Corporation was formed. Operating at 160 metal production sites in 30 countries, Harsco is one of the biggest service providers for steel industries in the world. Its local Volvo CE service provider, Jern & Maskin AS, is supporting the machine fleet to maintain uptime in this severe environment.