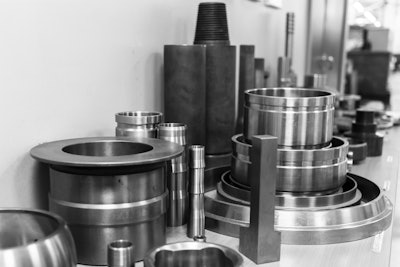
Nanodiamond material specialist Carbodeon of Finland has worked with metal finishing specialist CCT Plating of Germany, to develop a new NanoDiamond enhanced electroless nickel plating with significantly improved performance in sliding applications.
Electroless nickel coatings offer many advantages over other coating types, such as excellent corrosion and abrasion resistance, creating an even coating thickness over complex geometries and at relatively low cost. A limitation to their performance has been that they don’t perform well in tribological applications involving moving metal parts, where adhesive wear and galling tend to lead to rapid wear or failure.
Incorporating Carbodeon NanoDiamond into the coating solves this problem. Spherical diamond nanoparticles are specially treated to make them disperse in coating liquids and carry a positive electrical charge on their surfaces. In the plating process, the diamond particles behave similarly to positively charged metal ions and together with the coating material they co-deposit onto the component.
Metal-diamond composite surface treatments have already shown their value in abrasion resistant coatings, but in this latest generation of coatings the process has been optimized to better combat adhesive wear, which occurs mainly when the plated parts are in sliding contact with other metal parts.
Key performance characteristics are:
- The coating significantly reduces adhesive wear, but does not make the coating abrasive or increase the surface friction.
- The coatings can be used “as plated” which does not affect the substrate’s heat treatment condition, or can be subjected to annealing for maximum performance.
- Wear rate is reduced by 30% “as plated” and by up to 85% in the annealed state.
- The annealed version has two to three times the durability of standard annealed coatings.
- The coating hardness is significantly increased especially when annealed – reaching a maximum Vickers hardness values of 1030 Hv.
- The process contains no hexavalent chromium and so is environmentally friendly and free of complex regulations.
- Low diamond content makes these coatings affordable.
Target applications include anything which experiences sliding wear, including the automotive, printing, textile manufacturing and oil & gas industries.
The nanomaterial for the process can be obtained from Carbodeon who can also implement the complete plating process in existing customer plating facilities. Alternatively, job plating or turnkey solutions can be carried out by CCT Plating in Stuttgart, Germany.
Carbodeon has patented the nanodiamond material and the plating application.