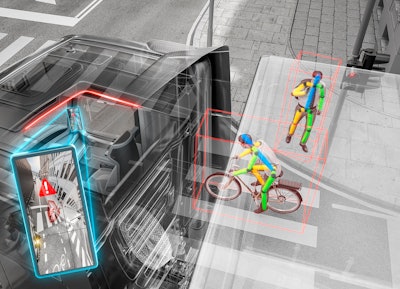
Use of proximity detection systems continues to increase as manufacturers look to improve safety and work toward further automating vehicle operations. These systems help increase visibility around a vehicle or piece of heavy machinery by alerting drivers of any obstacles—stationary objects, people or other vehicles—in their path. And in some cases, the system can even take corrective action, such as braking the vehicle, if drivers do not do so themselves.
Jon Morrison, President of the Americas, WABCO, says it was a big jump forward in the industry when it began integrating onto vehicles its radar-based forward collision mitigation system, OnGuard, capable of monitoring and mitigating speed differentials between two vehicles as well as braking independently of the driver. “Fleets have reported up to an 87% reduction in rear-end collisions from deployment of that technology,” he says.
While forward collision mitigation systems have greatly increased vehicle safety, further safety improvements can still be achieved, especially when it comes to the side and rear of a large vehicle. Because of this, side object detection and blind spot systems have gained acceptance within the industry, particularly for heavy-duty on-highway vehicles. Historically they have had a lower adoption rate says Morrison “but we see that increasing now as we see more of a tie-in to a system approach.” An illustration of a heavy-duty truck's blind zones.PRECO Electronics Inc.
“We think [these blind spot systems have] a high potential for mitigating limited vision crashes which account for approximately 20% of all truck initiated crashes,” he notes.
Tom Loutzenheiser, Vice President of Business Development at PRECO Electronics, says the company has seen the need for blind spot detection and side-turn assistance systems become more prevalent over the years, and that it has become an option on various types of equipment throughout heavy-duty industries. Market drivers for these and other types of proximity detection systems are being driven by regulatory entities as well as companies looking to establish safer operations, save money and improve efficiency, he says.
He adds that these systems continue to advance with the adoption of similar technologies within the automotive industry. “The significant difference these technologies make in automobiles is understood and accepted, making their importance [and] adoption within the heavy-duty industry mainstream,” adds Loutzenheiser. “Unfortunately, the deployment is still in process.”
Creating smarter systems
According to Morrison, blind spot and side object detection systems are using similar, if not the same, technologies as other types of proximity detection systems, as well as following many of the same trends, such as creating more integrated systems. The systems can be radar (Radio Detection and Ranging) or lidar (Light Detection and Ranging) based, and may or may not make use of a camera. For its OnSide blind spot system, WABCO uses a radar sensor technology that can discern whether a moving vehicle or other type of object is in the blind spot and warn drivers of potential collisions. It’s also good at operating at lower speeds—anything above 15 mph (24.1 kph)—a level at which the radar sensor is able to function accurately. “We feel that’s really an advantage right now with the radar technology, which is also reliable in low visibility conditions such as rain or snow,” says Morrison. “It basically sees through all of that, whereas sometimes lidar—which is a light-based detection system—could potentially be affected by weather and other environmental factors.”
For its Backsense radar obstacle detection system, Brigade Electronics Inc. uses Frequency Modulated Continuous Wave (FMCW) technology. Corey Heniser, CEO of Brigade Electronics Inc., says it transmits a continuously varying radar frequency signal with unique time stamps to each instance of the wave. “The time of the returning wave is referenced to the stamp without the radar needing to pause transmitting,” says Heniser. “This gives more accurate detection than alternative radar products using Pulsed Radar technology that transmit a single burst of radar and then listen for the returning wave.”
He explains this is because FMCW radars are continuously transmitting a signal whereas with pulsed systems a delay in measurement updates can be experienced. And because of the short wavelengths, FMCW radars function well in all types of weather conditions and environments.
Morrison notes the industry is starting to see more of an integration of radar and camera, lidar and camera, and even radar, lidar and camera into proximity detection systems. These technologies are all coming together “to get a more accurate picture of what’s happening around the vehicle, and are building blocks for more independent or autonomous function.”
Combining an object detection sensor with a camera can be beneficial for increasing visibility for operators, and is especially so when operating at lower speeds. “The challenge with lower speeds is that you can get vehicles that are running in parallel to each other at the same speed, [and] you have a tendency to potentially lose that speed differentiation that you need. Therefore, combining for example the side object detection with a camera can give drivers confirmation that another vehicle is present,” Morrison explains.
Also helping make object detection systems smarter is the ability to integrate them with other systems on a vehicle. Originally designed as an OEM solution for heavy-duty on-road vehicles, PRECO’s PreView Side Defender is a system which is integrated with the vehicle’s CANbus to detect objects that may be in a vehicle’s side blind spot and alerts operators of them when making turns or changing lanes. The system provides a 150-degree viewing angle and detects moving objects—such as cyclists and cars—while having the ability to filter out stationary objects.
The company will soon be releasing the fourth iteration of its PreView Side Defender optimized for the aftermarket through the integration of speed monitoring into the system without having to attach it to a vehicle’s CANbus.
This enables it to still detect objects in a vehicle’s side blind spot at high and low speeds while easing installation. “Within the trucking industry, a large percentage of fleets are now sending telematics, connecting motes to the Cloud, keeping track of speed, etc. This solution was created because newer trucks have body-builder-CAN gateways built in, and in-use heavy-duty vehicles do not,” explains Loutzenheiser. “This change made the system a powerful and affordable option, with additional ease of installation for retrofitting.
“Using the information gathered through the CANbus, our technology is able to ignore stationary objects based off of the selected detection zone, the speed of the machine/other objects, and proximity detection,” says Loutzenheiser.
Having the ability to filter out non-threatening stationary objects and alert operators only when necessary eliminates nuisance alerts and false positives, an important factor when designing object detection systems. “If there’s anything that’s a major complaint or dislike for drivers, [it’s] when a collision mitigation technology suddenly comes on by itself,” says Fred Andersky, Director of Marketing and Customer Solutions, Controls, Bendix Commercial Vehicle Systems.
The addition of a J1939 CAN connection to Bendix's BlindSpotter enabled the company to make its radar sensor smarter and expand the system's field of view.Bendix Commercial Vehicle Systems
“A [total] distance length of up to 40 ft. (12.2 m) means we now capture more of the front of the vehicle and more down the trailer at higher speeds where you’re more likely to have a potential issue for a lane change or something in your blind spot.”
Knowing the speed of the vehicle and being able to change the detection system’s field of view based on that is valuable in some types of situations. In yard applications, for instance, because vehicles are moving slower operators have more visibility and so a wider field of view for the detection system isn’t necessary like it would be for highway driving applications. Having a smaller area of coverage also means the system is less likely to detect things in the yard which may not be threats, and thus reduces false alerts.
Data is another benefit of adding the CAN connection. At some point in the future Andersky says it will be possible to collect data from radar. “Being able to fuse the information from that radar on the side with what we’re seeing at the front of the vehicle helps avoid more types of collisions,” he says. This will help to further the amount of coverage around the vehicle in order to avoid more types of collisions.
Building blocks to autonomy
“For full automation, perception systems are needed,” says Loutzenheiser. “Combining multiple sensor systems to offset deficiencies is key, and redundancy within sensor fusion is essential.
“In a perfect world, this highly accurate perception system would be combining multiple sensing technologies, with all of their own strengths and weaknesses, in which strengths offset weaknesses so they are each stronger when together.”
Smarter sensors and the continuing evolution of sensor fusion—more sensors working together to deliver higher levels of performance—will be the way to achieve this move toward full autonomy.
By integrating what were once stand alone or closed system sensors into the vehicle network they are able to do more in more situations. “The basic benefit that we get [with sensor fusion] is, when you make a decision isn’t it better to have more than one source of information? We’re now providing more sources of information into the system, so the intelligence in the system can figure out what’s going on faster and make a decision quicker on what needs to be done to alert or help the driver mitigate the potential situation,” explains Andersky.
Having more information going into the system reduces false alerts because now information from different sensors can be cross checked. This is especially important as more automated features and eventually fully autonomous operation is added to vehicles. “The more automation that gets involved, the higher level of crosschecking and validation or verification there needs to be,” he says.
While providing a platform for future designs, benefits of improved safety and automation of some vehicle functions are already being seen through the integration of sensors and systems.
WABCO’s OnSide, for example, provides a warning sound when it detects an object in a driver’s passenger side blind spot. When integrated with the company’s OnLaneASSIST active steering system, it provides both an audible alarm and commands the steering to take action independent of the driver. Morrison says this enables the driver to get back on track and re-engage with the vehicle. “We see that technology coming out in 2019, and something we think that’s going to be highly attractive to the commercial vehicle world because of the issues that can be overcome.”
Being able to create systems like these today which are capable of taking action on behalf of the driver are a key step in ensuring the fully autonomous vehicles of the future know how to recognize objects and make the right driving decisions when necessary.
An illustration of the various alerts and connectivity possible with today's obstacle detection systems.PRECO Electronics Inc.