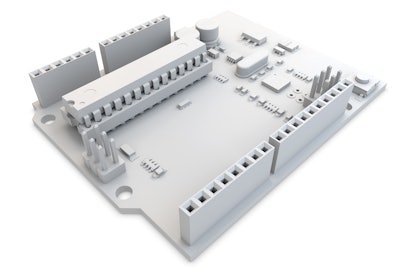
As interest in and availability of products for the internet of things (IoT), autonomous vehicles, 5G cellular networks, smart cities, and video-streaming services increase, the need to be able to push far greater quantities of data through often much smaller wired and wireless devices at much higher speeds becomes more important and challenging. To assure high-quality as well as high-speed data transfer, all components used in electronic interconnects are being scrutinized to minimize signal loss/decay, distortion, and interference. Often that necessitates that manufacturers upgrade performance of high-speed connectors, which, in turn, has led to the development of three new grades of high-performance liquid crystal polymers (LCPs) from Sumitomo Chemical Advanced Technologies LLC to meet the increasing demands of this segment.
Trends in device miniaturization (and connector miniaturization and sub-miniaturization with requirements for comparable or higher mechanical performance in thinner wallstock) plus use of higher density interconnects have reduced space and increased complexity on printed circuit boards (PCBs). At the same time, the market is pushing for significantly faster transmission speeds — from 3, 6, and 12 to 25, 50 and even 100 gigabytes per second. Putting so many high-speed, high-frequency interconnects in such close proximity increases transmission loads and, along with it, crosstalk, which increase the need for connector materials with lower dielectric constants and dissipation factors. Crosstalk between mobile phones is annoying; crosstalk between autonomous vehicles could prove deadly. Regular stories about high-profile website hacks is a constant reminder of the need to protect data integrity without impacting signal speed. Additionally, faster processing speeds and higher circuit density with lower profile, thinner connectors make thermal management a more pressing issue, which has increased thermal requirements for materials used for interconnects. To prevent data bottlenecks, manufacturers will need to continually upgrade connector performance to assure more reliable data transmission with greater clarity.
In order to better meet the changing needs of connector manufacturers, Sumitomo Chemical has developed three new SumikaSuper™ LCP grades specifically designed for high-speed connectors, including backplanes and automotive connectors for infotainment. SumikaSuper E6205L (available in natural and black) is a lower dielectric constant polymer that is ideal for connectors requiring higher data transfer speeds. However, for connectors that require both a lower dielectric constant as well as a lower dissipation factor (lower loss tangent), a unique LCP with a different chemical structure called SumikaSuper SR1205L (available in natural and black) may better meet requirements depending on connector geometry and design. For high-speed digital and wireless devices where electromagnetic interference (EMI) is a concern, owing to its deterioration of signal quality, a third grade, SumikaSuper SZ6911EM (available in natural) has been specifically designed to provide EMI shielding. This grade incorporates ferromagnetic particles that convert incident EM waves into heat energy, which subsequently can be bled off by thermal management systems. Each new grade benefits from Sumitomo Chemical’s polymer synthesis and compounding expertise.
LCPs are a family of polymers that produce thermoplastic parts with unique processing characteristics and extremely high performance, so they are commonly used to replace metals, ceramics, and other plastics due to high thermal resistance, excellent flowability, and opportunities for weight or wallstock reductions. Most commercial LCPs are aromatic polyesters characterized by high thermal and mechanical performance, inherent flame retardancy, good weatherability, excellent electrical properties1, high resistance to stress cracking, and chemical inertness.2 This makes them ideal for use in electrical and electronic components (including fiberoptic cables, PCBs, chip carriers, connectors (conventional, radio-frequency (RF), and fiber-optic), and other surface-mount components), microelectromechanical systems (MEMS), automotive applications (including components for ignition and transmission systems, lamp sockets, pump components, coil forms, and sensors), printer/copier/fax components, cookware, high-barrier/retort-processed food containers, plus components for chemical processing (including pumps, meters, and valves).
Commonly processed via injection molding, LCP parts can be joined via thermoplastic welding techniques, particularly ultrasonic and laser welding. Owing to the highly rigid structure of their molecular chains and their liquid crystalline nature — which tend to be nearly linear and to occupy a stacked orientation that maintains its order regardless of solid or liquid phase — LCPs are highly anisotropic. Essentially, primary bonds within an LCP polymer chain are highly attractive and hard to break, while secondary bonds between molecular chains are weaker and much easier to break. Although most thermoplastics and especially fiber-reinforced thermoplastics exhibit some degree of anisotropy after processing, the molded properties of LCPs can be significantly different in flow and cross-flow directions3, which requires some care when designing parts and tools for these polymers to take advantage of (and avoid the challenges of) this characteristic.
The highly ordered and linear nature of these molecular chains provides LCPs with self-reinforcing properties in the flow direction and contribute to excellent mechanical properties. However, LCP’s high anisotropy also means that weldlines (where flow fronts with different molecular orientations converge) are weaker and thus prone to warpage and thermal-expansion differentials. Because of this, LCPs are typically reinforced with glass fiber and mineral fillers — not so much to increase stiffness and strength but to reduce anisotropy. Warpage can be reduced with proper gate design in the injection molding tool. Because of their high performance, LCPs are priced accordingly. However, given their high melt flow rates, fast setup times, and low thermal expansion in the direction of flow, these polymers can be formed into thin-wall parts with short molding cycles that deliver high performance at low mass and lower material usage — all of which help offset higher initial material costs. (They also can be molded into large, thick-walled parts.) The thermal stability typical of LCPs enables processors to efficiently reuse regrind and recycle reject parts, which again reduces material losses and lowers effective part cost.
Depending on design and thickness requirements of a given connector program, Sumitomo Chemical can offer a suitable LCP grade. The company has been producing polyester-based LPCs since 1972 and provides dozens of compounds as well as alloys with other high-performance thermoplastics like polyethersulfone (PES) to meet a wide range of mechanical and thermal requirements (from 260-360 C). In addition to high-quality material, the company also is known for its first-class technical support — from part design to on-site molding assistance.
1 Electrical properties include high electrical resistivity, low relative dielectric constant, and low dissipation factor.
2 Resistance is excellent to strong and weak acids, alcohols, esters, ketones, and aromatic, chlorinated, and halogenated hydrocarbons over a broad range of temperatures. Hydrolytic stability in boiling water also is excellent. LCPs can be attacked by high-temperature steam, concentrated sulfuric acid, and boiling caustic chemicals. A more comprehensive treatment of the chemical resistance of LCPs is shown in Table 1 on the company's website.
3 It has been reported in the literature that anisotropic-dependent properties (e.g. tensile strength, coefficient of linear thermal expansion (CLTE), and elastic modulus) can be up to 3x greater in the flow vs. cross-flow direction. LCPs also have a high Z-axis CLTE.